What to expect from the next generation of autonomous trucks

Hitachi says autonomous trucks are advancing their ability to communicate with one another and other pieces of equipment on the mine site.
“Our next generation of autonomous will see that the trucks actually become even smarter,” said Brian Mace, Manager of Mining Applications & Product Marketing at Hitachi’s Construction & Mining Division during an interview with MINING.com at MINExpo last month.
“They can kind of talk to each other, and make some of those decisions by themselves through the autonomous software.”
Mace says this will be especially useful in remote locations since control can be centralized. Mining companies won’t have to support so many personnel at remote sites.
“So it’s autonomy—the efficiency of having multiple people in one spot for multiple mine sites.”
Transcript edited for clarity.
MINING.COM: What are some of the changes you’ve made to bucket design to help customers?
Brian Mace: We specialize in looking at the customer’s application, the production schedule, the hollow roads, and the material, and match the shovel with the truck through to the correct fleet for that customer.
We do some things with the bucket area of the GET (Ground Engaging Tools). There are some different configurations for the ground engaging tools, also there are packages for different configurations. We work with some other companies that we help custom design the bucket for the application’s specific needs and for different kinds of materials. And then what we really try to do is match that bucket with the truck body to ensure that we get the correct payload in the truck.
MINING.COM: What are some of the technologies that you’re introducing at MINExpo?
Brian Mace: So, one of the biggest things we’re introducing here is our autonomous truck, and that’s in collaboration with not only Hitachi Construction Machinery, which built the product with our parent company Hitachi Limited, but also owns Wenco Mining, which is a mine management fleet dispatch system. Our message here is “Hitachi to the Core.” It’s a combination of all these Hitachi companies: the entire product technology. Everything is Hitachi, from the smallest ball to the largest piece of equipment that you can see standing behind me. We put it all that together. We’ve been able to bring our autonomous truck through from proof of concept to running on a site test right now. It’s in the second generation and coming soon it will be—in the next two years—pushed out to be commercially available.
MINING.COM: Why are customers interested?
Brian Mace: There is more efficiency at the mine site. Mines can control the operation. They get repeatable performance out of the truck, and reliability. I think with today’s technologies customers get a lot more information from the trucks.
Our next generation of autonomous will see that the trucks actually become even smarter. They can kind of talk to each other and make some of those decisions by themselves through the autonomous software.
This will be especially useful in remote locations—getting people to be able to maybe control the mine site from a central location versus having to run in different locations.
MINING.COM: What are the steps right now for a fully autonomous truck?
Brian Mace: I think all the technology—as far as the sensors that are on the truck goes—has been established through a proof of concept. The technology has been tested, and today we move from that generation to the next generation, which is the trucks that are working with mine equipment. So they’re working in a pit with other equipment that has operators in it, so all the technology is now being tested there within that operation.
I think the future is going to be software-related, getting the trucks to think for themselves and make critical decisions. And then there will be what the whole truck experiences: a soft spot on the road and then an extra truck comes and sees the same soft spot. The people back in the dispatch see that they can dispatch equipment out to repair the hole in the road. That’s the kind of feedback coming back from equipment in the field which is critical to maintaining the performance and efficiency of the equipment in the pit.
MINING.COM: Can you take me through the steps of making equipment autonomous?
Brian Mace: One of the nice things is that with the truck and all the technology being Hitachi you could buy a truck today for your mine site and it may not be autonomous on the site but in the future, if you wanted to go to autonomous, you wouldn’t have to replace the truck. You could take our technology and put it onto the truck and make the truck autonomous. You won’t have to replace your fleet. You can use the existing fleet and move forward to autonomous.
We do the same thing for our trolley trucks as well. You can buy a truck and put the components on it if your mine is going to go to a trolley application, you can put those components on the truck as well, so instead of having to reconfigure the product, we have flexibility.
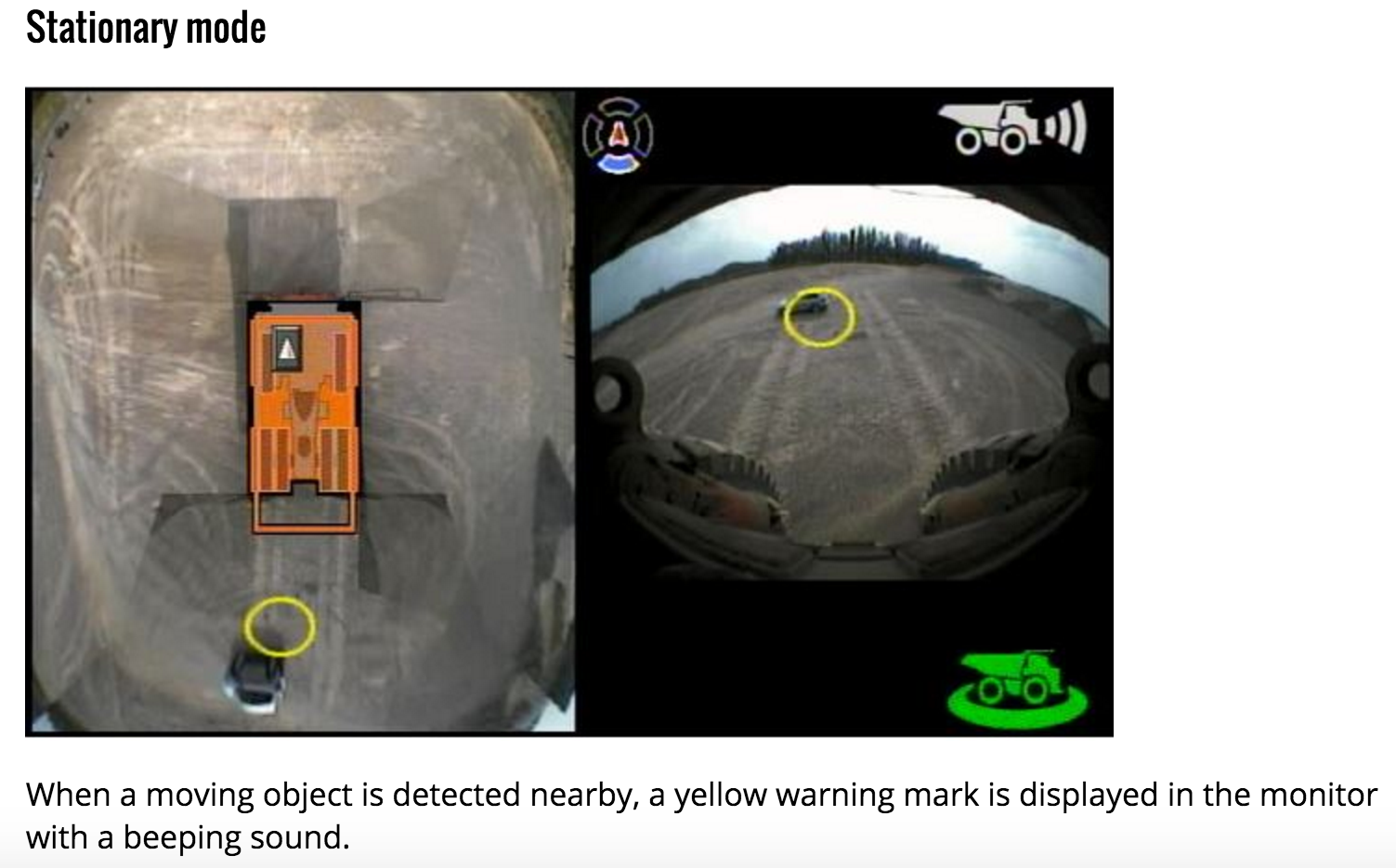
Hitachi’s Aerial Angle peripheral vision
MINING.COM: Can you tell me something about Aerial Angle?
Brian Mace: It’s a turn-around view monitor, so when either the truck or excavator are stationary, it gives the operator kind of a bird’s eye view—360 degrees around the equipment so they have full visibility around the equipment.
One of the enhancements we’ve done for the haul trucks is an alarm system. If there’s an object in the viewing area, the operator is notified through a visual and audible alarm system. And then, in addition to that, we have a fuller collision warning that measures if there’s an object in front of the truck and what is the stopping distance between that object and the truck, and if it’s necessary to apply which brake, and it would provide the warning to the operator.
Hitachi is a MINING.com advertiser
More News
RANKED: World’s biggest copper mines
April 18, 2025 | 11:21 am
{{ commodity.name }}
{{ post.title }}
{{ post.date }}
Comments