VW plans to be battery juggernaut in $29 billion answer to Tesla
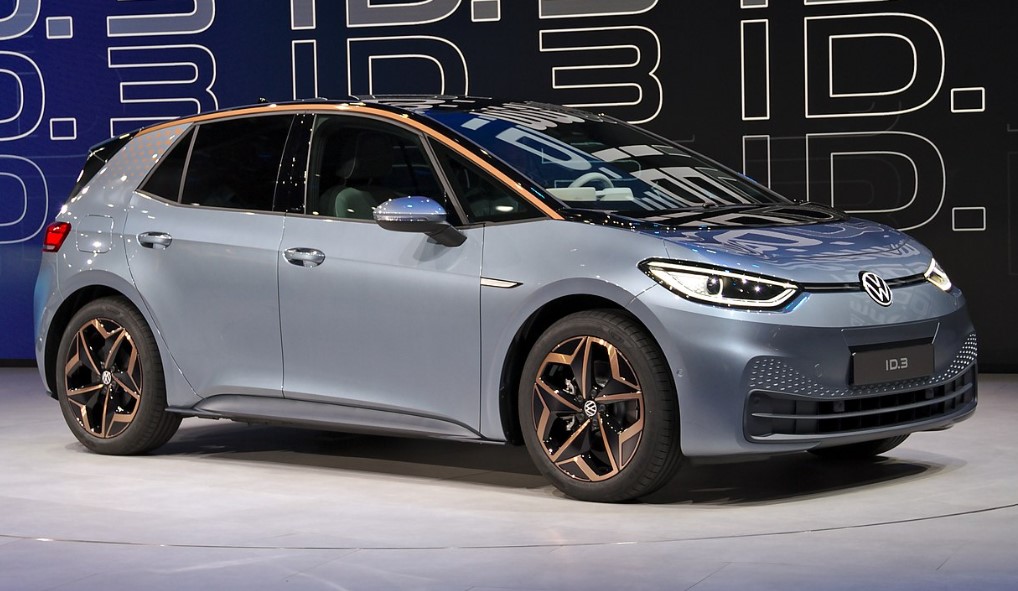
Volkswagen AG is stepping up efforts to unseat Tesla Inc. as the dominant electric-car maker with a plan to build six battery factories in Europe and invest globally in charging stations.
VW already has agreements for two battery plants and is exploring four additional sites for a total capacity of 240 gigawatt-hours by the end of the decade, it said Monday. The push will cost some $29 billion and would make VW and its partners the world’s second-largest cell producer after China’s Contemporary Amperex Technology Co. Ltd., according to BloombergNEF.
“E-mobility has won the race,” Chief Executive Officer Herbert Diess said during a webcast. “Our goal is to secure a pole position in the global scaling of batteries.”
Batteries have emerged as a key component in the electric-car race. After years of trailing Tesla and the bruising experience of the diesel-emissions cheating crisis, VW has switched gears to reorganize a sprawling behemoth from the ground up. The company boasts the industry’s most comprehensive EV push, with intentions to add about 50 purely battery-powered vehicles to its lineup by 2030.
VW’s battery factories will have a capacity of 40 gigawatt-hours each, and the company is looking for partners for most of them. The carmaker dropped a previous plan to join forces with Northvolt AB for its site in Salzgitter, Germany, and will make batteries there on its own. VW plans to construct a factory in France, Spain or Portugal by 2026 and one in Poland, Slovakia or the Czech Republic by 2027, plus another two sites at European locations that have yet to be identified.
“This is a huge announcement,” said James Frith, an analyst at BloombergNEF. “Building 240 gigawatt-hours of capacity will require around $29 billion in capex based on today’s manufacturing plants and technology.”
Sweden’s Northvolt will remain a key partner, winning a $14 billion order to supply cells to premium-car brands like Audi and Porsche. VW will boost its stake in the closely held startup from about 20% to an undisclosed higher level. VW didn’t elaborate on the status of existing agreements with SK Innovation Co. Ltd. and Samsung SDI.
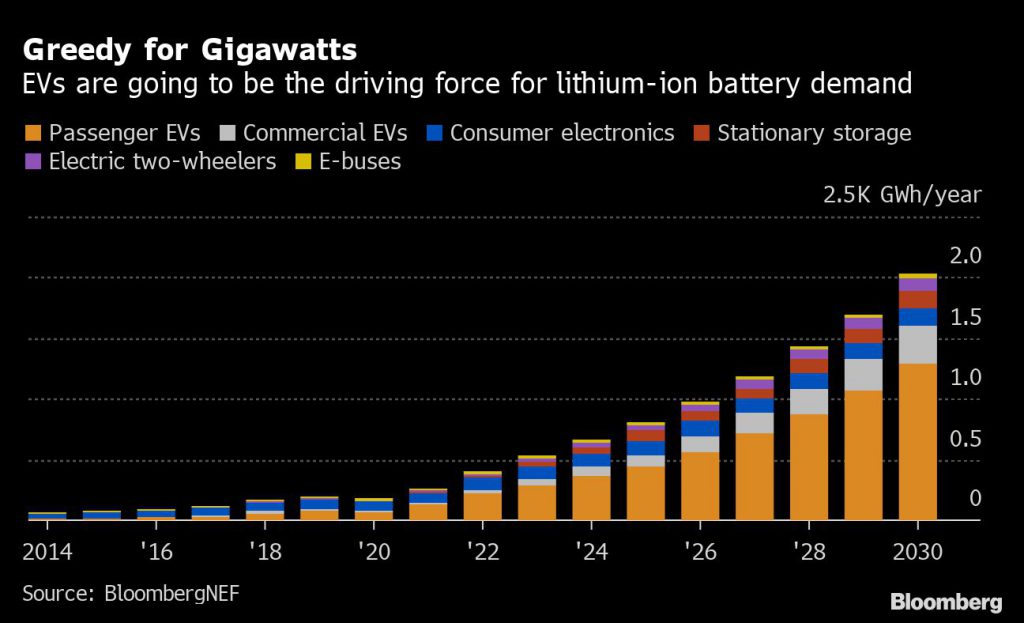
VW aims to at least double its share of deliveries that are fully electric this year, which could bring it within striking distance to Tesla’s EV sales. VW’s ID.3 hatchback and Porsche Taycan are based on dedicated underpinnings that stack up well against the maker of the Model 3. The German manufacturer plans to make some 26 million fully electric cars by 2030, highlighting concerns over battery cell costs, capacity constraints as well as raw material shortages.
Charging partners
Emulating Tesla as well as General Motors Co. with a dedicated battery event dubbed “Power Day,” VW gave its deepest dive yet on its strategy to beat a path to a future selling millions of EVs. It will invest 400 million euros ($477 million) by 2025 to build out much-needed charging infrastructure in Europe after the region overtook China in EV sales last year.
Fast-charging in Europe will grow five-fold to 18,000 stations, helped by cooperations with BP Plc in the U.K., Iberdrola SA in Spain and Enel SpA in Italy. In North America, VW is adding 3,500 stations this year and 17,000 points in China by 2025.
VW will offer bidirectional charging from 2022, a move that would change the way power grids operate by allowing car batteries to store excess energy and feed it back to the network in times of peak demand.
Cutting costs
VW plans to switch to new “unified“ cell design from 2023 to as much as halve battery costs. The company is also researching solid-state batteries that it says are cheaper to assemble and allow for faster charging.
“We will use our economies of scale,” said Thomas Schmall, VW’s head of technology. Battery costs will fall “significantly” below 100 euros per kilowatt-hour, he said.
Cell materials are in high demand and account for the biggest share of a battery’s cost, so securing supply before bottlenecks arise is key. Nickel is Tesla’s biggest concern for scaling production of lithium-iron battery cells, CEO Elon Musk said last month.
VW is bolstering recycling efforts and is focusing on partnerships to ensure adequate supply, it said. Its deal with Northvolt is similar to Tesla’s tie-up with Panasonic Corp., which dates back to 2009.
Rival plans
As carmakers scale up EV offerings, Tesla and other new entrants including Nio Inc. are stepping up their battery efforts as well.
China’s CATL is targeting close to 500 gigawatt-hours capacity by 2025, BNEF’s Frith said.
Tesla expects to add a battery-cell factory to its car-assembly plant under construction near Berlin. The site will initially have a capacity of more than 100 gigawatt-hours a year and eventually ramp up to as much as 250 gigawatt-hours, Musk said during a battery conference in November, without saying when the facility would be up and running.
(By Christoph Rauwald)
Read more: Cobalt, nickel free electric car batteries are a runaway success
More News
Lithium Americas reaches final investment decision for Thacker Pass mine
Once open, Thacker Pass is expected to produce 40,000 metric tons of battery-quality lithium carbonate per year.
April 01, 2025 | 03:05 pm
Gold retreats from record as traders brace for Trump’s tariffs
Traders are on edge as Trump plans to announce sweeping levies on all of America’s trading partners on Wednesday, raising the risks of retaliatory measures.
April 01, 2025 | 12:58 pm
{{ commodity.name }}
{{ post.title }}
{{ post.excerpt }}
{{ post.date }}
Comments