Vale opens largest iron ore mine in its history

Vale SA (NYSE:VALE) cut the ribbon on a massive iron ore mine in Brazil on Saturday – the largest in its history and what the world’s largest iron ore producer says is the biggest ever in the mining industry.
While that is quite a claim, delving into the details of the $14.3-billion S11D complex shows that Vale is most likely correct.
“For me, seeing the completion of S11D is much more than just witnessing a new landmark in the mining industry. More than an enterprise embodying the latest technology, low cost and high productivity, the S11D portrays Vale’s ability to make things happen”: Vale’s CEO, Murilo Ferreira
Located in Canaã dos Carajás in Southeast Pará, the project – which includes the mine, processing plant, railroad and port logistics – has been 15 years in the making, starting with the first technical and feasibility studies in 2001. The Preliminary License (LP) was granted in June 2012 and, a year later, the Installation License (LI) was issued. On December 9, the Operation License (LO) was granted. Commercial operations start in January 2017 and the mine’s lifespan is expected to be 30 years.
S11D is also the largest private investment made in Brazil in a decade, which Vale says will boost the economies of the states of Pará and Maranhão. The company says its operations in Minas Gerais will also benefit from the project, since that ore will be blended with that extracted from S11D.
“For me, seeing the completion of S11D is much more than just witnessing a new landmark in the mining industry. More than an enterprise embodying the latest technology, low cost and high productivity, the S11D portrays Vale’s ability to make things happen,” Vale’s CEO, Murilo Ferreira, said in a press release describing the project in detail.
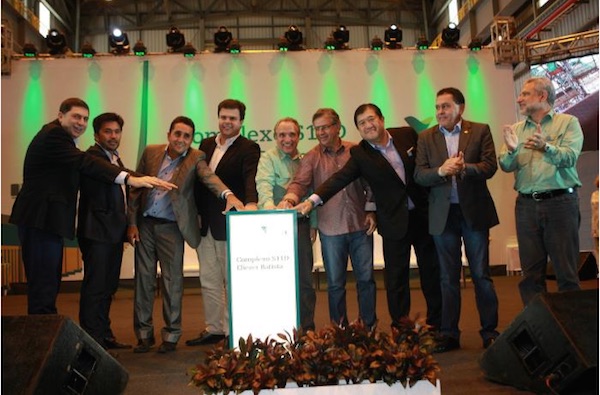
Vale executives inaugurate the $14.3-billion project on Saturday. Photo courtesy of Vale.
The completion of the mine is as much a feat of mining engineering/ construction as of transportation logistics.
Out of the US$14.3 billion invested in the project, $6.4 billion accounted for the mine and plant, and $ 7.9 billion in the construction of a 101-km-long railroad branch, and to expansions of the Carajás Railroad (EFC) and of the Ponta da Madeira Maritime Terminal in São Luís (MA).
S11D forms part of Vale’s massive Carajás complex and will add another 90 million tonnes to the miner’s capacity pushing it to between 400 and 450 million tonnes per year, by 2020.
The project was named after its location: it is on block D of the S11 ore body, which contains four blocks: A, B, C and D. According to Vale, S11’s mineral potential is 10 billion tons of iron ore, and blocks C and D together have reserves of 4.24 billion metric tons. The first geological surveys in the region occurred in the 1970’s.
Its full name is the Eliezer Batista S11D Complex, named after the company’s former president who was in charge of building the Tubarão Complex and assessing the feasibility of the Carajás mine.
Vale said in November it has been able to reduce cash costs to just $12.70 per tonne (it’s in the high teens at Rio Tinto and BHP) and that S11D could push costs below $10 a tonne, thanks largely to the weak real which is down more than a third in value against the US dollar over the past year. The press release confirms that Vale expects to deliver ore at the Ponta da Madeira Maritime Terminal in São Luís (MA), the so-called C1 cash cost, at US$7.70 per tonne – 41% less than Vale’s current average C1 cost.
One of the most interesting aspects of the project is its automation. The mine will use a truckless system for conveying the ore – with a set of structures comprised of mobile excavators and crushers interconnected by a conveyor belt. Shovels will dump the ore in mobile crushers, which feed a system of mobile and fixed conveyors installed inside the mine, and long distance conveyors connecting the mine to the plant and waste piles. The total length of the truckless conveyor belts operating in the mine and the plant is 68 km. Vale says the truckless system will cut fuel costs by 70% as well as slash waste and greenhouse gas emissions.
The ore will be dry processed with equipment developed by Vale in partnership with manufacturers, specially tailored to process the high-moisture ore from Carajás, the company states. Dry processing – using iron ore’s own natural moisture – is expected to cut water consumption by 93% and will eliminate the need for tailings dams.
Read more about the project here, including a video of a drone flyover
{{ commodity.name }}
{{ post.title }}
{{ post.date }}
Comments
Anita sari
obat kutil kelamin: http://obatkutilkemaluan.website