Metso Outotec launches Nordberg HP200e cone crusher range evolution for higher performance
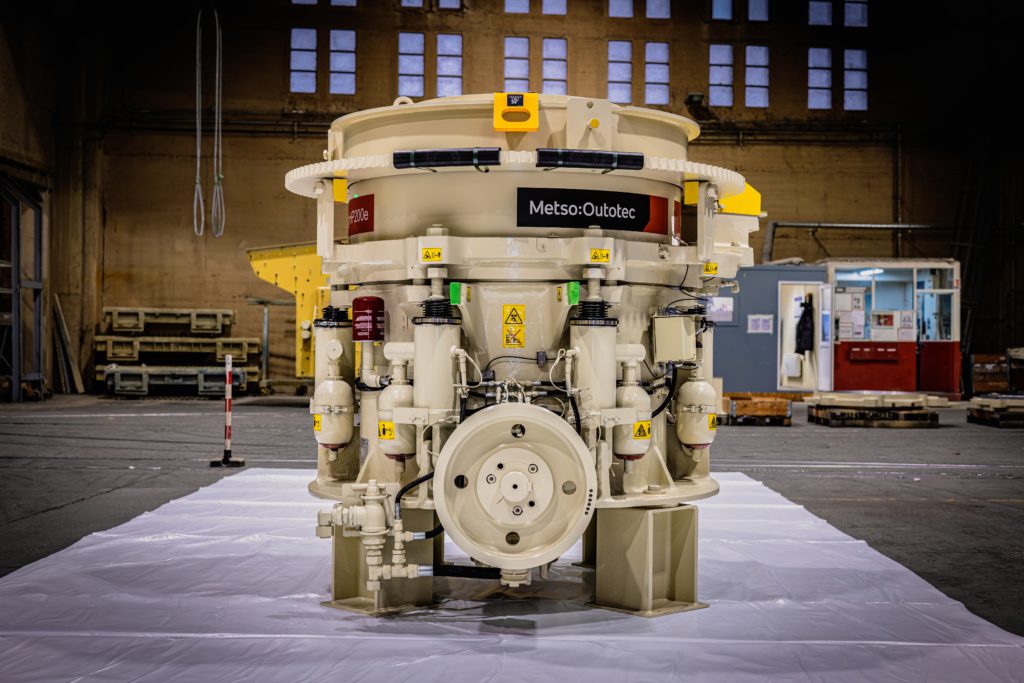
As a result of continuing cone crusher technology development, Metso Outotec introduces a new HP200e cone crusher to the aggregates markets, providing more performance and uptime in a more sustainable way, enabled by kinematics and new chamber designs. The new liners are fitted in the crushers without backing material, making maintenance breaks shorter and the liner replacement faster, safer and less hazardous for the environment.
”The evolution of Metso Outotec’s cone crusher technology brings multiple benefits and present a true evolution for aggregates producers in terms of performance, uptime, serviceability and application coverage,” says Ilkka Somero, Product Manager, Nordberg HP Cone Crushers in Metso Outotec.
”The concrete benefits include enhanced performance, +10% more head motion, +20% more kW power, +20% more force, new more efficient chambers, an anti-spin brake for higher uptime, serviceability improvements and a feed cone lifting tool. Environmentally, the new HP200e crushers are also a more friendly solution, as they do not require backing material. We are truly happy to be able to offer this latest evolution of our leading crusher technology to our customers,” he continues.
Metso Outotec ensures strong aftermarket support and availability for the HP200e crushers. The majority of spare parts in the current HP200 and the new HP200e are common, which will enable continued global spare part support for new units. Metso Outotec has established a start-up inventory for HP200e specific parts in Europe and North America. Further, a full scope of HP200e crushing chambers will be available in main stocking locations for the launch markets.
Metso Outotec also provides a head&bowl upgrade kit for the existing HP200 cone crushers, allowing the installation of no-backing chambers and for customers to enjoy the same health, safety and environmental benefits as with the new HP200e model.
More News
Rio Tinto in talks to develop lithium deposit in the DRC – report
Roche Dure has the potential to be the largest lithium mine outside Australia.
March 28, 2025 | 08:11 am
BNP Paribas predicts copper ‘collapse’ once tariffs take effect
After topping $10,000 earlier in the week, prices fell for a third day in London.
March 28, 2025 | 07:39 am
{{ commodity.name }}
{{ post.title }}
{{ post.excerpt }}
{{ post.date }}
Comments