US battery belt grows with $1 billion Kentucky cathode deal
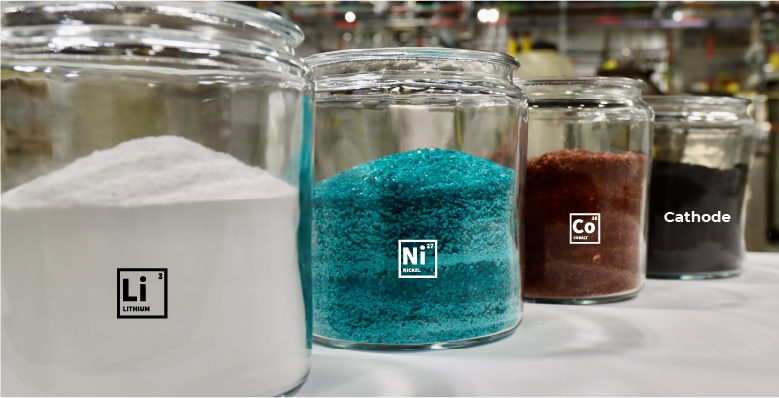
For years, the US electric vehicle industry has grappled with two supply-chain issues: how to source critical materials for battery production, and what to do with old batteries once they’re spent. A deal announced today by Ascend Elements aims to address both challenges.
The Massachusetts-based maker of battery materials said it has reached a billion-dollar deal with an unnamed automaker to reprocess old batteries into cathode material, a substance that’s responsible for more than one third of the expense of a finished EV battery pack. Ascend is building a cathode plant in Hopkinsville, Kentucky, and plans to begin deliveries next year.
The contract covers cathode for at least 40 gigawatt hours of batteries a year, Ascend Chief Executive Officer Mike O’Kronley said in an interview, enough for 750,000 electric cars. In 2021, that would have satisfied the entire US EV industry, but five times as much cathode will be needed by 2025, according to BloombergNEF data. Ascend’s contract marks the second major deal for cathode made in the US, and follows a similar agreement between Nevada-based Redwood Materials Inc. and Panasonic Holdings Corp. in November.
Most of the world’s cathode currently comes from China, but US-sourced battery materials are in increasingly high demand. To qualify for consumer tax incentives passed in last year’s Inflation Reduction Act, EV batteries must be built in North America using materials processed by close US trading partners, which excludes China. Those incentives and others pushed by the Biden administration have spurred more than $70 billion of investments since last August along America’s new Battery Belt, which stretches roughly from Michigan to Georgia.
“When you step back and look at it, we haven’t seen this level of investment in manufacturing in the United States in decades,” O’Kronley said. “This is really just the start. It represents one of the very first commercial realizations of what the US is trying to do nationally.”
Ascend was founded in 2015 by two battery researchers at Worcester Polytechnic Institute. They developed a process for extracting complex cathode chemistries directly from shredded battery materials — skipping the laborious process of first extracting each mineral individually. At a plant in Covington, Georgia, Ascend recycles battery materials out of discarded consumer electronics and manufacturing scrap from plants run by Honda Motor Co. and Hitachi Ltd., among others.
O’Kronley says Ascend has laid the foundations for its new cathode plant in Kentucky and plans to begin installing manufacturing equipment by the end of the year. Cathode delivery will start in the fourth quarter of next year, with full-volume production in 2025. The contract is for a minimum of $1 billion of cathode delivered over no more than five years, with options for the buyer to expand to $5 billion of cathode under similar terms. Ascend said the buyer requested not to be named.
O’Kronley worked in auto manufacturing for 30 years before becoming CEO at Ascend in 2020. In 2016, he was head of corporate strategy at A123 Systems LLC, a producer of lithium-ion batteries, when he received some early samples of recycled cathode from Ascend. Prototype battery supplies rarely hold up against established products, but A123 built Ascend’s cathode into some batteries for testing against a leading supplier.
“That material performed better than the material A123 was buying — really to the surprise of the entire technical team,” O’Kronley said. A123 soon became an investor in Ascend, and O’Kronley joined the company’s board. Ascend plans to close a Series D funding round this summer to finance additional factory expansion, though O’Kronley said it hasn’t decided whether to build additional operations in Kentucky or elsewhere.
The company’s growth to this point was assisted by $480 million in matching grants from the US infrastructure law, which O’Kronley described as key. Battery manufacturers “knew what we were capable of, we just needed to prove that we could build a factory,” he said. “Having that non-diluted funding come in was extremely helpful and is now starting to translate into commercial contracts.”
(By Tom Randall, with assistance from Gabrielle Coppola)
More News
{{ commodity.name }}
{{ post.title }}
{{ post.date }}
Comments