Improving energy efficiency in comminution
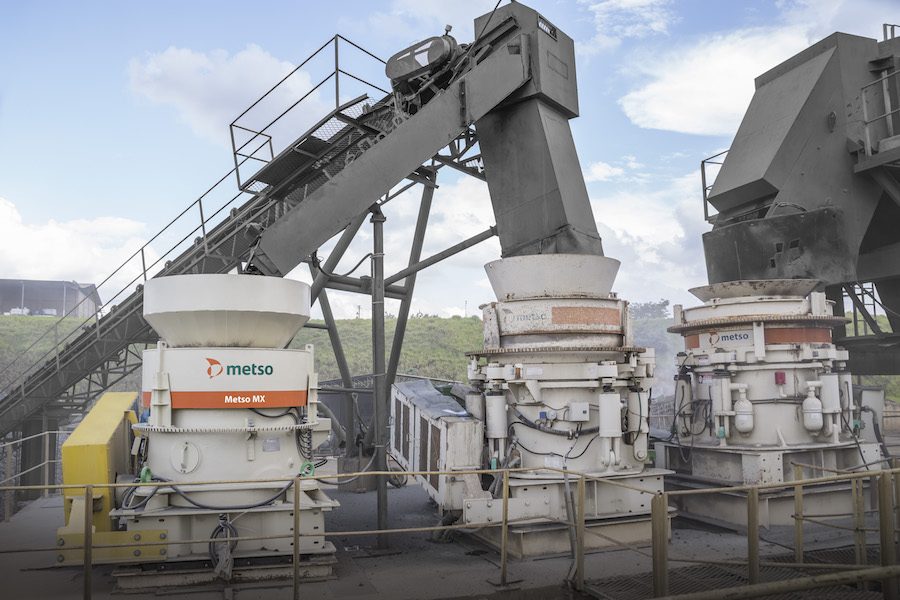
The comminution process, which includes both crushing and grinding, is one of the world’s most energy-intensive industrial processes. Comminution uses at least three percent of total global electricity production and according to the Coalition for Energy Efficient Comminution, it accounts, on average, for more than 50 percent of a mine’s energy consumption and 10 percent of total production costs. Energy-efficiency is one of the pillars of comminution circuit design, and ignoring this can be the difference between a profitable operation and a money loser.
Mines rarely have control over the cost of energy, so it is vital that comminution processes meet process objectives while consuming as little energy as possible. Specific energy consumption (kWh/t) is a significant contributing factor when a new comminution circuit is selected, because the electrical power accounts for such a large portion of the overall operating costs. An efficient operation is the best hedge against variable energy prices.
MINING.com asked three experts at Metso to discuss ways for mining companies to improve energy efficiency in comminution. The experts are Alan Boylston (AB), Director of Process Engineering Development, Suzanne Lynch-Watson (SLW), Global Manager – Consulting & Labs, and Peter Radziszewski (PR), VP Product RTD, Consumables.
PART 1: Making the right investment – designing an energy-efficient comminution circuit
How do you design an energy-efficient comminution circuit?
AB: “Horses for courses” is an old British expression meaning that people (or horses) have different skill sets and should be used accordingly. The same is true for comminution circuits. There is no magic design that is the best for all circuits. Comprehensive ore characterization work on both composite and variability samples, is key in determining the right comminution circuit design. In hard rock applications the designer may favor a design that incorporates more crushing upstream of an HPGR (high pressure grinding rolls) circuit for energy efficiency. But if there is a lot of clay present or there is high moisture this is probably not the best design. In this case, an AG or SAG mill may be appropriate. For smaller throughput scenarios, a three-stage crushing plus rod mill plus Vertimill may make the most sense. It all depends on the ore characteristics and the overall plant requirements.
SLW: Generally, when a circuit is designed, a number of alternative circuit configurations are considered in the early stages. The traditional SAB (SAG following by ball milling) is one option always considered due to its capacity to process very high tonnages, the relative simplicity of design, high availability and the fact that it is accepted so widely. However, it is one of the most inefficient means of comminution.
Depending on the ore characteristics, some ores are suited to HRC (high pressure grinding), which is a much more energy-efficient process, or three/four-stage crushing. It is very important to think about the pros and cons of each option, especially considering the ore types to be processed, the location, the environmental considerations and the size of the operation.
Should one go for bigger or smaller units to maximize plant efficiency and save energy and costs?
AB: Sometimes having two pieces of equipment do the job that one can do is not the best solution. Some designers prefer having two smaller mills instead of one large mill. The thinking is that when one mill goes down, the other is still operating and you still have 50 percent or more plant throughput. However, what is often overlooked is that with two smaller mills, the total frequency of shutdowns is likely to be double, so is there really a gain? Add in the additional cost of labour, parts, planning and tools to maintain two mills instead of one, and I tend to think the costs outweigh the benefits.
SLW: Having one large piece of equipment means a lot of cost saving at every stage of the operation – less civil and structural costs (concrete and steel), less conveyors/bins/chutes/material handling equipment, less moving parts and maintenance. This is the reason why SAG mills became so popular. Previously it was not uncommon to see four lines of rod mills, each with two small ball mills, to achieve the same or lower throughput as an SAB circuit today.
The trend over the past 30 to 40 years has been towards bigger and bigger equipment and now we ask the question: Is there a limit to this, and is it the most efficient way to break rock? In my opinion, the answer is no, it is not the only option we should consider.
As a general rule, the larger the reduction ratio that a comminution device is required to achieve, the less efficient it is. Comminution machines can be much more energy efficient if they target a smaller size range, ie. F80 to P80. Therefore, a really energy-efficient circuit may mean three stages of grinding instead of only two and each stage can be slightly smaller and more efficient than one big one – for example, a SAG mill (or HRC) followed by a ball mill and with a tertiary Vertimill. These options should at least be considered in the prefeasibility stage to see if the energy savings overcome the cost of an extra stage of grinding.
How are IPCCs more energy-efficient than traditional truck and shovel operations?
AB: IPCC and reductions in fuel consumption are an integral part in comminution efficiency. IPCC by itself is not more energy efficient – the crushing and screening unit operations are the same as in a stationary plant. However, conveyors are far more energy efficient than trucks so there is a big decrease in fuel consumption. Combining IPCC and coarse ore sorting – for example by rejecting waste rock after secondary crushing in the pit – can be a game changer. Not only is there a benefit of reduced energy consumption in the mills (and higher recovery), but the cost to convey material out of the pit goes down proportionally to the amount of material rejected.
PR: On the other hand, conveyor systems tend to be less flexible than haul trucks and in many cases there is a risk that if a conveyor stops, the whole operation stops. With a haul truck, if a truck breaks down, the other trucks are still running. Production is not at risk. But this is changing with more flexible systems, remote monitoring and easier change-outs of parts while operating.
PART 2: How to leverage your investment and save energy through process optimization
One way to save energy is by more blasting and less crushing and grinding. This way you can reduce the feed size before primary crushing, thus increasing circuit throughput and reducing the energy required for downstream comminution.
What is the role of drill and blast designs in increasing throughput and saving costs and energy in the next stages of the process?
PR: Blasting is the most cost-efficient means of ore size reduction. Chemical energy is cheap as opposed to electrical energy. If you can design a blast pattern that maximizes the use of cheap chemical energy in a safe manner, you will have a significant impact on the electrical energy required to complete the size reduction process.
SLW: This is an interesting topic on which Metso has worked a lot during the years. We have numerous case studies in which changes in drill and blast designs have led to increases in downstream throughput of five to 20 percent. Our case studies are in open pit mines primarily for SAG circuits, but also for tertiary crushing circuits.
In-situ rock has two main parameters which define the Run-of-Mine (ROM) size distribution that is generated in the blast. They are: rock structure (which defines the top size) and rock strength (which defines the amount of fines generated). The blast design – burden, spacing, hole diameter, bench height, explosive, stemming, delays, size of polygon, etc. – determines the intensity of the blast. However, there are limits to how intense a blast can be, dictated by the surrounding rock. It is important to consider stability, vibration and other factors to make sure the blast is not so intense that it causes environmental or safety issues.
Increasing throughput through a SAG mill generally requires feeding it with more fines, since these flow straight through the mill. If these can be generated in the blast, then it is a much more cost-effective way of achieving a higher SAG throughput.
Generally, the biggest benefits (10 to 20 percent increase in throughput) are seen for the hardest ore. Softer ore benefits much less, and sometimes it is necessary to reduce the intensity of the blast in these cases to ensure an optimal ROM for downstream processing.
One very important point is that more blasting does not mean less crushing. It does make the job of the primary crusher a little different, but any subsequent crushing stages need to be fully utilized to ensure they are processing to capacity. It is also very important to ensure that any changes to the ROM are taken into account when reviewing the primary crusher operation. Liner profile and crusher settings should be reviewed to ensure the crusher is operating well and able to transfer the benefits of the new ROM to downstream processing stages without causing problems in the crusher.
As an example, we had a case that had heterogeneous rock characteristics in terms of its mineralogical, geological and geotechnical properties. We recommended changes to blast designs and comminution practices, and these were partially implemented for a validation trial. The trial demonstrated a 14.8 percent increase in mill throughput for the specific ore selected for the study, and an average increase of 5.7 percent for all ore types, with no additional installed equipment/power/capacity.
What are the downstream benefits of pre-concentration and what are the current available technologies?
AB: Pre-concentration and ore sorting is a hot topic these days, as rejecting waste rock early is the most direct way to reduce comminution cost. The trick is to limit how much valuable material is rejected along with the waste. When done properly, pre-concentration can actually increase recovery, leading to a win-win scenario: less power consumption and more metal production.
SLW: I agree with Alan. There is a quote by Rob Morrison of the Julius Kruttschnitt Mineral Research Centre (JKMRC) in Australia, which is: “The best way to break rocks better is not to break them at all.” This is the absolute fundamental goal of pre-concentration – to remove anything from the ore which does not need to be broken. The challenge is to remove the liberated gangue at each stage of comminution to ensure it does not consume energy unnecessarily in the following stage.
Most circuits are not currently set up to handle removal of gangue at each step, especially at the tonnages of large scale operations, but there is a great deal of work going on in this area, also at Metso. It is a two-part problem: the ability to detect the particles that are low grade/barren, and the ability to remove them. The first one is about having the right sensors which can detect the relevant ore property to indicate low grade, and the second one is about having the right equipment to divert the low-grade material to an alternate location, quickly and for high tonnages.
PR: I like the Morrison quote. But pre-concentration is not necessarily new and includes things like gravity separation, dense media separation, flash flotation and screening. More recent developments are related to sensor-based ore sorting such as optical sorting, X-ray sorting and the like which is, of course, of interest to us.
However, screening is the one that I like as it is often overlooked as a pre-concentration means. Basically, depending on the ore and operation, it is possible that a good portion of the ore after blasting or after SAG milling might already be liberated and reports to a smaller size fraction. Screening the small-size fraction out following a SAG mill or even an HRC might be appropriate. Such an analysis fits into Metso’s skill set and facilities.
PART 3: How does increasing wear life and reducing the number of spares factor into making the comminution circuit more energy efficient?
PR: Ah! Wear, a subject close to my heart! As mentioned previously, comminution produces three things: size reduction, heat and wear. There is published evidence that indicates, at least in the lab, that when you increase grinding efficiency, you actually reduce, at the same time, heat generation and wear. For a given mill, a limited amount of energy is input. It either goes to produce what we want (size reduction) or a larger portion of it goes to produce what we do not want (wear and heat).
SLW: Another example of improving wear life for increased mill performance, including reduced specific energy consumption, is given in a paper by Sever Ciutina (Metso MLS) and R.J.Soriano (Senior Metallurgist, Masbate Gold Mine, Philippines) at the 12th Mill Operators’ Conference, 2014. It provides an analysis showing how the installation of curved pulp lifters on the discharge of a fixed-speed SAG mill reduced wear issues, thus increasing the wear life, and also reduced the energy consumption without any corresponding loss of throughput (so a lower specific energy consumption of about 10 percent).
PART 4: Ensuring the longevity of your investment – energy savings and productivity gains through refits
A processing equipment overhaul may not be possible at some mines. For these operations, a refit may be the only option. Can you give us some examples of how a refit resulted in significant energy savings and productivity gains?
PR: One of our customers had a circuit running already, but needed to add energy in fine grinding in order to capture the full value of the ore they were mining. So, they added a VTM-3000. Their overall energy consumption increased, which normally would mean that the circuit is more inefficient. However, and more importantly, their operating work index dropped! It was quite a successful application of the Vertimill technology both from an energy efficiency point of view (as measured by operating work index) and from a value recovery point of view.
AB: I think the installation of two Vertimills at another customer’s operations in New South Wales, Australia is a perfect example here. The mine was going deeper and the ore was getting harder. In order to maintain throughput, a VTM1250 was installed in semi-parallel with the existing ball mill circuit. The VTM1250 accepted undersize from a new screen installed on a portion of the ball mill circuit’s hydrocyclone underflow. This allowed the ball mill to focus on coarser material while the Vertimill finished the grind on the finer material. The second Vertimill was the world’s first VTM3000. This was installed as a tertiary grind to reduce product size reporting to flotation. The net result of this installation was a two to four percent increase in flotation recovery.
SLW: Another interesting case is where upgrade kits were used in Peru to upgrade the Metso MP1000’s to MP1250 equivalent machines. The Metso crusher upgrade kits are a cost-effective way of achieving an increase in capacity without spending money on the installation and commissioning of new equipment. It is important to consider the whole circuit before upgrading though, to ensure this is the best solution for alleviating the bottleneck and achieving increased production.
Then there is the example of using an HRC as a pebble crusher to increase the throughput in the SAG circuit. It can be very effective in increasing SAG throughput for a small increase in installed power, therefore reducing the overall specific energy consumption across the SAG circuit.
A last important example is the replacement of cyclones with fine screens. Cyclones are not the most efficient classifiers since the separation is also affected by the specific gravity of the particles and other hydrodynamic properties. Their use became widespread in the 1950’s due to their small footprint and relatively low maintenance requirements. However, fine screens provide a much sharper separation, since they only separate on particle size. This means that an efficiently operating fine screen has much less by-pass (fine material which ends up in the coarse stream without being classified) and therefore a lower recirculating load. The lower recirculating load means that the mill is able to process more new feed for the same mill power consumption. Figures vary but average increases in throughput are around 15 percent (reference: Screens and Cyclones in Closed Grinding Circuits, Dundar et al, IMPC 2014). Metso’s fine screens have advantages in that they are stacked such that the footprint is as reduced as possible.
Where do you see energy-efficiency in the comminution circuit going?
AB: There is only one way for energy efficiency in mining and mineral processing to go, and that is up. My own research has shown that there is a remarkable correlation between global population growth and demand in metals like copper and gold. As the world population grows to 11 billion or more by the year 2100 (according to estimates by the UN), the demand for metals and minerals will grow accordingly. At the same time, a reduction in ore grades means more rock needs to be processed for every bit of saleable metal. If we don’t drastically improve the way ore is processed, the negative effects on the global environment and our standard of living will be enormous.
SLW: We need to do things a whole lot better than we do right now if we are to meet the demand. There is also the concept of circular economy, which is a field of great interest to many. Extracting metals from landfills, old machines, mobile phones and other waste products could be one of the most cost effective and energy efficient ways of retrieving metal in the future. We currently do not have the best technology to process these materials efficiently and in an environmentally friendly way, but it is an important area and it could become one of the key means of meeting world demand in the future. Metso already has some interesting technology for part of the metal recycling process.
{{ commodity.name }}
{{ post.title }}
{{ post.date }}
Comments