EVs vs. gas vehicles: What are cars made out of?
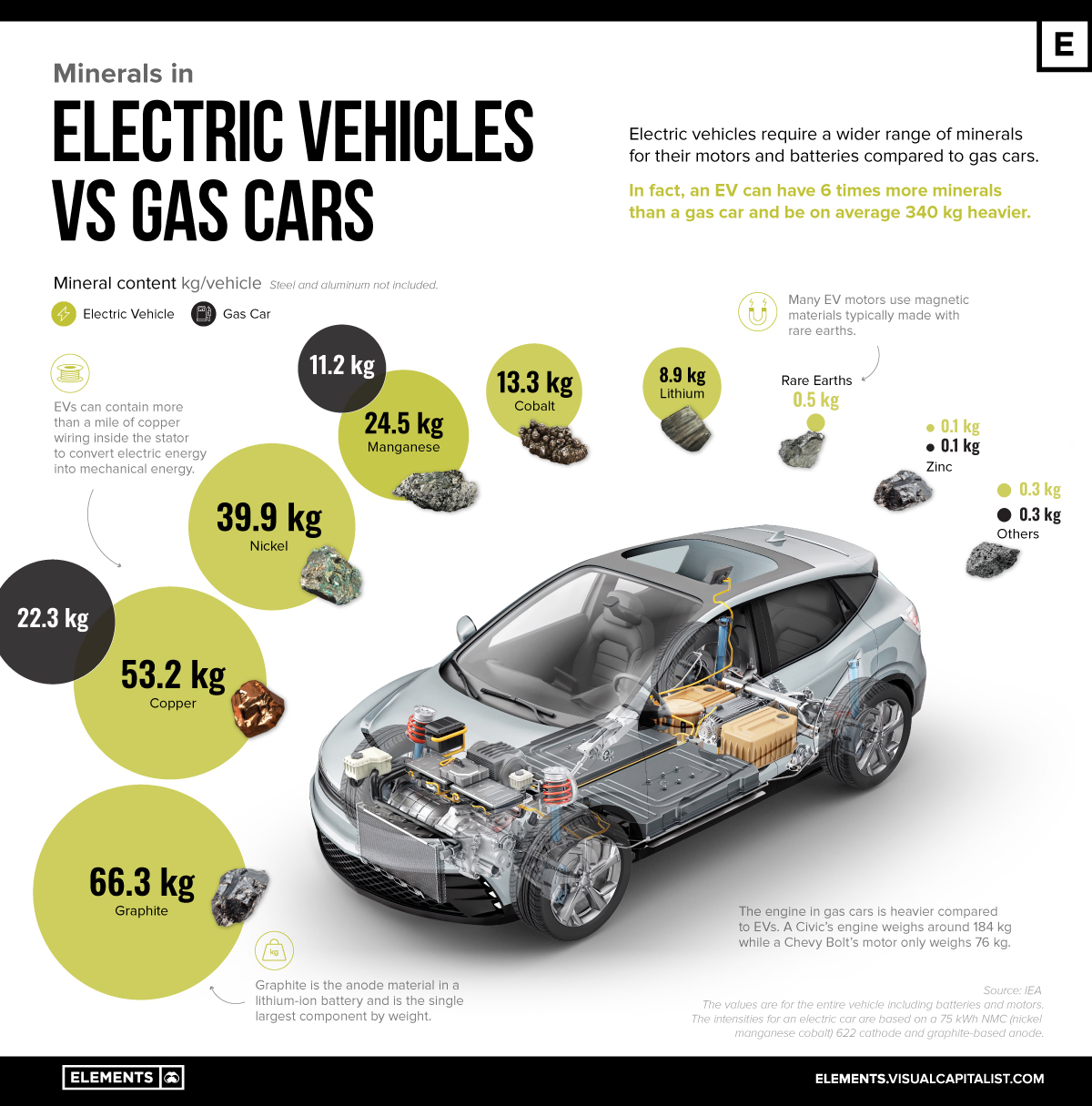
Electric vehicles (EVs) require a wider range of minerals for their motors and batteries compared to conventional cars.
In fact, an EV can have up to six times more minerals than a combustion vehicle, making them on average 340 kg (750 lbs) heavier.
This infographic, based on data from the International Energy Agency (IEA), compares the minerals used in a typical electric car with a conventional gas car.
Editor’s note: Steel and aluminum are not shown in analysis. Mineral values are for the entire vehicle including batteries and motors.
Batteries are heavy
Sales of electric cars are booming and the rising demand for minerals used in EVs is already posing a challenge for the mining industry to keep up. That’s because, unlike gas cars that run on internal combustion engines, EVs rely on huge, mineral-intensive batteries to power the car.
For example, the average 60 kilowatt-hour (kWh) battery pack—the same size that’s used in a Chevy Bolt—alone contains roughly 185 kilograms of minerals, or about 10 times as much as in a typical car battery (18 kg).
Lithium, nickel, cobalt, manganese, and graphite are all crucial to battery performance, longevity, and energy density. Furthermore, EVs can contain more than a mile of copper wiring inside the stator to convert electric energy into mechanical energy.
Out of the eight minerals in our list, five are not used in conventional cars: graphite, nickel, cobalt, lithium, and rare earths.
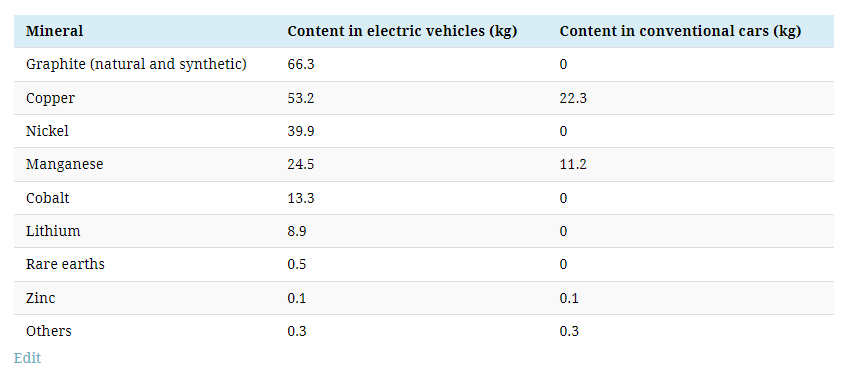
Minerals listed for the electric car are based on the IEA’s analysis using a 75 kWh battery pack with a NMC 622 cathode and graphite-based anode.
Since graphite is the primary anode material for EV batteries, it’s also the largest component by weight. Although materials like nickel, manganese, cobalt, and lithium are smaller components individually, together they make up the cathode, which plays a critical role in determining EV performance.
Although the engine in conventional cars is heavier compared to EVs, it requires fewer minerals. Engine components are usually made up of iron alloys, such as structural steels, stainless steels, iron base sintered metals, as well as cast iron or aluminum alloyed parts.
EV motors, however, often rely on permanent magnets made of rare earths and can contain up to a mile of copper wiring that converts electric energy into mechanical energy.
The EV impact on metals markets
The growth of the EV market is not only beginning to have a noticeable impact on the automobile industry but the metals market as well.
EVs and battery storage have already displaced consumer electronics to become the largest consumer of lithium and are set to take over from the stainless steel industry as the largest end-user of nickel by 2040.
In 2021 H2, 84,600 tonnes of nickel were deployed onto roads globally in the batteries of all newly sold passenger EVs combined, 59% more than in 2020 H2. Moreover, another 107,200 tonnes of lithium carbonate equivalent (LCE) were deployed globally in new EV batteries, an 88% increase year-on-year.
With rising government support and consumers embracing electric vehicles, securing the supply of the materials necessary for the EV revolution will remain a top priority.
(This article first appeared in the Visual Capitalist Elements)
More News
{{ commodity.name }}
{{ post.title }}
{{ post.date }}
Comments