Grinding down energy consumption in comminution
Smart miners are investigating new techniques and technologies in order to improve the energy efficiency of their comminution circuits.
Increasing demand for metals and minerals coupled with declining ore grades mean that, in order to maintain their output, mines must process ever larger amounts of material and expend an increasing amount of energy to do so.
In tandem, global energy costs are rising, very quickly in the case of some countries, and so to ensure profitability and keep their operations economically viable, miners are looking at different ways to optimize energy consumption throughout the mining process.
According to the Coalition for Eco-Efficient Comminution, comminution – the process of crushing and grinding ore – is by far the most energy consuming step in the mining process. It accounts for around 53% of mine energy consumption which equates to at least 10% of production costs. In comparison, leaching and absorption, the next biggest energy consumers, take up 22% followed by excavation and hauling at 10% and drilling and blasting at 2%. And comminution isn’t just a major energy sink within the mining process; it accounts for 3% of the total amount of electrical energy consumed globally.
Metso’s director of process engineering development, Alan Boylston, put this into perspective in a 2017 report detailing his outlook for the mineral processing sector over five years.
“In 2012, the world generated about 21,600TWh of electricity,” he said. “Three percent of this is 648TWh. Based on the current fuel mix in the US, this equates to nearly 400,000kt of CO2 every year, and at 10 cents per kilowatt-hour, the total cost of comminution power in the global mining industry is about US$65 billion per year. This is more than twice BHP’s gross revenue in 2016.”
Improving the energy efficiency of comminution is therefore key for miners that wish to remain competitive on the global stage and, given the potential scale of impact, reducing their energy intensity is also a big factor in allowing miners to maintain their social license to operate.
However, rather than looking at this purely as a challenge that must be overcome, smart miners are also viewing it as an opportunity; energy costs may pose a significant danger to their bottom lines, but the potential monetary savings that can be created by employing eco-efficient processes and technologies can run to millions of dollars a year.
One way of tackling this is to design energy efficiency into the mining process from day one using techniques such as in-pit crushing and conveying or sorting, smart blasting, preconcentration and better screening to reject gangue early on and reduce the energy needs of downstream processes, including comminution.
While this may make sense for some new projects and where operational conditions are favourable, it is not always an option, particularly for mines that have been running for some time. In these cases, another, less capital-intensive option is to select crushing and grinding technologies that naturally consume less energy, and to couple these with an intelligent control system that optimizes operating conditions according to ore characteristics and rate of throughput.
Next-generation grinding technologies in particular offer vast scope for improvement, and machines such as high-pressure grinding rolls (HPGRs) and vertical stirred mills that were introduced 30+ years ago are now slowly gaining more traction as miners look to tighten their balance sheets and improve their environmental stewardship.
With this in mind, let’s look at some of grinding technologies on offer and the results they can deliver.
A vertical improvement
Vertical mills are not new to the mining market. However, their potential as an energy saving tool has only been properly acknowledged in the past 10 years.
Products such as Metso’ VertimillTM and Stirred Media Detritor (SMD) can offer significant energy savings over traditional balls mills in grinding applications and, thanks to a lower capital cost, less media consumption and lower maintenance requirements, they can also provide a lower total cost of ownership.
Gravity-induced stirred mills such as Vertimill initiate a ball charge motion using rotational movement of a screw to provide a reduction in material size, while fluidized stirred mills like the SMD use a rotational movement to fluidize a media-slurry mixture, resulting in particle size reduction. The type of mill and circuit configuration used are essential factors in maximizing the grade and recovery profile of an ore, and so are selected on a case-by-case basis.
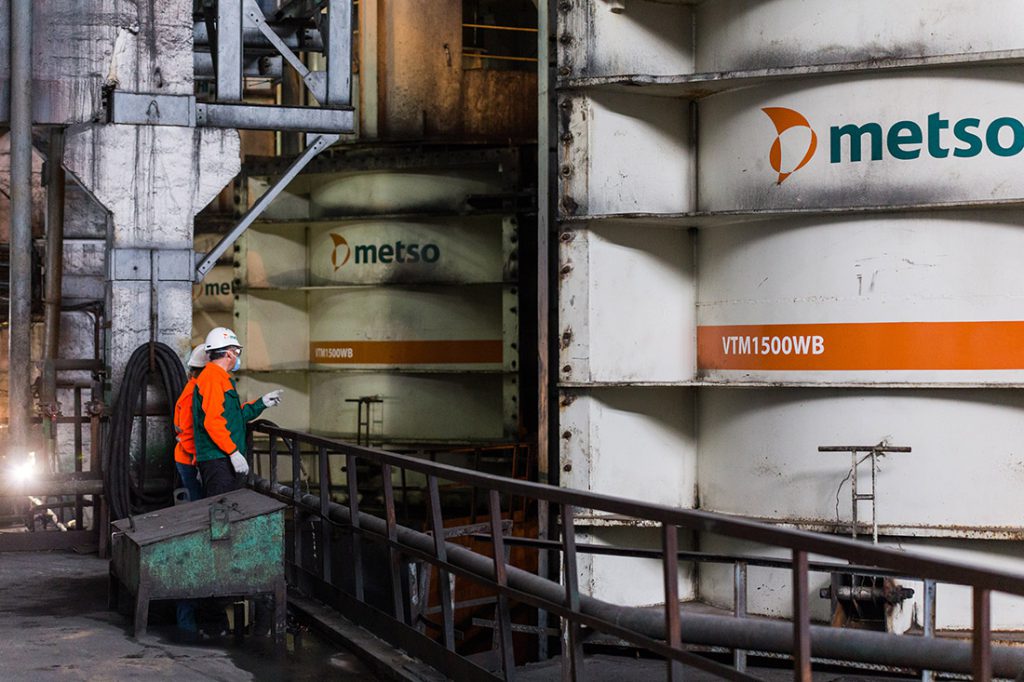
Vertimills are one of the best-known vertical milling technologies. They were originally introduced in the 1950s for industrial applications, and Metso completed its first large-scale installation for metallic ore grinding in 1980. The company has gone on to sell nearly 450 units worldwide, and Metso’s CEO, Pekka Vauramo, told journalists at the Bauma 2019 tradeshow in Munich, Germany, earlier this year that these units generated a collective saving of 625,000t of CO2 during 2018 – the equivalent to around 20% of what a small airline produces in a year.
The Vertimill product line features standard mill sizes from 11kW (15hp) to 3352kW (4,500hp) and can handle feed sizes up to 6mm and grinding products smaller than 20 µm. Vertimills can operate with a minimum energy consumption of 20%, making them useful for regrinding and other applications with variable flows and, on average, they offer a 25-30% reduction in energy consumption compared to ball mills.
An excellent example of this can be seen at Anglo American’s Minas Rio iron-ore operation in Brazil. The mine was able to cut its electrical power consumption by 30% by applying vertical mills instead of ball mills in its regrind circuit. The mine opted to install 16 Vertimill VTM-1500-WB grinding mills to create a circuit with two regrinding lines. Each comprises eight mills, each with an installed power rating of 1.1MW, and four cyclone batteries for grading iron ore.
Rodrigo Vilela, director of operations at the Minas-Rio system, part of Anglo American’s Iron Ore Business Unit, explained: “Minas-Rio uses 17.9MW of power in its regrinding process while the application with ball mills would be 25.6MW; this represents a significant reduction of 7.7MW.”
This energy saving equates to a financial gain of €5.5 million (R$23 million) per year for Anglo American (excluding taxes) – including energy costs, demand and charges related to the use of the regrinding circuit.
SMDs meanwhile are best suited to fine and ultra-fine grinding applications with feed sizes from 250 µm. They use rotational energy created by impeller arms to impart a high-energy motion to the media/slurry mixture inside the mill. This results in particle-to-particle shear and compressive forces which produce a grinding mechanism. The power intensity of SMDs (kW/m3) is relatively high compared with other mill types, but this is necessary to generate a vortex within the slurry during operation and to bring the particles into contact for efficient grinding.
In general, the finer the product required, the more efficiency stirred mills exhibit over ball mills. The grinding action (attrition), vertical arrangement, and finer media size distribution means that Vertimills offer an average energy saving of 30-50% compared with ball mills, while SMDs offer savings of more than 50% in very fine grinds.
Another benefit that comes with less energy use is a reduction in media consumption. One concentrator in Mexico experienced a 48% drop in media consumption from 821g/t to 429g/t using Vertimills, which equated to a significant reduction in consumable costs and also in carbon footprint.
On a roll
At the coarser end of the feed spectrum, HPGRs, a technology that also originated outside of the mining industry in cement applications, offer energy efficiency opportunities when employed as part of quaternary, tertiary or pebble-crushing circuits.
HPGRs are best suited to high-tonnage, hard-rock operations where the material has a relatively low moisture content. They use two counter-rotating tires – one fixed and one floating – studded with tungsten carbide nodules to instantaneously crush ore. Hydraulic cylinders apply very high pressure to the system, causing inter-particle comminution as the feed travels between the two tires.
The basic operating principle behind HPGRs makes them very energy efficient: the feed is introduced to the crushing zone, where high pressure is applied to the bed of material in a controlled manner. This creates microcracks within the ore which weaken the particles

Metso’s product, the HRCTM, features a patented Arch-frame that provides an even gap setting across the width of the tires and prevents skewing. This helps to extend the wear life of the roller bearings and the tire surface. The frame also eliminates the need for spring-loaded cheek plates, which are replaced by flanges in the HRC. These keep the bed of material within the HRC’s crushing zone and ensures a more even pressure profile across the length of the bed to maximize the amount of ore that is crushed.
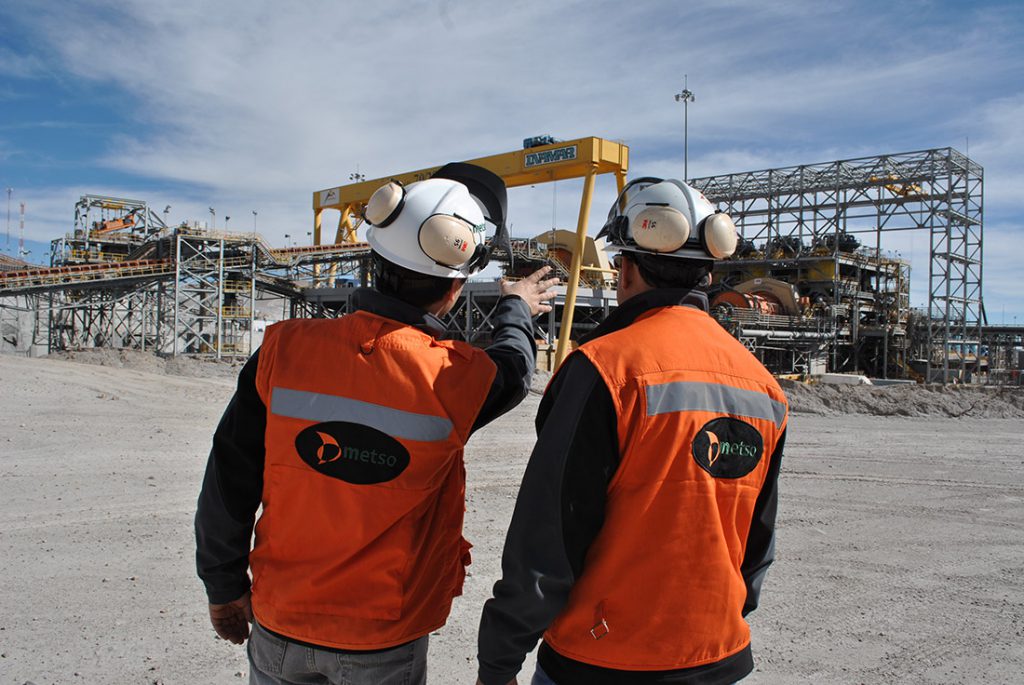
A high-profile example of HPGR efficiency is the Metcalf Concentrator at Freeport-McMoRan’s Morenci site in Arizona, US, which began operating in May 2014. The team at Metso worked alongside Freeport to install an HRC 3000 at the new 63,500t/d facility. Weighing in at 816t (900 short tons) and featuring two 3.0m x 2.0m tires capable of crushing 5,400t/h of ore, this is still one of the largest HPGRs ever installed.
Due to diminishing ore grades and rising energy costs, Freeport was looking for a more energy-efficient way to process its ore, and HPGR provided a flexible and economic alternative to a traditional semi-autogenous grinding (SAG) mill-based circuit.
At Metcalf, the HRC is fed by a secondary cone crushing circuit and is followed by two ball mills for secondary grinding. The the speed and pressure can be adjusted to reduce energy consumption further during periods of low throughput or with less competent ore types.
Conclusion
There are many options open to both new and existing mines when it comes to reducing the energy intensity of their operations, and particularly comminution circuits. As demonstrated above, the potential return on investment associated with new technologies can be significant, and reputable OEMs can tailor or build solutions to fit specific needs.
It’s a cliché ending to an article but, aside from inefficiency, mines literally have nothing to lose and everything to gain by improving their energy efficiency.
More News
{{ commodity.name }}
{{ post.title }}
{{ post.date }}
Comments