BeltGenius ERIC: Digital twin increases the performance of belt conveyor systems
York, Pa. / Crailsheim, Germany: 2 August 2018 – BeltGenius ERIC (Efficiency and Reliability Intelligent Control) from Voith analyzes a range of data to determine how efficiently the belt conveyor systems of a mine are operating. Standardized values make it easy to compare individual conveyors. This gives mine operators numerous starting points for increasing the productivity of their system, while also lowering energy consumption and thus cutting carbon dioxide (CO2) emissions.
BeltGenius ERIC is a new software solution developed by Voith. It allows mine operators to gauge the efficiency of their conveyor belt systems at a glance. The gathered data provides operators with numerous starting points to optimize their system, thereby reducing operating costs.
The system continuously gathers conveyor belt performance data, including belt speed, belt tension, effective motor power for all drive motors and temperature. These parameters are then transmitted to a server at Voith, which contains a digital twin of the system. The digital twin tracks all relevant information, including belt length, belt width, the diameter of the carrying rollers, drive pulleys, return pulleys, the configuration of the transfer stations, the topography and the trough angles. Using this information, ERIC determines a normalized efficiency value, known as the Energy Performance Indicator (EnPI), based on the energy consumption for horizontal material transport. This indicator allows the operator to review the efficiency level of a particular belt conveyor. The data is further visualized on the client’s individualized user interface, in the form of an online dashboard.
The normalization of the EnPI makes it possible for the mine operator to easily compare all existing systems in terms of their energy performance. Voith also offers the option of equipping individual belt segments with RFID chips. Less-efficient belts and system sections are then easier to identify, and if necessary replace, by means of the interaction between the digital twin and the RFID. Thanks to its innovative data display system, BeltGenius ERIC provides a straightforward way to reduce energy consumption and expand service life of major components such as drives, belts and idlers, therefore reducing operating costs of mine operation.
At the same time, the digital twin compares the installed power to the energy actually being used. This allows the operator to identify power reserves. In this way, the existing capacities of the belt conveyor system can be put to optimum use without jeopardizing the safety of the system. In the event of any significant deviation in the EnPI, BeltGenius ERIC sends a direct message to the operator. Together with Voith, the operator can then take action to prevent potential damage. The system conforms to ISO 500001 and allows operators to achieve compliance with the latest global standards. Voith has provided for the immediate future by linking into a comprehensive infrastructure for the monitoring of belt conveyor systems.
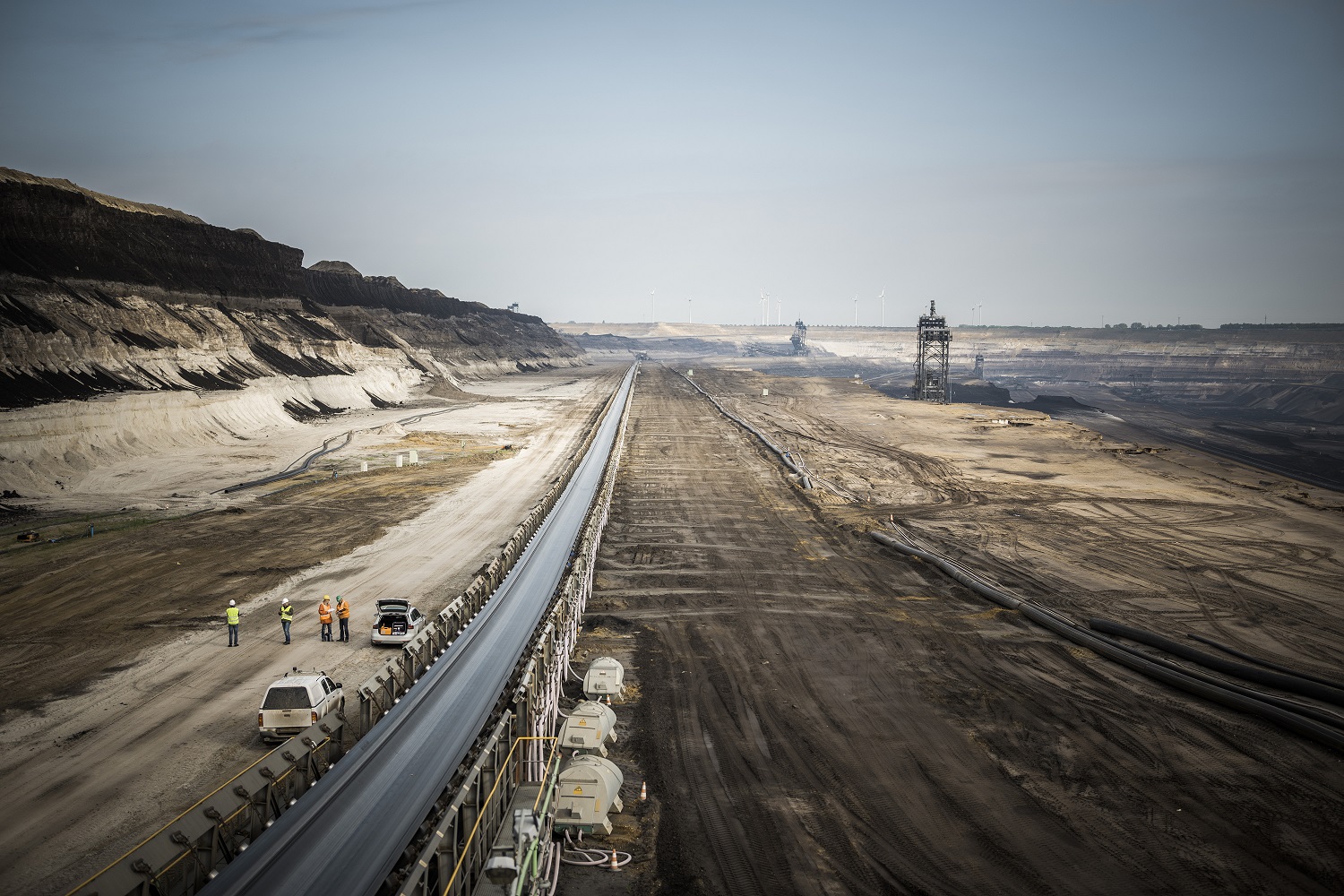
BeltGenius ERIC from Voith identifies inefficient system sections or belt segments and reduces energy and operating costs.
A webinar from the launch can also be viewed on www.Voith.com/BeltGenius.
For more information, please visit www.Voith.com/BeltGenius.
{{ commodity.name }}
{{ post.title }}
{{ post.date }}
Comments