Treatment of refractory gold: more sustainable gold ounces with Metso Outotec’s new MesoTHERM BIOX process
Metso Outotec, a frontrunner in minerals and metals processing, has recently launched the Outotec MesoTHERM BIOX® process for the treatment of refractory gold. This innovative solution for the treatment of refractory gold ores significantly reduces cyanide consumption, and therefore costs, in the leaching of certain bio-oxidation product residues. The first refence plant is up and running at the Fairview mine in South Africa.
”The MesoTHERM BIOX process is based on the highly successful mesophile Outotec® BIOX® process. It produces cleaner product solids and offers an easy and cost-effective upgrade path for plants already using this process,” Jan van Niekerk, Director of Gold Process Solutions at Metso Outotec explains.
The standard process uses a mixed population of mesophilic bacteria with most BIOX plants operating at 40 to 42 °C. The new MesoTHERM process utilizes a combination of the traditional BIOX mesophilic bacteria as the primary oxidation stage followed by thermophilic bacteria, operating at ~ 65 °C, to complete the oxidation.
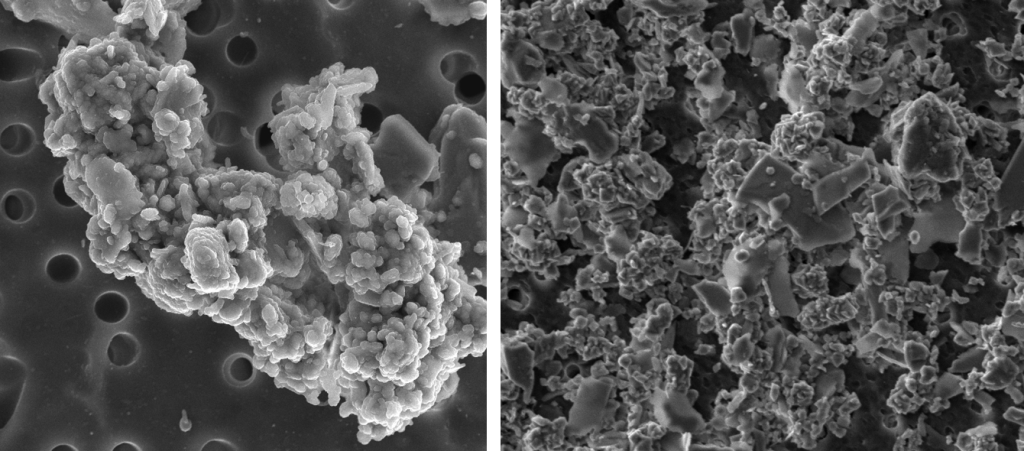
“The higher operating temperature in the thermophile stage allows for more complete oxidation of the sulphur in the concentrate, thereby reducing the cyanide consumption during the subsequent cyanidation step. Depending on the application, cyanide consumption can be reduced by up to 50%, lowering costs and reagent storage requirements,” says van Niekerk.
Over 25 million ounces of gold produced with the BIOX process
The BIOXprocess, designed for the treatment of refractory gold concentrates, has been commercially available for over 30 years with a total of 13 plants commissioned during that time.
“To date, over 25 million ounces of gold have been produced with BIOX. The process is especially suitable for remote locations by virtue of the simplicity of operation and scalability of the technology using a modular design,” van Niekerk explains.
Commercial BIOX plants operate at treatment capacity within the range of 20 to 2137 tons per day of flotation concentrate. Figure 3 shows the typical flowsheet. Table 1 shows the 13 BIOX plants commissioned to date with the 14th plant currently under construction.
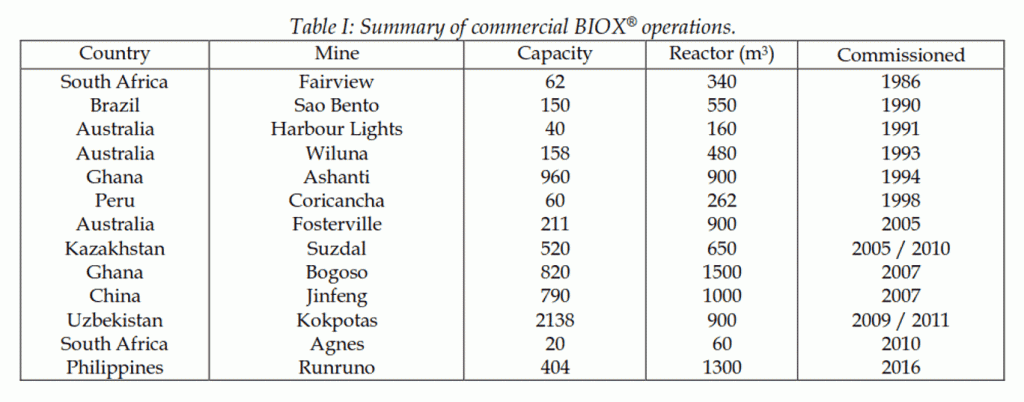
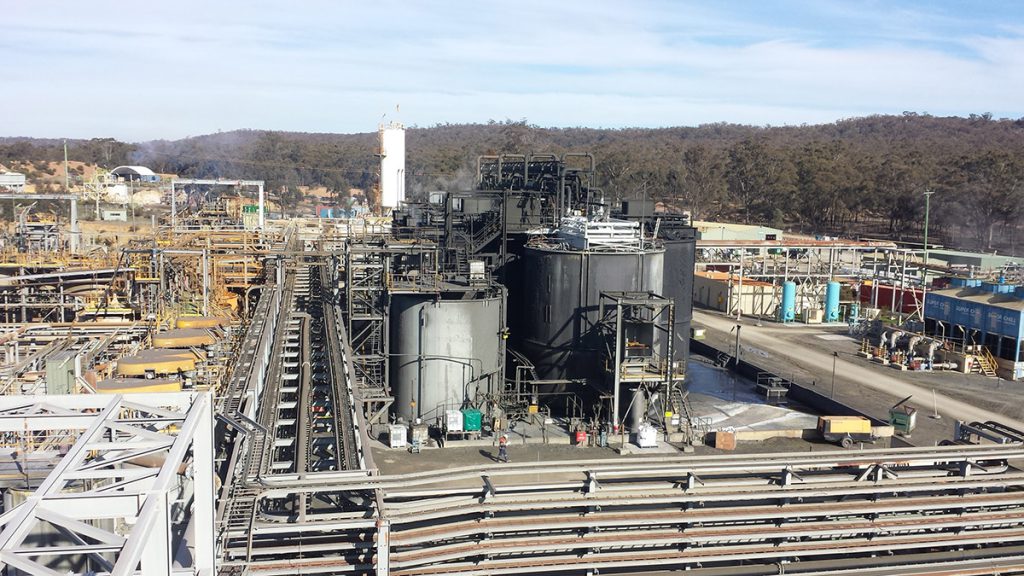
Reduced cyanide consumption and simplified process operation
“In the MesoTHERM process, the primary mesophile oxidation stage is identical to the BIOX process with the dilute concentrate slurry fed with nutrients to the primary BIOX reactors operating in parallel. Figure 3 shows a typical flow sheet for the MesoTherm process,” says van Niekerk.
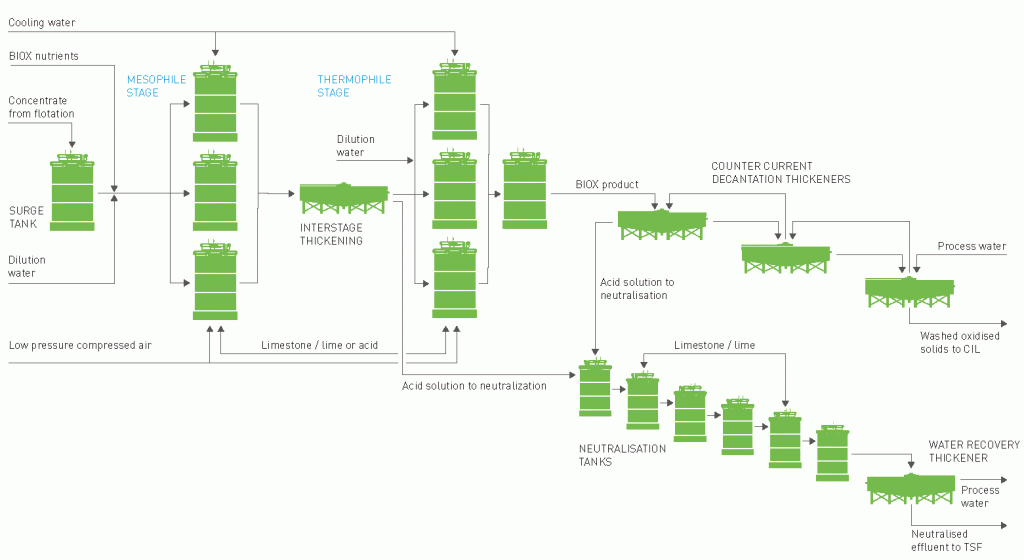
Sufficient residence time is allowed in the primary reactors for the bacterial population to be maintained under standard operating conditions. Compressed air is sparged into the reactors to supply oxygen for the oxidation reactions and evaporative cooling towers and internal cooling coils are used to remove heat generated by the exothermic reaction. The partially oxidised primary BIOX product is fed to an interstage thickener to remove some of the dissolved species prior to the thermophile oxidation stage.
The thickener underflow is then diluted to the target density prior to feeding to the thermophile stage. The thermophile stage consists of a number of primary reactors operating in parallel. The primary thermophile product overflows into a secondary thermophile reactor to ensure that high sulphide oxidation extents are achieved. The oxidised thermophile product is washed in a standard 3 stage CCD circuit prior to cyanide leaching.
“Cyanide consumption during leaching of the biooxidation product is an important operating cost parameter and for some concentrates, the cyanide consumption following mesophile biooxidation can be higher than alternative process routes,” van Niekerk explains.
The cyanide is consumed through the reaction of the cyanide with partially oxidised sulphur species to form thiocyanate as per reactions 1 and 2 below:
SxS2- + CN– → [S(x-1)]2- + SCN– 1
S2O32- + CN– → SO32- + SCN– 2
“The MesoTHERM process, operating at the higher temperatures during the secondary oxidation stage, aims to eliminate the presence of these partially oxidised species in the final biooxidation product, thereby reducing consumption of cyanide through the formation of thiocyanate,” says van Niekerk.
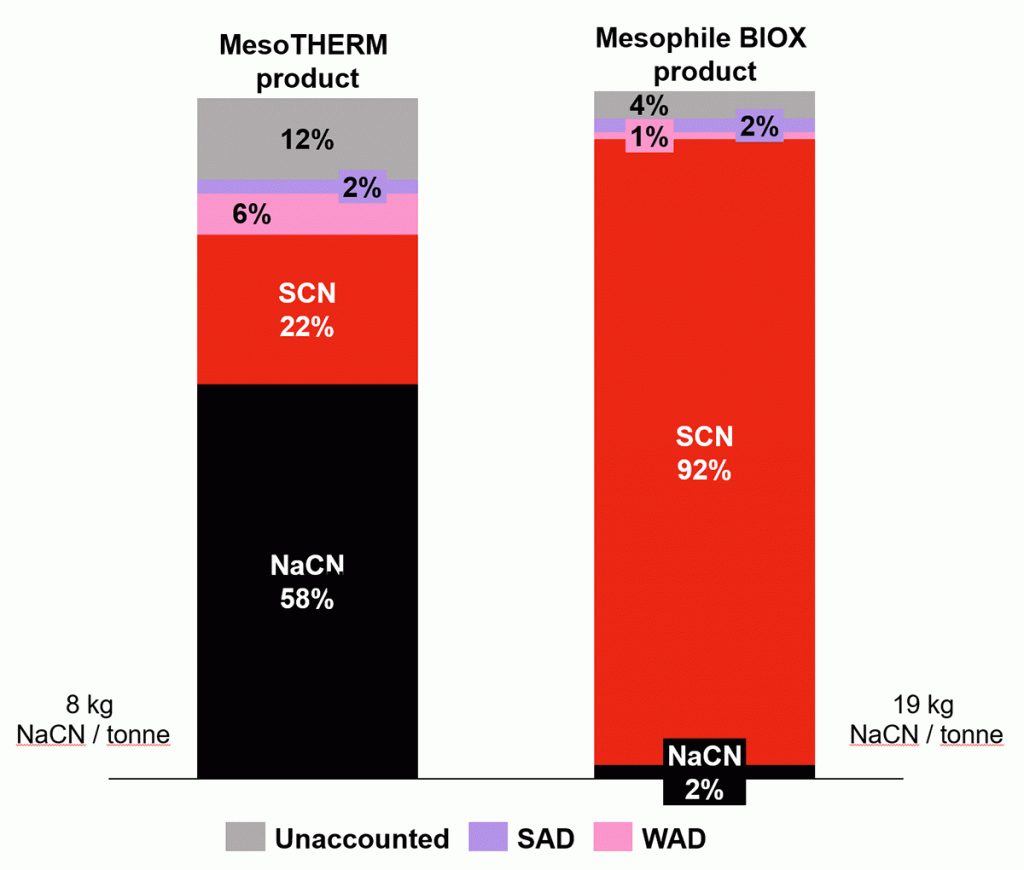
“Bench scale test work on a refractory gold concentrate indicated that the cyanide consumption during leaching of the biooxidised product can be reduced from ~19kg/t for the standard BIOX mesophile to 8 kg/t for the MesoTHERM product while maintaining the same gold recovery (see also Figure 4). The saving in cyanide consumption is due to the substantial reduction in the formation of thiocyanate in the leach residue solution.”
Pilot test work at Fairview BIOX plant verified design targets
The development of the MesoTHERM technology followed a strict toll-gated process from bench scale batch tests through various pilot plant stages to the 21 m3 demonstration reactor operated at Fairview BIOX plant in South Africa (Figure 5).
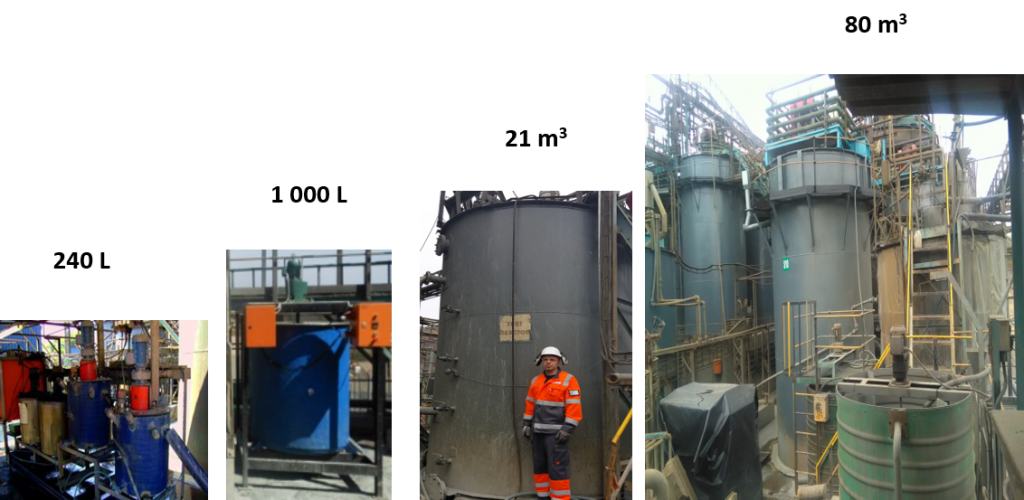
The initial bench and small scale pilot plant stages were aimed at confirming the technical and commercial viability of the process, to confirm the potential reduction in cyanide consumption can be maintained moving from batch to various size pilot plant reactors and to develop understanding of the thermophile bacterial culture.
“The pilot plant test work confirmed the initial good results achieved and gave Metso Outotec the confidence to proceed with the demonstration test run. The 21 m3 demonstration scale was used to extract the required process design correlations required for the design of the commercial scale thermopile reactors and to prove the process under industrial conditions treating a variable feed,” explains van Niekerk.
“The operation of the 21 m3 reactor confirmed that the thermophile stage can achieve similar and higher overall oxidation rates when compared to the mesophile product and that a 50 % reduction in cyanide consumption can be achieved while maintaining the overall gold recovery (Figures 8 a and b). The 21 m3 demonstration reactor also allowed the extraction of the required oxygen mass transfer data.”
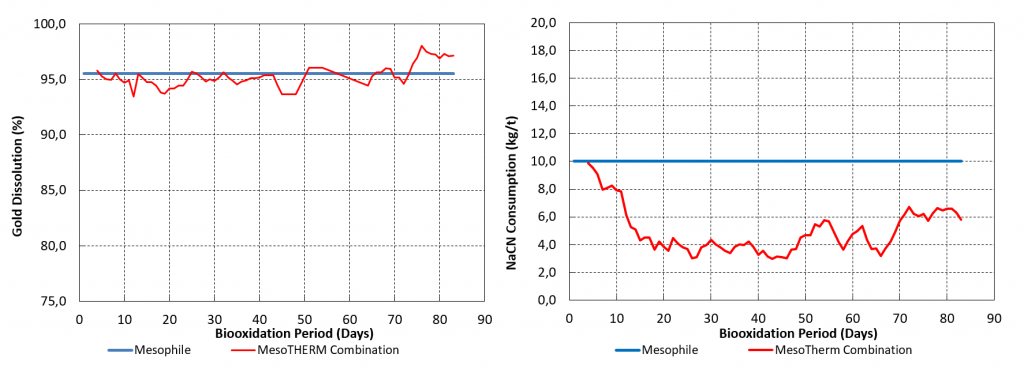
The final stage in the development process was the conversion of one of the commercial secondary BIOX reactors to a thermophile reactor. The 80 m3 secondary reactor was converted into a thermophile reactor and operated as a full production reactor at the Fairview BIOX plant in South Africa.
“Fairview’s reactor has now been in operation for over 12 months, treating partially oxidised BIOX product from the primary BIOX reactors. The operation of the reactor allowed the Metso Outotec team to confirm the scaleup correlations used for the design of the reactor. The stable operation of the reactor has also confirmed the ability of the process to achieve the anticipated cyanide consumption reduction under commercial operating conditions,” says van Niekerk.
First OKTOP BIOX Reactor to be commissioned soon
Agitator performance is critical for the overall performance and efficiency of the process. Thus, a complete OKTOP® BIOX® reactor design was completed to be used with the BIOX and MesoTHERM BIOX processes. The Outotec OKTOP® 3105 dual impeller, developed to give superior gas handling and oxygen mass transfer rates under typical BIOX operating conditions, enables also lower power consumption while maintaining process performance.
“The Outotec OKTOP 3105 impeller design (Figure 7) was selected as the optimum design for the BIOX application. It was tested using various configurations in a 500 l laboratory reactor before the optimum configuration (Figure 8) was tested both in water and BIOX slurry using a 21 m3 test reactor at the Fairview Mine,” says van Niekerk.
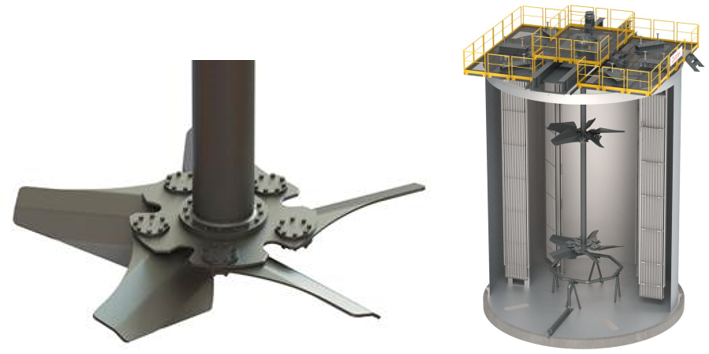
“The 21 m3 demonstration reactor confirmed that the selected configuration will result in superior oxygen mass transfer when compared to the traditional reactor configurations used for BIOX applications (Figure 9). The Cam and Motor BIOX plant, currently under construction in Zimbabwe will be the first application of the OKTOP 3105 configuration for a BIOX reactor.”
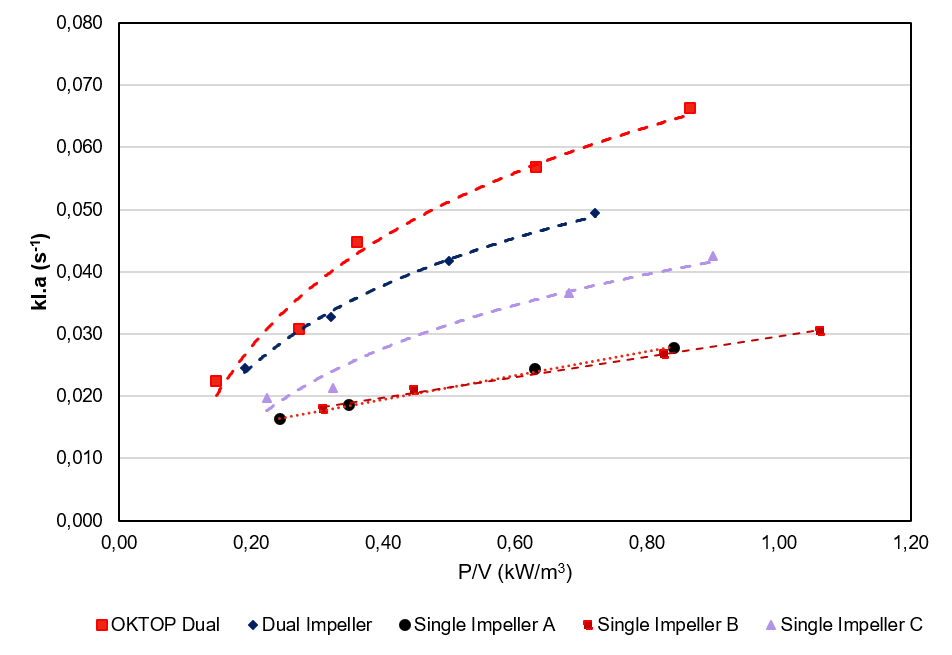
“The design of the Cam and Motor BIOX agitators confirmed that the use of the OKTOP 3105 configuration will result in significantly lower power consumption when compared to the traditional single BIOX impeller configuration used for the older generation BIOX plants,” says van Niekerk.
From ore to metals – full scope of gold processing solutions
As a result of the merger of Metso Minerals and Outotec, the new company Metso Outotec has become a leading provider of advanced solutions for the mining and metallurgical industry.
For the processing of free-milling ores to refractory gold ores, Metso Outotec offers end-to-end process solutions including comminution, flotation, pressure oxidation, bio-oxidation (BIOX® process), roasting, leaching and recovery with analysers and automation systems. Tailings management and effluent treatment are also an integral part of the company’s solution offering.
“Our competitive edge is based on our extensive experience in minerals processing, hydrometallurgy and pyrometallurgy combined with our proven technologies and equipment. One-stop provision of process design, plant engineering, equipment, automation and project management helps eliminate expensive and restrictive interfaces during implementation. In-depth process and plant knowledge make us a unique strategic partner for our customers,” concludes van Niekerk.
Find out more about the Outotec® MesoTHERM BIOX® process:
More News
{{ commodity.name }}
{{ post.title }}
{{ post.date }}
Comments