Miners say covid-19 has accelerated move to digital, automation
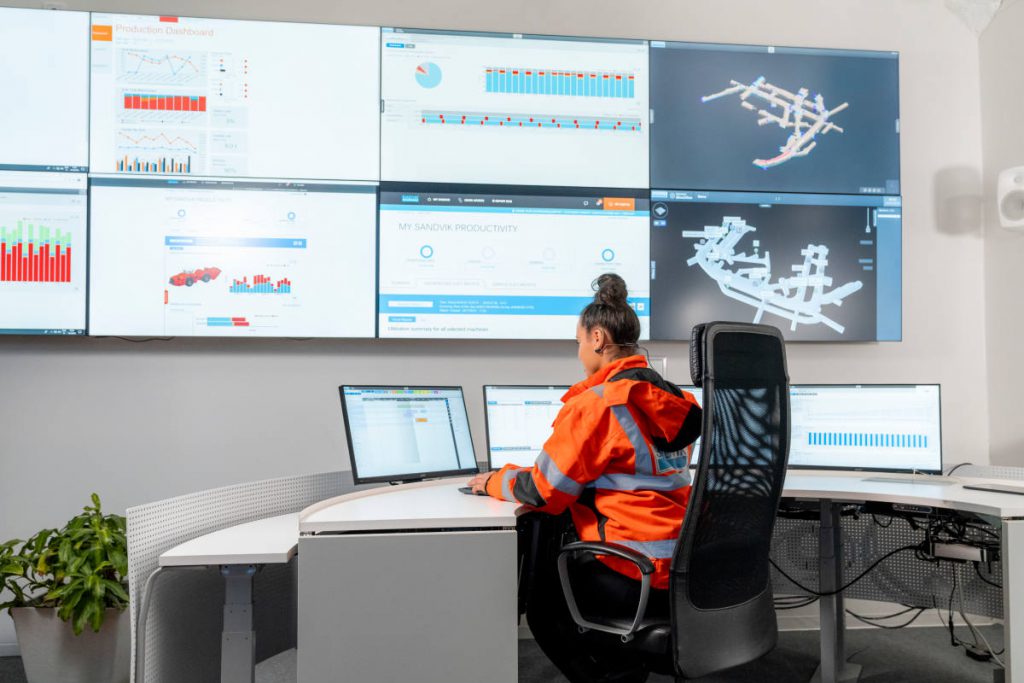
The coronavirus lockdown is hastening digitalisation and automation in the mining industry, major firms and their partners said this week, helping to get more work done at remote mines, even if operators are far away.
That trend will drive down costs quicker, leading to smaller, cleaner mines where more can be done with fewer people, industry officials said at the Imarc mining conference in the southeastern Australian city of Melbourne.
“The pandemic has forced us to think about how we can do more of the work that had to happen on site, remotely… (and) how we do those tasks with less people,” said Suresh Vadnagra, chief technology officer at Newcrest, one of the world’s largest gold-mining firms.
Big data now allows energy use and carbon emissions to be tracked and integrated with a mine’s maintenance and operations
Digital twinning and better use of big data was also winning adherents, he added.
Australia’s Big Three iron ore miners already have “digital twins”, or big city control centres to let them manage parts of their operations from hundreds of kilometres away, but such sites are becoming more common.
Blasting the ground to collect ore offers an example of how big data is being used to make operations more efficient.
Manually drilled blast holes can have small differences in relation to their location on a plan, as well as to each other, which can sometimes mean a blast sequence is not efficient.
Now a detonator put in the bottom of a blast hole can function as a sensor that can provide information such as moisture content and signal its position relative to the rest.
“All this data allows the possibility to utilise Artificial Intelligence (AI) for modelling and designing blast timing,” said Dirk van Soelen, a vice president at explosives maker Dyno Nobel.
Efficiencies of this kind, combined with new technology, will help diversified miner Anglo American carve out another 10% to 20% of costs in the next three to five years, said Chief Executive Mark Cutifani.
“In using automation and industrial processes, we have changed mining methods,” he said. “Anglo is using bulk ore sorting and it plans to roll that through our sites in the next few years.”
Improved methods of sorting ore grades at its copper mines are helping Anglo cut its energy intensity, he added.
Big data now allows energy use and carbon emissions to be tracked and integrated with a mine’s maintenance and operations, said Bas Mutsaers, global strategy tech and marketing lead at Schneider Electric.
“We can use this data to confirm our understanding of the processes at the site, to see correlations,” he said, which could help miners forecast when to consume, produce, store or sell energy on solar farms, for example.
“AI is allowing us to do this at ever higher levels of complexity and speed.”
(By Melanie Burton; Editing by Clarence Fernandez)
More News
US stocks surge most in 5 years as Trump delays some tariffs
The S&P 500 Index surged more than 7% in afternoon trading.
April 09, 2025 | 11:14 am
Liontown kicks off production at Australia’s first underground lithium mine
Miner said the successful start of underground production stoping from the Mt Mann orebody is a "key milestone".
April 09, 2025 | 10:52 am
Chile mining minister expects short-term copper demand to slow due to tariffs
The country would hope for a competitive advantage at the low-end of tariff range, Mining Minister Aurora Williams said.
April 09, 2025 | 09:40 am
{{ commodity.name }}
{{ post.title }}
{{ post.excerpt }}
{{ post.date }}
Comments