Potential … with a grain of salt
This article was originally published on Crain’s Detroit Business.
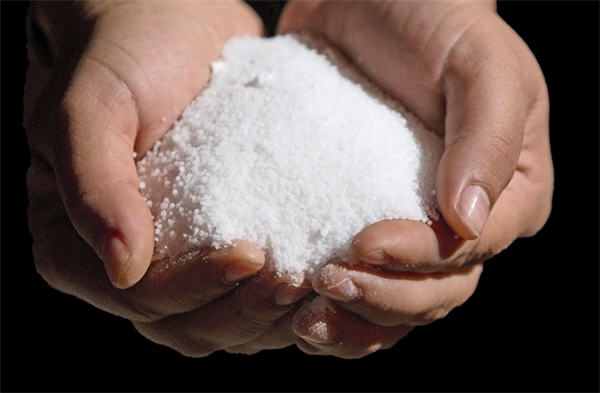
Think of your hand as Michigan. You’re holding in your palm a stash of potash that recently created a multibillion-dollar buzz. But sift through that a bit. | Image from Bloomberg
Only weeks after a swirl of media reports trumpeted that potash soon may become a $65 billion industry for Michigan, the owner of the only potash mine in the state stopped production of the mineral and laid off a dozen workers.
Plymouth, Minn.-based Mosaic Co. — the world’s fourth-largest producer of the mineral that America’s breadbasket uses as a fertilizer — has been trying to unload its potash mine in Hersey, east of Reed City, for years. It once considered closing the facility, which employed about 30 full time and 60 contractors before the layoffs in November.

The Mosaic Co. plant in Hersey, Mich., epitomizes the hurdles that must be cleared to make money mining potash in Michigan. | Image from Matthew Gryczan
Compared to Mosaic’s other potash mines in Canada and the United States, Hersey has remained a pipsqueak since it started production in 1989.
Potash mining here is further stymied by the collapse of prices resulting from disagreements between members of an international oligopoly that kept prices stable. In the summer, leading potash producers in Russia and Belarus launched a price war that pushed potash prices to their lowest level in three years, causing stockpiles to form in countries such as Brazil and China.
Some industry observers say it may take more than a year for prices to start moving up again — and only if production is cut now.
Yet two exploration and development companies are staking their futures on what they say is tremendous potential for potash in Michigan. Toronto-based Great Lakes Potash Inc. thinks that future will be centered on Midland, while Denver-based Michigan Potash Co. LLC is betting on the Hersey area.
Together, the companies control mineral rights to mine potash on nearly 50,000 acres of land above a 14 million-acre subterranean basin that approximates to the palm of your right hand if it were a map of Michigan. Representatives of both companies are lining up investors to fund the next steps, which include exploration wells, pilot plants and fully operating mines that carry a price tag in excess of $1 billion each.
Everyone seems to agree that making money on Michigan potash isn’t a get-rich-quick scheme. It will take years to get production from mines that ultimately would require financial backing of some of the world’s largest corporations — a daunting proposition when the price of potash has cratered on international markets.
“The timing (of plans in Michigan) couldn’t be worse at this point,” said Nathan Elliott, president of Insight West Research, a Regina, Saskatchewan-based research firm that follows the natural resource and energy industries for companies such as Mosaic. “Potash Corp., the largest producer of potash in the world, just cut its workforce by 18 percent, affecting just over 1,000 jobs,” because of oversupply.
“But in the grand scheme of things,” Elliott said, “I think Michigan is a major play. The world is basically wanting what Michigan has — and that is food, fuel and fertilizer.”
Today’s instability in prices likely will diminish by the time mines in Michigan would come on line, he said.
If potash reserves in Michigan are close to the estimates he has seen, “the numbers are staggering,” Elliott said. “If that is the case, Michigan could be in for a wonderful ride.”
Based on those estimates, Great Lakes Potash and Michigan Potash want to stake claim now because of Michigan’s proximity to vast agricultural markets.

Ian Colquhoun, president and CEO, Great Lakes Potash
“Based on what I know, Michigan has one-sixth of the world’s resource of potash, and nobody is talking about it,” said Ian Colquhoun, president and CEO of Great Lakes Potash.
“If you’re going to play in the commodity space and you can’t make it work when commodity prices correct themselves, then you ought not to play,” said Ted Pagano, general manager of Michigan Potash.
Different name, but still the same
Hersey epitomizes the hurdles that must be cleared to make money mining potash in Michigan. The deposits are about a mile and a half underground — so deep they can’t be dug and moved as solid rock profitably. Instead, mining companies force hot water down one cluster of wells to dissolve ores that contain potash and common table salt. Another cluster of wells leading to the processing plant removes the resulting brines.
Just drilling one well can cost more than $2 million.
When it gets to the processing plant, the potash — potassium chloride, an element essential for plant growth — is separated from sodium chloride, which can make fertile soil barren. About two-thirds of the production at Hersey is sodium chloride now, but the mine yielded a higher percentage of potash when it started production.
The relatively pure salt at the Hersey plant is bagged and sold for water softeners and other uses, while the remaining potash solution is reheated and pumped back underground following the halt in production last month.
Hersey never played a significant role in the overall production by Mosaic, which inherited the mine when the company was formed in 2004 by the combination of IMC Global Inc. and Cargill Inc. In fiscal 2013, the mine accounted for a little more than 1 percent of Mosaic’s finished potash product.
Besides ending potash production at the mine, Mosaic also continually has let its mineral leases lapse, allowing Michigan Potash to begin acquiring them in 2010.
“Mosaic has made the decision to decommission the Hersey potash facility and sell it as a salt mine with the best interests of our shareholders in mind,” Rob Litt, Mosaic’s senior manager of corporate communications, wrote in an email. “This allows Mosaic to focus our on strategic priorities and investments that drive long-term value.”

Ted Pagano, general manager, Michigan Potash
Litt would not comment further on the decision to convert Hersey into a salt mine only.
Pagano, who said his company has leased about 14,000 acres on all sides of the Hersey plant, said Mosaic refuses to sell the mine to any company that would be a competitor in potash production.
The mine isn’t by any means played out, and it is profitable, said Pagano, who employs some of the engineers laid off from the Hersey mine. Although it has been producing lower amounts of potash with its current wells, more well clusters could be drilled on surrounding land to continue mining in richer potash deposits.
So if mining potash is commercially viable in Michigan, why is Mosaic exiting when it already has a significant investment in plant and mineral leases?
Both Pagano and Colquhoun said Hersey has been little more than a distraction for Mosaic, a $10 billion company with holdings in Canada and the United States.
And an expensive distraction at that, given the amount of technological upgrades needed to improve profitability, both men said.
“The mechanisms that they’re using for solution mining are 1964 vintage,” Pagano said. “We’ve come a long way in crystallization and co-generation technology.”
Said Colquhoun, “When I talked with my engineer about how they configured their wells for injection and production, he said immediately, ‘Oh, that’s a loser.’ ”
Another drawback: a lack of cheap transportation.
“You can’t go to a high-production facility because it doesn’t have rail,” Colquhoun said of the Hersey location. “When you look at Hersey, there is nothing but bags and bags of salt outside waiting for trucks. With no way to transport potash in bulk, they were doomed to be a small operation.”
Early owners of the plant apparently saw the problem. Lawrence Trombley, a proprietor of the Hersey Roller Mills store in the center of the village, said the predecessor company of Mosaic was interested in repairing a railroad trestle and laying two miles of spur line to connect its mine with the Pere Marquette railroad line that linked Hersey with the port of Ludington and other Michigan cities until 1987.
But in the early 1990s, advocates of turning underused rail rights of way into recreational trails for hikers, bicyclists and snowmobilers succeeded in tearing up the tracks and converting the property into trails, Trombley said.
Mosaic has been a good corporate citizen for Hersey, Trombley said, supporting the community through construction of a public playground and sponsoring tractor pulls by Lodge 196 of the Independent Order of Odd Fellows. Trombley was philosophical about the layoffs and potential change in ownership.
“I think this is a blip,” said Trombley, who has lived in Hersey since 1969. “Someone will operate it — there’s too much investment there. It’s not going away, just going to be run under a different name.”
2 paths to potash production
It’s to Michigan’s benefit that Great Lakes Potash and Michigan Potash have two distinct approaches to tapping into what both companies say is a remarkable resource in potash and salt, the residue of where a prehistoric sea once covered Michigan.
The Lower Peninsula is actually a huge basin of sedimentary rock sloping gradually toward the center, which once held a salt-filled sea. As the sea began evaporating more than 350 million years ago, it left behind naturally occurring brine and minerals such as salt, potash and gypsum.
Before the Civil War, a slew of companies began to extract brine from the Saginaw Valley to produce salt, making Michigan the top producer of salt in the United States from 1880 to 1892. From the Saginaw Valley, salt producers soon expanded into Bay, Gratiot, Huron, Iosco, Isabella and Macomb counties — the general region where Colquhoun sees his opportunity.
Great Lakes Potash is the first company to hold mineral rights in Michigan to mine potash on public lands, he said. The company intends to commercialize deposits first identified by Kaminak Gold Corp. in its research of the Michigan basin, beginning in 2008. To concentrate on its mission to explore for gold, in 2011, Kaminak sold options on its leases covering nearly 34,000 acres and its proprietary database of high-grade targets to Great Lakes Potash. Great Lakes intends to lease an additional 22,000 acres in the near future, Colquhoun said.
Great Lakes Potash has three primary areas of interest that cover blocks of public land in or near the Cadillac State Forest Area, the Gladwin State Forest Area and acreage directly west of Midland, where it intends to sink its first exploratory well by March.
The company raised about $2.2 million in the spring of last year and plans to raise an additional $5 million to start exploration, which may entail drilling more than eight more wells to identify the optimum site to locate a pilot plant, Colquhoun said.
He is working full time under a consulting contract with Great Lakes Potash along with Dan Weir, who serves as executive chairman. Colquhoun has engaged experts from Kalamazoo, Grand Rapids and Midland to provide legal and technical help.
Colquhoun said he has mapped the best spots in a 5,000-square-mile area using data logs of about 250 wells that have yielded “real, real hard numbers” that he could use for exploration.
“Our estimates based on our three top project areas indicate we are looking at about 11 to 14 million tonnes (metric tons, or about 2,200 pounds) per square mile of economic, high-grade potash,” he said. “Even at 10 million tonnes per square mile in this 5,000-square-mile area, that is a resource worth about 50 billion tonnes of potash.”
Based on the assessment, “Michigan makes up a resource that no one knew before,” Colquhoun said.
According to the U.S. Geological Survey, the proven reserve of potash around Hersey totals 40 million metric tons. Colquhoun said the USGS estimates the worldwide resource potential is 250 billion metric tons.
“We would like to be the beginnings of the next Dow Chemical,” he said.
That could turn out to be a boon for Michigan because of royalties from potash production. Tom Hoane, a geologist with the Michigan Department of Natural Resources Minerals Management Section, said the state would receive a 5 percent royalty on sales of potash from state lands. It collects rental fees of $3 an acre now, along with mineral leases.
“Michigan has so much going for it. There’s rail, divided highway, natural gas, cheap electricity, all the things that make your project work — all sitting by Midland. And Midland is accustomed to deal with brine, pipelines and production plants because of Dow Chemical.”
Midwestern states such as Illinois, Iowa, Indiana, Ohio, Wisconsin and Michigan together use millions of metric tons of potash annually, comparatively “right around the corner” from producers in Canada, along with New Mexico and overseas.
As for timing, Colquhoun estimated it would take about four more years to complete the exploratory work and engineering, with two years to build a mine to tap the resource.
Pagano said Michigan Potash has a “shovel-ready project” by concentrating its efforts on tapping sites in Osceola and Mecosta counties where exploration largely has been completed and an operating mine shows feasibility.
With his associate, Kevin Latimer, Pagano is actively seeking private partners and public support for his project, which could break ground in the middle of next year and be completed three years later.
Neither Pagano nor Latimer would give specifics on the number of current investors, amounts raised or other specifics on Michigan Potash.
Pagano said plans call for a relatively small mine near Hersey costing about $450 million with capacity to produce 300,000 metric tons of potash annually and the potential to bolt on 700,000 additional metric tons annually for a total cost of $1 billion.
“Our pilot plant is Hersey, so we know that it works,” said Pagano, who has been in discussions with Mosaic for the past two years to buy the mine. But the potash producer is not interested in selling to anyone that would be a competitor.
With regard to transportation, Pagano pointed to truck-rail loading options in Baldwin, Cadillac and Clare and barge options in Bay City and Muskegon, where product could be transported to LaPorte, Ind., or down the Mississippi River.
“If you look at the overall trend — 10 years moving forward — it’s looking really, really rosy for potash,” Elliott said. “Saskatchewan has benefited from an extremely nice run in potash production, and five to six years is a really good wheelhouse to aim for in Michigan.”
Matthew Gryczan: (616) 916-8158, mgryczan@crain.com. Twitter: @mattgryczan
More News
{{ commodity.name }}
{{ post.title }}
{{ post.date }}
Comments