How Norilsk Nickel reduced maintenance downtime by 86 pct
Norilsk Nickel Harjavalta Oy (NNH), located in Finland, is a member of the Norilsk Nickel Group and develops competitive products and production technology. NNH employs 230 people and produces roughly 60,000 metric tons of nickel chemicals and nickel metals annually.
Quant, with a 25-year track record in the industrial maintenance field, has been responsible for maintenance operations at Harjavalta Industrial Park since 1999, and the Total Maintenance Outsourcing agreement with Norilsk Nickel Harjavalta Oy was recently renewed again for another 3-year term starting in 2015.
Tommi Heikkilä, Maintenance Manager at Norilsk Nickel Harjavalta, explains why NNH wanted to continue the Total Maintenance Outsourcing agreement:
Learn how Quant can help you optimize maintenance costs and improve plant performance
“We wanted to make sure the development of maintenance continues as it had before, and we saw that Quant has the capability to continue this development,” says Tommi Heikkilä. “We have had, and will have, many process changes that Quant have adapted, and will adapt to, together with our joint strategy. This requires the maintenance functions to be very flexible and the communication in this partnership plays a key role. Our common target is to optimize OEE and secure the most efficient utilization of our assets.”
The current maintenance plan also pays special attention to predictability and the improvement of maintenance disciplines. According to NNH’s Senior Manager, Plant Services Kimmo Tuomi, unnecessary production breaks are avoided by executing a service program every four weeks. This includes continuous onsite condition monitoring.
Increased emphasis on OEE (Overall Equipment Effectiveness) has also improved technical availability, which has risen from 96.7% to 99.6% between 2003 and 2010. This represents a decrease of 86% in production losses.
Benefits
- Maintenance has managed to improve effectiveness even when the production process has changed significantly
- Lost production volume due to maintenance downtime has decreased by 86% between 2003 and 2010
- Technical availability of production reached 99% in 2008 (96.7% in 2003) with availability levels at steady 99.4% – 99.6% (2008-2010)
Jose Baptista, Development Manager for Reliability at Quant says “The overall technical and methodical scope of maintenance has changed over time. Today maintenance is not restricted to simply repair the equipment when it breaks, it also has influence on the sustainable development of society as it influences the environment, safety of personnel and facilities, energy efficiency and financial aspects. Companies that previously considered maintenance simply as a source of spending, increasingly have become aware that maintenance is, without any doubt, a critical factor to remain competitive.”
Learn more about industrial maintenance and future trends, White Paper by Jose Baptista
Quant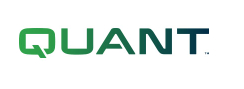
Quant is a global leader in industrial maintenance. For over 25 years, Quant (formerly ABB Full Service) has been realizing the full potential of maintenance for their customers. From embedding superior safety practices and building a true maintenance culture, to optimizing maintenance cost and improving plant performance, our people make the difference. Quant is passionate about maintenance and proud of ensuring they achieve customers’ goals in the most professional way. For further information about Quant, please visit www.quantservice.com
Read an interview with Quant’s Industry Segment VP Mining & Minerals and learn how the company has developed the full potential of human capital for maintenance of their mining customers.
How can Quant help you? Find your nearest office location here or email info@quantservice.com.
Keep up to date with Quant, subscribe to Quant plus magazine here.
More News
{{ commodity.name }}
{{ post.title }}
{{ post.date }}
Comments