Why LFP cathode material is making a comeback
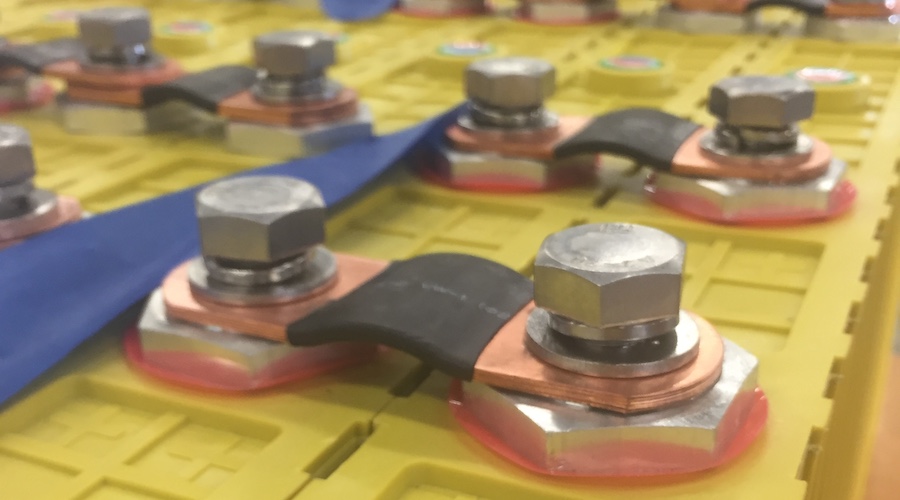
A previously side-lined EV battery cathode material – LFP, composed of lithium iron and phosphate – has come to the forefront in 2020, thanks to its safety, low cost, and the simplified battery pack design that it allows, a white paper published by Roskill reveals.
According to the market analyst, the set of reasons may be the driving forces behind Tesla’s, BYD’s and Volkswagen’s decision to choose LFP cathodes to power their electric vehicles in the Chinese market.
When it comes to safety, for example, Roskill points to the fact that the Chinese Ministry of Industry and Information Technology issued new regulations this year which will require EVs to inhibit any fire or explosion within five minutes after a thermal runaway incident happens in battery cells.
To avoid costly mitigation systems needed in the new regulatory context in China, carmakers seem to be resorting to inherently safe LFP cathode materials
“To achieve that level of protection, Chinese EVs using nickel-based chemistries such as NCM will require mitigation systems; these may include the use of fire-proof mica plates between pack and vehicle, ‘aerogel’ segments distributed throughout the pack, or robust but heavy steel beams, among many other solutions,” the paper’s summary reads.
“Such protection systems come at a monetary cost but, more importantly, an energy density cost (given their weight and volume), undoing advances in cell performance that were designed to lower pack cost and, therefore, EV prices.”
After describing the issue, Roskill points to the fact that to avoid costly mitigation systems, carmakers can resort to using inherently safe LFP cathode materials, which would allow them to build simplified battery packs without modules, and without the otherwise necessary but voluminous safety and auxiliary components.
“In the last 12 months, companies such as BYD, CATL and Honeycomb (SVOLT) have revealed several pack architectures using this approach,” the analyst’s document states. “As a result, some of these companies claimed up to 30% higher volumetric energy density, while decreasing the cost by as much as 30%, thanks to a more streamlined pack design.”
Besides safety features, cobalt prices may be pushing the LFP comeback.
“Cobalt price rises in 2018 made the cathode cost on a 50kWh battery pack move up 13-28% y-on-y. Although the cost impact at total vehicle level was much smaller, at 4-7%, this change could wipe out the margin obtained in smaller mass-market cars,” the whitepaper reads. “In comparison, the cost of LFP moved just 1% y-on-y in the same period, with a marginal effect on total car cost.”
To the prices of the blue element, Roskill adds the fact that labour and human rights conditions linked to its mining in the Democratic Republic of the Congo, which is responsible for over 50% of the cobalt produced worldwide, remain murky.
“These environmental, social, and governance (ESG) concerns, coupled with the fact that around 25% of global cobalt reserves could be depleted by 2030 (even when considering ultra-high nickel chemistries and cobalt recycling), pose a significant risk to supply chain disruptions,” the report reads.
Whether LFP will overtake nickel-based cathodes, in Roskill’s view, is yet to be seen. The reasoning behind this is that 95% of LFP cathode manufacturing is produced in China and that patent restrictions that confine its production to the Asian country will be lifted only in 2022.
More News
{{ commodity.name }}
{{ post.title }}
{{ post.date }}
Comments