Tips to improve grinding profitability with mill liners
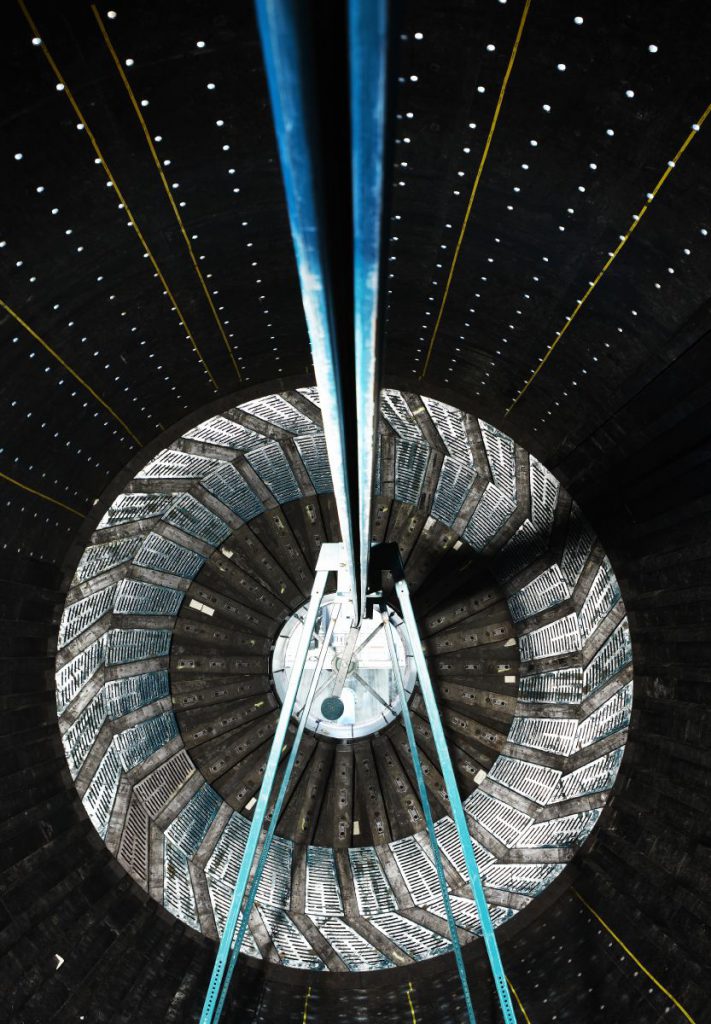
When the grinding mill turns, it is the mill lining’s job to grip and lift the charge to create the desired charge motion and ensure that as much of that energy as possible is transformed into efficient grinding. We started off with the tips on improving grinding profitability already in our first blog post and cover now the remaining two aspects: optimized design and maintenance.
4. Optimized grinding mill liner design
A mill lining should be optimized by design in order to minimize problems, utilize the mill’s capacity and keep a good liner profile throughout the wear life. This can be done by maximizing the efficiency of the grinding process.
It is important to control the charge motion to ensure that as much of the impact, attribution and abrasion takes place on top of and inside the charge. If there’s too little charge motion, there won’t be enough energy to grind the ore; and if there’s too much charge motion, there’s a risk that a lot of energy turns into liner and media wear, heat and noise. If the liners are subject to direct impact, there is also a big risk of liner breakage.
As a mill liner wears, it typically becomes less profiled and at some point, it loses its capability to provide enough lift to create the correct charge motion. By optimizing the design, it is possible to minimize these effects. Our Poly-Met liner concept retains an efficient profile, similarly to metallic mill linings, as different types of wear-resistant inserts are used in combination with impact-resistant rubber.
Mill liner design trends – then and now
The old-fashioned high-high design of tight space, created for maximum wear life, used to be very common. But the simulation tools that are available today demonstrate that these old designs are not very efficient. They occupy too much volume, they do not agitate the charge properly, and, at the same time, they might be too aggressive and cause the charge trajectory to be too high.
The current trend is to go for a wide-space design to prevent packing and to utilize the mill volume to the highest extent possible. It is really important to make a design that promotes the optimum charge motion to prevent the liners from being impacted by the media and ore, and at the same time to make sure that the efficiency is as high as possible in order to save energy.
A high-low design is one way to improve the performance in a mill with a tight-spaced drilling pattern. However, that does require more frequent maintenance, as you need to replace every second row twice as often. A more modern design is the wide spaced, one-shot design, where everything can be replaced at the same time, minimizing the number of maintenance stops.
Discharge system optimization
The discharge system is another area with potential for optimization. In a single rotation mill, a curved discharge system ensures that the pulp is discharged in an efficient way instead of flowing back into the discharger, causing wear. This is also a way to prevent pooling. With mills becoming larger and larger with higher throughput and the production targets constantly increasing, it has become more and more important to optimize the design to be able to utilize the mill’s full capacity.
5. Well-organized maintenance of mill linings to finish up efforts towards better profitability
Every mill stop, no matter how short, causes costs, so the number of stops should be minimized. Often, the mill has to be at least partially ground out, water might have to be pumped out and the mill properly washed out to ensure that all the trapped ore or other particles are removed so that the mill can be entered safely. Some mills are quite hot or the process can contain gas or fumes that must be vented out, and the pH value in some mills makes the environment less friendly. Finally, relining takes time; and even after everything is done, it takes a little while before the mill is running at full capacity again.
One way to avoid extra maintenance stops is to ensure that the liner wear life is in balance, i.e. as many parts as possible should have the same wear life. If the plan is to have two major maintenance stops every year, the liners should last 6, 12, 18 or 24 months to minimize the need for intermediate stops.
The correct lining reduces maintenance time
It is crucial to carefully study the wear pattern inside the mill. It is a good idea, especially with a new design, to measure the liners more frequently to determine if the wear is linear or if it accelerates in certain positions or at some particular state of wear. Once the wear pattern is known, the design can be changed accordingly…
Read the entire article on metso.com: Five tips on mill liners to improve grinding profitability 2/2.
{{ commodity.name }}
{{ post.title }}
{{ post.date }}
Comments