Australian state establishes eco zones to process critical minerals
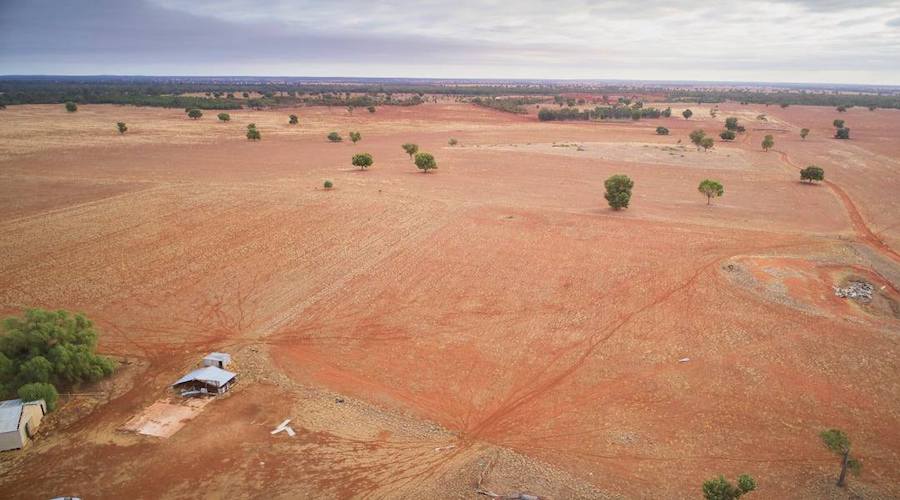
Australia’s New South Wales has set up development zones to tap growing demand for critical minerals that have been sustainably developed, a consultant to the state said on Thursday.
The “special activation precincts” will fast track industries including critical minerals processing, Janette Hewson said.
They will obtain United Nations certification for “eco-processing”, for example by using renewable energy, Hewson told a Minerals Council of Australia event in Canberra.
Australia is a large producer of so called critical minerals supplying half of the world’s lithium for electric vehicle batteries, as well as being major supplier of nickel and copper.
Companies that can process sustainably in a highly regulated environment will have an advantage with manufacturers and vehicle makers
It also has reserves of cobalt, which is used in some battery technologies, but has seen supply problems because of poor artisanal worker conditions in some producer countries.
“The demand trajectory is showing this huge need for credentialed critical minerals,” Hewson said.
Companies that can process sustainably in a highly regulated environment will have an advantage with manufacturers and vehicle makers, for whom sustainability and the carbon footprint of their supply chain is a growing concern, she added.
The comments chime with Tesla Chairman Robyn Denholm who said on Wednesday that the automaker planned to increase its spending on Australian minerals to more than $1 billion in coming years.
Manufacturing has to decarbonise very quickly over the next 30 years, Denholm told the same event, adding: “Low carbon minerals will be at a strong advantage in new supply chains being created through renewable energy.”
Mining processes currently account for roughly half of the carbon footprint of a battery cell. The best way to cut that is for Australia to stop shipping raw materials between 6,000 and 9,000 kilometres (5,592 miles) before refining, Denholm said.
Australia typically ships lithium and other minerals to battery chemicals makers in China, South Korea and Japan.
Part of the lithium processing called calcination is energy intensive and takes place in markets offshore with coal based energy grids. However, green energy and local production could significantly cut the carbon footprint of the product, she said.
(By Melanie Burton; Editing by Alexander Smith)
More News
{{ commodity.name }}
{{ post.title }}
{{ post.date }}
Comments