Five ways mining has already gone green
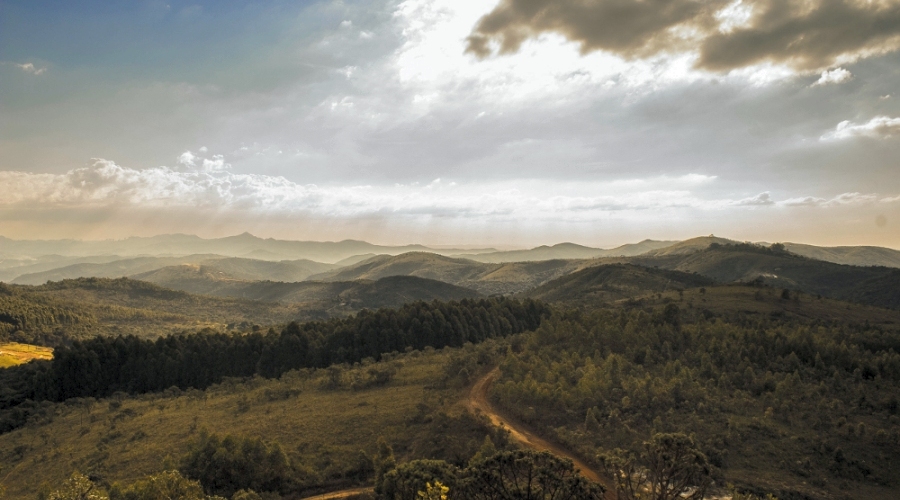
While “green” initiatives have become the latest fad across almost all industries, you might not expect that mining is already at the forefront of sustainable and environmentally friendly practices. (Main image credit: Tiago Gerken/Unsplash)
Everyone is going green. Everywhere you look, businesses and individuals alike are extolling the benefits of a green lifestyle, emphasizing sustainability, conservation, and environmentally friendly practices. This is a great movement — since the resources we extract from the Earth are finite, and since we only have one planet, it makes sense to take the best possible care of it. Going green and managing industrial projects in a responsible, efficient manner are one and the same.
For those outside the mining industry looking in, green efforts might appear not to be the standard operating protocol. It might surprise them, then, to learn that the sector has already implemented a number of innovations in green technology and practices. Let’s run through a few examples:
1. Methane Capturing Techniques
Methane capturing mining techniques, like those used by CONSOL Energy Inc., manage to keep one byproduct of coal mining activities, methane gas, under control. Not only is methane useless to core operations — it can trigger explosions in mines if left unchecked.
Rather than pushing the methane out through the mine’s ventilation system, as was once the standard operating procedure, CONSOL’s system pulls the gas from the mine with a powerful fan, according to the Wall Street Journal, then sends it through a heated ceramic that oxidizes the methane and turns it into carbon dioxide and water vapor to be released into the atmosphere.
2. Zero Discharge Water Programs
Zero discharge water programs, such as those operated by condorchem, take the wastewater produced by mining activities and make it viable for reuse, aiming to bring the ratio of wastewater disposed of to water recovered to zero. That way, not only does the process eliminate the need for costly disposal processes, but it also keeps the project’s net water usage at an extremely efficient level. Vacuum evaporation and crystallization methods are two common practices that aim to achieve that net zero discharge.
3. Energy Efficiency Efforts
Like other efforts to go green, one technique commonly used across the mining industry is streamlining energy consumption, using less and using it more efficiently. In Canada, miners are striving to make their operations more efficient in terms of energy output on a number of levels. Vehicles used in mines are increasingly powered by clean diesel fuel, and in some cases, alternative energy sources. Similarly, hybrid power sources like diesel-rechargeable batteries and hydrogen fuel cell-rechargeable batteries are “the most advanced and practical [power sources] for mining vehicles” today.
4. Reclamation
Reclamation projects at old mines really put the “green” in going green — they’re typically reseeded with natural vegetation as one of the final parts of the process, after the land is contoured and topsoil is placed in the graded area. According to the National Mining Association (NMA), U.S. mining companies have reclaimed more than 2.8 million acres of mined land, typically converting the areas into public spaces like parks, recreation areas, and even wildlife reserves.
5. Green Products and Dust Control
Notably, mine operators turn to green industrial solutions to control the dust kicked up as a byproduct of mining activities — resulting from both core operations and heavy truck traffic to and from the work site.
Dust can be a real hazard, in terms of worker safety and productiveness, operational efficiency, and relations with surrounding communities. And it’s worth noting that the products used to keep dust under control must also conform to regulatory and green working standards — which is why so many mine operators turn to Midwest Industrial Supply, Inc. for help. Midwest provides them with environmentally friendly, fully-certified dust control solutions, both above and below ground.
In the coming years, every industry will be going green — and once they have, they’ll find that with these environmentally-conscious and innovative methods, the mining industry has already beat them to it.
{{ commodity.name }}
{{ post.title }}
{{ post.date }}
Comments