Graphite can come from a surprising source: methane
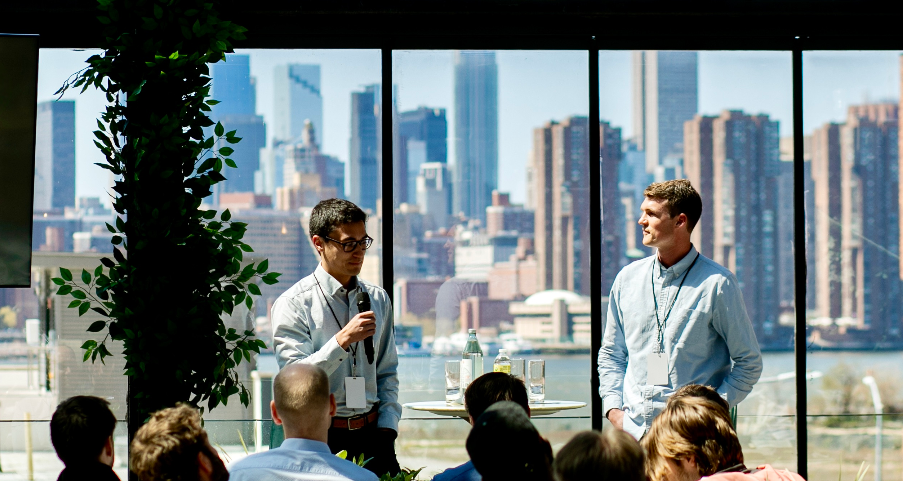
Graphite is key to manufacturing the lithium-ion batteries that power everything from electric cars to smartphones. While China is the world’s top producer and exporter of the crystalline carbon, there’s been a push to grow a US supply chain.
Oakland-based startup Molten Industries is working to build it by relying on something that’s cheap and abundant in the US: natural gas. The company has developed a specialized technique to break methane into graphite and hydrogen, the latter of which can be used as a source of clean energy. The effort is funded in part by a $25 million Series A financing round led by Bill Gates’s Breakthrough Energy Ventures (BEV).
“This is at the intersection of two really important climate tech theme areas for us at Breakthrough: making batteries scaleable and more cost-effective to drive EV sales to grow, and on the other side, low-cost clean hydrogen,” said BEV managing director David Danielson.
Big automotive companies are hungry for low-cost, reliable domestic graphite due to international supply chain issues, he added. Graphite is typically mined or made synthetically from fossil fuels, and China controls about three-quarters of the world’s graphite anode supply chain, according to data from mineral intelligence firm Benchmark.
Higher freight costs like those experienced during the pandemic and China’s temporary export restrictions have raised concerns in the US and elsewhere about the risk of largely relying on one source of the valuable material. Boosting domestic production is a key priority of the Biden administration, which in 2022 invoked the Defense Production Act to fund the industry.
To create graphite, Molten relies on pyrolysis, a technique that involves heating methane until it breaks into its constituent components of carbon and hydrogen. If there’s no oxygen or water present during this process, the methane gets split without any resulting CO2 emissions.
Other pyrolysis companies exist but most create products like soot or carbon black that can’t be used in battery production. Those companies also often rely on microwave or plasma-based heating, techniques that can be very energy-intensive. By contrast, Molten’s reactor is like a toaster: It uses resistive heating, which is more efficient, according to co-founder and chief executive officer Kevin Bush.
Molten says its graphite will be cost-competitive with other sources. It’s also banking on the fact that customers will want a lower-emissions synthetic graphite than the kind currently on the market, which is made by treating fossil fuel-based feedstocks using a process that emits methane and air pollutants. The only potential sources of emissions in Molten’s process are from producing the natural gas it uses as feedstock or the grid electricity powering the pyrolysis.
Graphite wasn’t a big part of the startup’s vision when it was founded in 2021. “Our original focus was just to make the lowest-cost hydrogen with the most energy-efficient reactor possible,” said Bush. “We did figure out along the way that we could actually make battery-grade graphite rather than just an amorphous carbon soot.”
Molten has built a pilot reactor in Oakland and is constructing a full commercial-scale unit the size of a shipping container that Bush said he expects to be operational next year. That unit will be able to produce 500 kilograms (1,100 pounds) of hydrogen and 1,500 kilograms of graphite daily, he said.
Whether there will be demand for the latter in the coming decades remains to be seen, though. Other materials like silicon, lithium and hard carbon may begin to compete with graphite as the default material in battery anodes, according to BloombergNEF. The shift could potentially halve demand by 2035.
The market for hydrogen may also be challenging because of high costs to produce and use it and policy uncertainty, according to Payal Kaur, a BloombergNEF hydrogen analyst.
“It’s a story that follows pretty much every market,” Kaur said. “You have way more supply than you do offtake.”
(By Michelle Ma and Rafaela Jinich)
More News
{{ commodity.name }}
{{ post.title }}
{{ post.date }}
Comments