The ‘Right Way’ and the ‘Wrong Way’ to Build a Good Diesel Fuel Performance Additive
Introduction
There are many diesel fuel additive companies in North America supplying numerous different additive products formulated for diesel powered equipment. Each of these vendors claim their specific products are the best available to upgrade diesel fuel for the fuel producer, fuel supplier and final fuel consumer. However, actual testing has often proven to be just the opposite.
Nearly all diesel fuel additive suppliers make very generic product claims that their additive will “yield better fuel economy”, “increase engine power”, “reduce smoke”, “increase fuel lubricity”, “reduce system deposits”, “lower maintenance costs”, “save money”, etc. Unfortunately for the additive buyer, there is no ‘watch dog group’ who monitors diesel fuel additive advertisements and no oversight mechanism in place (anywhere in the world) to verify the stated product claims.
The proof of any diesel fuel additive’s performance is the sole responsibility of the purchaser of the additive product. While some fuel additive claims can be verified with laboratory testing, proving most claims can only be done in the field by treating the diesel fuel and actually running the additized fuel in the buyer’s daily fleet operations. Unless diligent steps are taken to laboratory ‘test the prospective product’ BEFORE the purchase is made, there is no guarantee the particular additive product chosen will meet any of the benefits claimed.
Diesel fuel additive testing begins with choosing a reputable ASTM qualified laboratory with established experience in testing diesel fuel additives. This too can be a bit of a challenge for the diesel fuel additive buyer but if the right questions are asked, a good laboratory can be found.
The laboratory search should begin with reviewing the current ASTM D-975 Specification for Diesel Fuels (1). This document lists the various physical parameters that must be met for all diesel fuels whether in an on-highway or off-road application. Unfortunately, the ASTM D-975 Specification(1) provides only the basic recommended physical fuel property boundaries and does not specifically address performance upgrades achievable with diesel fuel additives. However, many of the same laboratory tests described in ASTM D-975(1) can be used to precisely determine the enhancements achievable with a prospective diesel fuel additive.
The following pages detail the diesel fuel physical properties (and additive enhancements) required in order to improve summer diesel fuel to optimize its performance in today’s ‘common rail’ fuel injection diesel engines. The second article will address particularly important and relevant information regarding diesel fuel additives for today’s modern ‘common rail’ fuel injection engines during cold weather operations.
Discussion
Cetane Improver Additive (predominantly 2-ethylhexyl nitrate) is the main chemical additive component used for decreasing the ignition delay time (raising the fuel’s Engine Cetane Number). This improves combustibility of a diesel fuel. Improving combustibility of a diesel fuel by raising the Engine Cetane Number is important because there is a finite amount of time (microseconds) between fuel injection and exhaust during the combustion cycle in each cylinder.
A diesel fuel ignited at the optimum time before piston TDC (top dead center) of the compression stroke will correctly burn and release the maximum BTU (heat energy) from each fuel droplet during the power stroke. When this happens, all of the heat energy in the fuel will be converted into usable power pushing the piston down resulting in maximum horsepower produced from the fuel. This directly correlates into less unburned hydrocarbon emissions and improved fuel economy.
Enhanced fuel combustion manifests as less visible smoke emissions, reduced combustion chamber fuel related deposits, less post combustion EGR Valve and DPF deposit cleanings, fewer driver low power complaints and less vehicle downtime resulting from driver low power complaints.
The long standing ASTM D-975 Specification for Diesel Fuels(1) in North America only requires a minimum Engine Cetane Number of 40. While a few diesel fuel refiners produce diesel fuels well above this bare minimum number, some supply diesel fuels only two or three numbers above the minimum.
The overall average Engine Cetane Number of diesel fuels produced in North America ranges from 44 to 46 despite the fact that diesel equipment operators know engines run better on fuels with a much higher Engine Cetane Number. Cetane Improver Additive treating to enhance diesel fuels in North America is most often left to the diesel fuel purchaser.
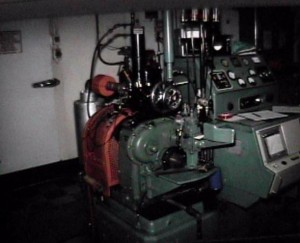
ASTMD 613 Engine Cetane Test Cell
In theory, ‘any increase’ in a diesel fuel’s Engine Cetane Number should provide some improvement in engine operation. However, only an increase of 4 to 5 Engine Cetane Numbers will actually be noticed by the driver. This is especially important with the increase of European diesel vehicles entering the North American markets. These diesel engines are designed to operate best on the European mandated 51+ Engine Cetane Number diesel fuels and indications are the European mandate will increase to 55+ in 2019 or 2020.
It is also important to note that an Engine Cetane Number increase of 4 to 5 numbers will be needed to effectively measure and document a significant fuel economy improvement. This is why it is so important to have any prospective diesel fuel additive tested with the buyer’s diesel fuel in an engine test cell under ASTM D-613 Test(2) procedures to verify the exact Engine Cetane Number increase possible with the additive.
Detergent Additive (predominantly amine based chemistry) is the major chemical additive component used to clean up existing fuel related deposits and keep them from reoccurring in the fuel delivery system. Detergent Additives also play a very important role in diesel fuel combustion and power production because any deposits in the fuel pumps or fuel injectors will negatively affect the spray pattern produced in the engine cylinders during each injection cycle.
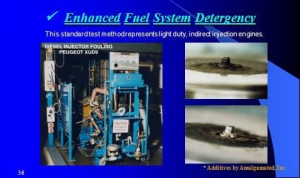
Peugeot XUD9 Fuel Injector Test Apparatus & Test Injector Tip Photos
If the fuel spray pattern droplets are not uniform or the amount of fuel to be injected is impeded or limited because of internal or external deposits on even one fuel injector, optimum combustion and maximum power production cannot happen.
This condition will produce increased smoke, more unburned hydrocarbon emissions and reduced engine horsepower for all throttle settings. The end result will be increased driver low power complaints and increased vehicle downtime.
Unburned diesel fuel related to poor fuel detergency also will increase deposits in the engine combustion chamber, escalate deposits in the post combustion areas (exhaust valves, EGR valves, DPF, etc.), increase fuel dilution in the crankcase oil and shorten the normal engine maintenance overhaul period. All of these situations will increase costs and decrease the useful life of the diesel powered equipment.
There is no ASTM test procedure or easy rating method to determine the detergent content in a diesel fuel or a diesel fuel additive. Likewise, there is no easy means to determine a detergent’s effectiveness in keeping the fuel injectors free of deposits and working properly.
The only recognized means today of testing diesel fuel detergency is the costly and time consuming DW-10 CEC F-98-08 Direct Injection Common Rail Diesel Engine Nozzle Coking Test(3). All diesel fuel additive suppliers should be required to ‘certify’ that their particular additive product treated at the recommended treat rate will achieve a DW-10 Pass Rating.
This diesel engine injector test is conducted over a 72-hour test cycle period of alternating high speed/load and low speed/load to determine the power loss resulting from fuel injector deposits. The test uses a European Peugeot 4-cylinder, 2.0 liter direct-injection turbocharged light-duty common rail engine with maximum injector pressure of 1,600 bars.
The DW-10 CEC F-98-08 Test is conducted for a specific amount of run time using a base diesel fuel treated with 1ppm of zinc (in order to increase injector deposits). As the fuel injector deposits increase, fuel flow through the injector will decrease and power production will decrease. The same diesel fuel treated with detergent additive is tested for the same time period and the fuel flow through the injector and power production is compared to the non-additized run time. A power loss of less than 2 percent during the test with detergent treated fuel is considered a ‘DW-10 Pass’ of the test.
Lubricity Additive (non-acid synthetic type) is an important diesel fuel additive component because the diesel engine fuel delivery system is lubricated by the diesel fuel itself. If the lubrication value of the diesel fuel is less than adequate, the fuel pumps and injectors will not work properly and increased wear will occur.
Today’s diesel engine fuel injectors are designed to operate with extremely high injection pressures (35,000 psi and more) in order to better atomize each fuel droplet. Additionally, fuel is injected multiple times through extremely fine injector tip holes during each injection cycle in the excessively high temperature environment of each engine cylinder.
If the fuel does not provide proper lubrication to the system, the fuel injectors lacking proper lubrication will ‘stick’ causing a chatter-like noise and the required amount of fuel will not be injected. The net effect will be incomplete combustion, poor power production at all engine power levels and reduced fuel efficiency. Ultimately, without adequate fuel lubrication, the engine will seize.
Diesel fuel additive buyers should undertake their own laboratory testing for diesel fuel lubricity value enhancement using the ASTM D-6079 HFRR (High Frequency Reciprocating Rig) (4). This precise test procedure requires only 90 minutes of laboratory time and can be accomplished with a small amount of diesel fuel and additive to verify the lubricity enhancement claim.
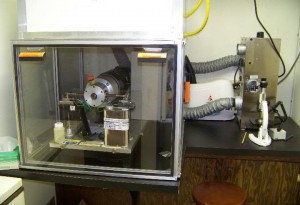
Two Place HFRR Lubricity Test Apparatus
The HFRR test method uses the measurement of a wear scar produced on a small metal ball reciprocated against a polished disc immersed in the subject diesel fuel. The result is a simulation of the expected wear internally in fuel injectors and pumps in the diesel fuel delivery system related to the fuel lubrication value.
Improved fuel lubricity will result in a decreased HFRR wear scar measurement and a correlation to better lubrication of the fuel delivery system.
While the current ASTM D-975 Specification for Diesel Fuels(1) shows a maximum HFRR wear scar of 520 µm, the USA Engine Manufacturers recommend a 460µm maximum rating for fuel lubricity. European Engine Manufacturers have lowered their recommend HFRR fuel lubricity to less than 400µm of wear scar. This is important because America is experiencing a significant influx of European diesel powered equipment all manufactured with common rail fuel injection systems and all new diesel engines being built today in the USA incorporate common rail fuel injection.
Improving the lubricity value of the diesel fuel will decrease component wear and insure maximum life expectancy of the fuel delivery system. This will keep maintenance costs lower and reduce fuel system downtime hours over the life of the vehicle.
Stability Additive is the fourth important chemical component required to protect diesel fuel and insure optimum performance in an engine. Diesel fuel is an organic product and like all organic products it degrades (oxidize and breakdown) at some rate from the time it is refined until it is consumed.
Rating diesel fuel’s rate of oxidation (instability) through laboratory testing determines the extent of degradation that will take place in the fuel between its manufacture and its use. This rating is important because as a diesel fuel oxidizes (degrades) it will generate very fine free carbon particulates which are very abrasive and tend to collect internally in fuel injectors.
Unstable fuels also manifest in the fuel system as varnishes that coat and cause scoring of the moving parts. Varnishes cause sticking of injectors so delivery of the proper amount of fuel to the engine does not happen. This eventually will stop the engine entirely.
Unstable diesel fuels also will create sludge materials that collect and build up in low areas of the fuel storage and delivery system (i.e. tanks and lines). The longer an unstable fuel is used, the more degradation byproducts will be formed.
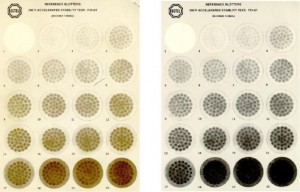
Dupont F-21 Stability Chart – Pad Readings
A measure of diesel fuel thermal stability can be determined in a petroleum laboratory using the well-known ASTM D-6468 High Temperature Stability of Middle Distillate Fuels Test(5).
The test pads can be visually rated (using the charts to the left) to define the free carbon created during the test or analyzed using a laboratory light reflectometer. The more carbon created during the test, the less light will be reflected in the reflectometer (lower reflectometer result).
Diesel fuels treated with a ‘good Stability Additive’ will have test pad ratings of 2 or less and a light reflectometer result greater than 90 percent.
While a quality stabilizing additive can be used to dramatically slow the degradation of a diesel fuel, it is impossible to completely stop the natural diesel fuel degradation process. It is important for a diesel fuel user to have his base (incoming) diesel fuel tested for stability in order to determine the ‘state of degradation’ before treating with a stabilizing additive product.
The diesel fuel user should have his prospective Stability Additive tested at the same time in the same base (incoming) diesel fuel in order to determine whether or not the Stability Additive will, in fact, stabilize his diesel fuel. It should also be noted that some of the other performance additive products can negatively affect the oxidation rate (stability) of a diesel fuel. For this reason the diesel fuel purchaser should have his fuel treated with any other additives his is using and then stability tested and, if necessary, extra Stability Additive should be added to the fuel in order to counteract the negative effects of the other additives.
Corrosion Inhibitor Additive is another very important chemical compound that needs to be added to diesel fuels because (a) all diesel fuels naturally contain water which is corrosive and (b) all water contains dissolved salt which will create deposit build up in fuel injectors.
While the diesel fuel water content may be small (typically 40ppm to 100ppm), that amount of moisture is more than enough to cause rust and corrosion in all parts of the fuel delivery system. Though the salt content in the water may seem extremely small (typically a few parts per billion), the dissolved salt particles continually circulate throughout the fuel delivery system during operation.
Since most diesel engines return 75 to 80 percent of the diesel fuel back to the vehicle fuel tank as ‘return fuel’, the same salt particles can flow through the injector more than 500 times during the consumption of one tank of diesel fuel. This gives ample opportunity for the salt particles to stick and form a deposit build up inside the fuel injector. When this occurs the fuel injector will cease to function and engine power production will diminish causing a driver low power complaint and downtime.
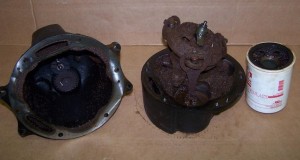
Diesel Fuel Storage Tank Pump/Meter Assembly & Island Filter With Fuel Corrosion
The picture to the left shows the corrosive effects a diesel fuel can have on the fuel delivery system in a diesel fueling facility (after six months of continual use).
The same corrosive effects can occur in fuel injectors and pumps during the operation of a diesel engine.
An ASTM D-665 NACE Spindle Corrosion Test(6) should be conducted to determine the effectiveness of Corrosion Inhibitor Additive. A NACE 1-A or better result with the “correct” Corrosion Inhibitor Additive will indicate fuel related corrsion and rust will be prevented when the additive is treated at the correct dosage rate in the diesel fuel used.
The first photo (to the right) shows a diesel engine fuel injector pintle ‘with excessive corrosion’ caused by using diesel fuel without corrosion inhibitor.
The second photo (to the right) shows a diesel engine fuel injector pintle ‘without corrosion’ resulting from using diesel fuel treated with effective corrosion inhibitor additive.
There can be no doubt the first pintle (with corrosion) will not operate properly in the injector nor allow the correct amount of diesel fuel to be supplied into the cylinder. Excessive fuel injection corrosion will ultimately stop the engine operation entirely.
Deposit Modifier Additive is the final important chemical component required especially in diesel fuels for engines with today’s high performance common rail fuel injection systems. The proper amount of diesel fuel Deposit Modifier Additive treated continually in the diesel fuel used will:
- Keep the intake valves and exhaust valves and pistons tops cleaner to reduce ‘hot spots’
- Keep the EGR Valves free of excessive carbonaceous build up and reduce replacements
- Keep the Diesel Particulate Filter unit cleaner which will reduce regeneration frequency
- Keep the entire exhaust system cleaner and extend its useful life before replacement.
Although nearly all diesel fuel additive suppliers make a claim for ‘reducing fuel related deposits’, there is no laboratory test method for determining the amount of Deposit Modifier Additive included in a diesel fuel additive product. The only means of verifying the benefits claimed is to actually run the additive treated diesel fuel in an engine for an extended period of time.
The prospective diesel fuel additive buyers can request a written certified statement from the additive supplier that the additive product being supplied does include adequate Deposit Modifier Additive to reduce or minimize fuel related deposits. This tactic may eliminate some exaggerations from untrustworthy and unscrupulous diesel fuel additive suppliers and help to insure the additive buyer receives a product worth the money spent.
Summary
There is no one watching over the advertising used to market diesel fuel additives. Therefore, many performance claims are nothing more than ‘marketing fluff’. This article (and the subsequent one) is drafted to assist the additive buyer in sorting out what can and what should be done in order for the buyer to source the best performance additives for his diesel powered equipment.
References
- Diesel fuel specification published by the American Society for Testing of Materials
- Diesel fuel Engine Cetane Number test method published by American Society for Testing of Materials
- Diesel fuel injector coking testing procedures published by The CEC – Coordinating European Council
- Diesel fuel lubricity test method published the American Society for Testing of Materials
- Diesel fuel thermal stability test method published by ASTM
- Diesel fuel spindle corrosion test method published by NACE International
Note: The data and statistics presented herein are only a representative sample of the multitude of lab and field testing that Amalgamated, Inc has undertaken over the past 43+ years to document and verify the validity and performance of the diesel fuel additive products it sells. Amalgamated, Inc encourages all fleet owners and diesel fuel users to test and verify the performance and compare the cost effectiveness of diesel fuel additive products BEFORE they purchase any add.
{{ commodity.name }}
{{ post.title }}
{{ post.date }}
Comments