Enhancing flotation cells for increased sustainable production
With the world’s push towards sustainability, mining companies are examining ways to decrease their carbon emissions footprint – and assessing their onsite options, which can range extensively.
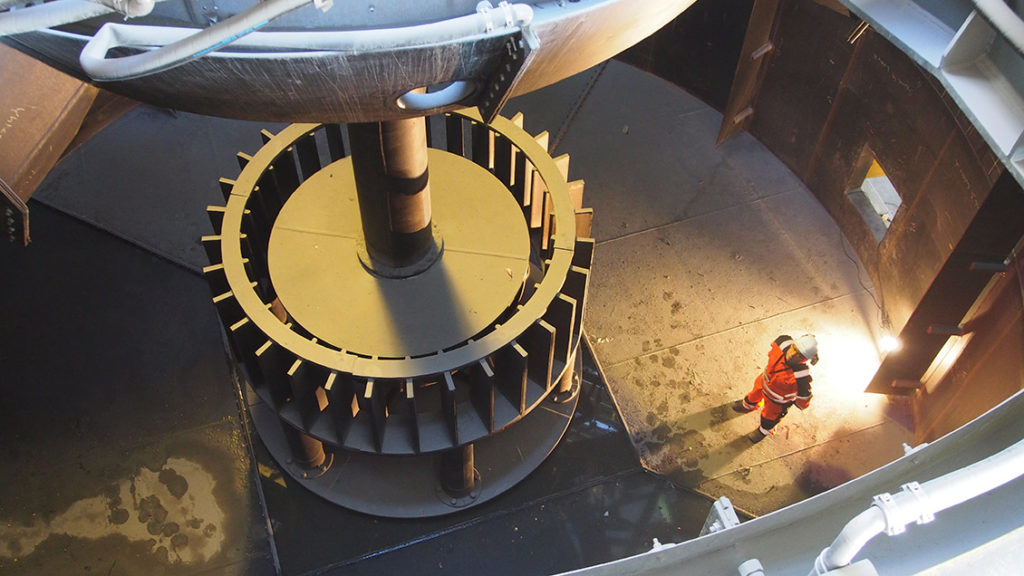
Within a plant, each process stage has untapped opportunities to reduce CO2 emissions, water, or chemical usage. The questions are always focused on ways to save on energy or reduce waste.
Flotation is a method widely used to separate and concentrate ores by altering their surfaces to a hydrophobic or hydrophilic condition is a topic engaged by many mining companies as one area that is being examined for ways to improve in terms of sustainability. Metso Outotec offers a number of options.
Optimize existing flotation operation
One of the first things to consider before considering major investments is whether the flotation machine is operating at its most efficient point,” says Guillermo Bermudez, product development manager at Metso Outotec.
“Optimizing a flotation cell involves verifying all aspects of your equipment to maximize process and mechanical performance.”
Several areas need to be examined, Bermudez says, including:
Flotation process assessment, which begins with a comprehensive assessment of your flotation circuit to clarify what is working well and what may need improvement. Measuring the flotation performance is the first step to understanding how to operate more sustainably. Mixing mechanism rotational movement consumes the most energy in a flotation machine.. Rotor Speed Optimization is a straightforward method to ensure that only the required energy is utilized to achieve better or the same metallurgical performance.
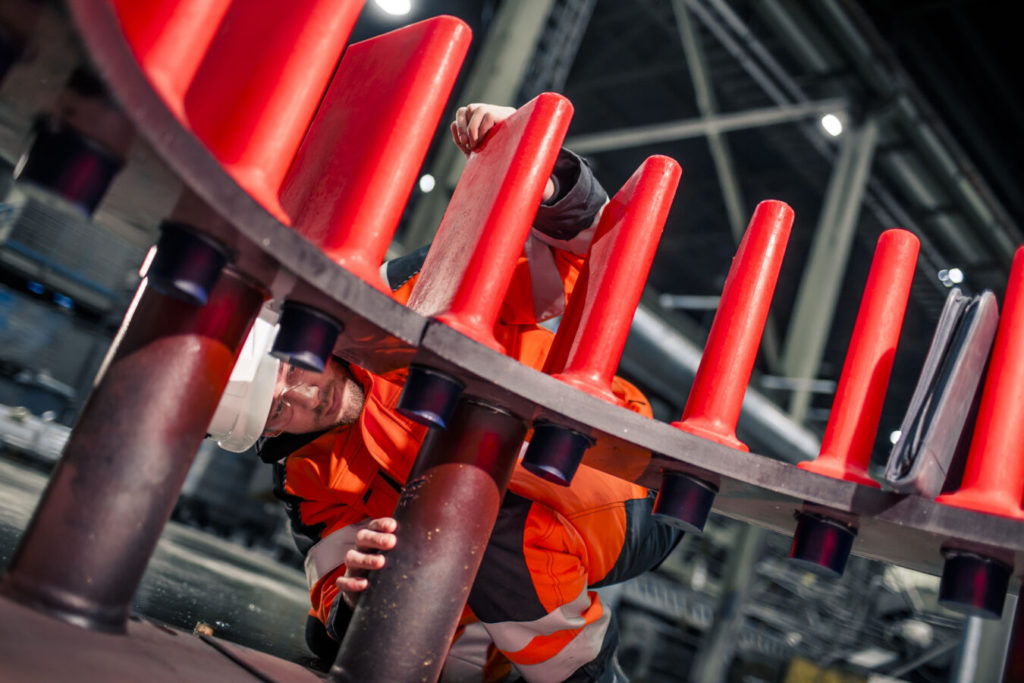
High-quality spare and wear parts: Improved circularity of your flotation machine is possible when extending wear components life. The result is less raw material usage, reduced maintenance shutdowns and transportation which will ultimately lead to an improved handprint.
Upgrade existing flotation machine
“Process optimization can only get you so far as you are working with the limitations of your existing assets,” says Bermudez. “ If your float cell is an older model and restricted by design, you might consider upgrading your equipment. “
Upgrades are a great way to get new life out of your existing equipment while only using a small portion of your budget. With many options to choose from, upgrades can be staged across multiple years, adding annual benefits while matching periodic CAPEX limits.”
Three key upgrades can be considered to significantly decrease CO2 emissions as well as reduce energy consumption:
- FloatForce Upgrade: FloatForce mechanism maximizes mixing and aeration inside the flotation cell. Upgrading your outdated flotation mechanism with FloatForce makes it possible to reduce the rotation speed up to 10%, resulting in approximately 20% savings in energy;
- Center Launder Upgrade: The Center launder upgrade can deliver substantial improvements in a key aspect of the flotation process: froth recovery. This is possible because by drastically reducing froth surface area and transport distance. This has a direct reduction effect in airflow rate resulting in roughly 24% of the blower’s power consumption and
- Concorde Cell Blast Tube Upgrade: The Concorde Cell is a new technology equipped with Blast Tubes that enables targeting ultra-fine particles recovery with high local energy dissipation, making energy usage more efficient. Upgrading your self-aspirated pneumatic flotation machine with Metso Outotec BlastTubes decreases plant footprint due to faster flotation kinetics.
“Optimizing and upgrading flotation performance can result in increased metallurgical recovery using existing equipment, meaning that the extra tons of valuable material have avoided the comminution step, which is by far the most energy-demanding portion in minerals processing,” says Bermudez.
“At one point though if the process changes place to high a demand on the existing equipment, then simply optimizing or upgrading may not be enough to match the new operational requirements. New equipment and technology should then be considered and can also bring significant production and sustainability benefits.”
New equipment for additional energy and water savings
The latest addition to Metso Outotec’s flotation equipment range is the Concorde Cell™, which sets a new benchmark in high intensity pneumatic flotation by recovering unachievable fine and ultra-fine particles, resulting in significant revenue gains and minimizing plant operating costs, energy and water consumption per metal production targets.
The Concorde Cell technology for improving fine and ultra-fine particle recovery is Metso Outotec’s proposition for more finely disseminated and complex orebodies. Combining the well-proven TankCell® with Concorde Cells is a low risk and high benefit approach for minerals processing flowsheets. The Concorde technology offers a superior recovery rate for fine and ultra-fine particles. The cell produces very high shear and extremely fine bubbles which increases recovery in particles under 20 microns.
The patented Concorde technology is the first fine and ultra-fine solution for complex and previously inaccessible ore types within various mineral processing flowsheets for gold, copper, nickel, platinum, silver, lead, zinc & molybdenum.
“The Concorde forced air Blast Tubes treat 100% of fresh feed combined with tailings recycling for improved performance, so it allows for finer grinding to get extra liberation without the risk of valuable particles being reported into tailings” says Alejandro Yáñez, Senior Manager, Concorde Technology.
The Concorde technology enables efficient use of the Earth’s resources with increased recovery of fines and smaller plant footprint, helping miners to minimize energy and water consumption per metal production targets. The Concorde Cell is part of the Planet Positive portfolio, which focuses on the most environmentally efficient technologies (>100) in Metso Outotec’s portfolio.
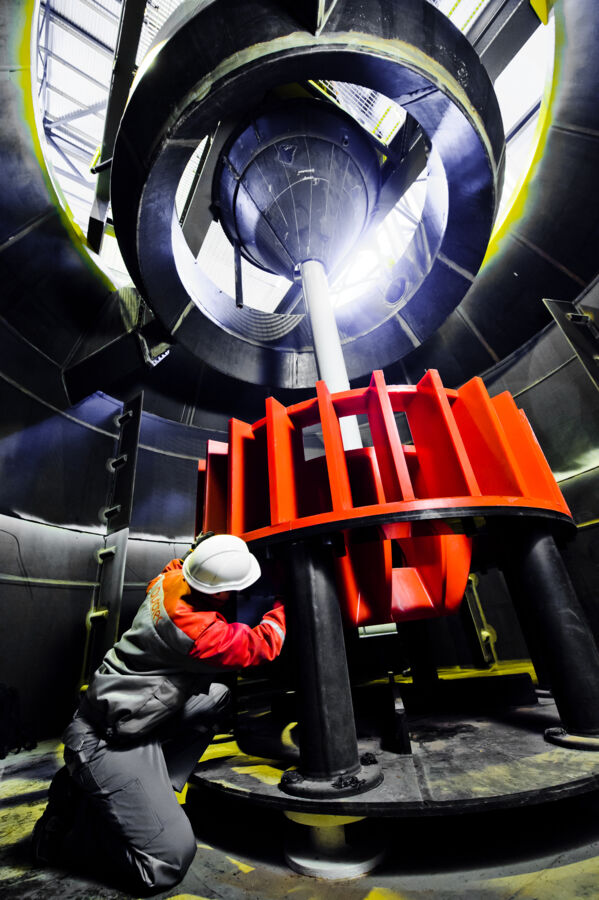
Sustainability and budgets – It’s about finding the balance
“In the end, it’s about balancing your budget with your desired sustainability targets. The correct solution depends on your circumstances. An overall plant review is the best place to start with a holistic outlook to determine the best solution. Whichever option is chosen will influence your overall sustainability efforts and requires a cost-benefit analysis.”
To help plant productivity reach targeted KPI’s from a sustainability point of view in energy consumption, and carbon footprint) or from an efficiency perspective, like poor recoveries of valuable minerals, poor continuity, identifying the obstacle and analysing and identifying the root cause of theoretical bottlenecks is key to reaching a goal.
Having the right analysis, which is deep and concise enough is crucial prior to making an optimization decision, including assessing the mechanical status of your cell.”
Bermudez says key questions to consider include: Have you studied the recent changes in your ore properties? Has there been major changes in the flotation feed? Have you assessed the viability of your operational strategy? Once the ore properties and its preparation have been properly addressed, then we can look into optimizing your cell performance.”
Learn more at Metso Outotec.
Sign up for Metso Outotec’s webinar on recovering ore value optimization here.
2 Comments
Robert Kanyika
We have a complex ore with Copper, Zinc, Gold and Silver all targeted in our recovery.
Robert Kanyika
Interested in improving of copper, zinc, gold and silver recoveries.