Sweden could take global lead in green steel production – report
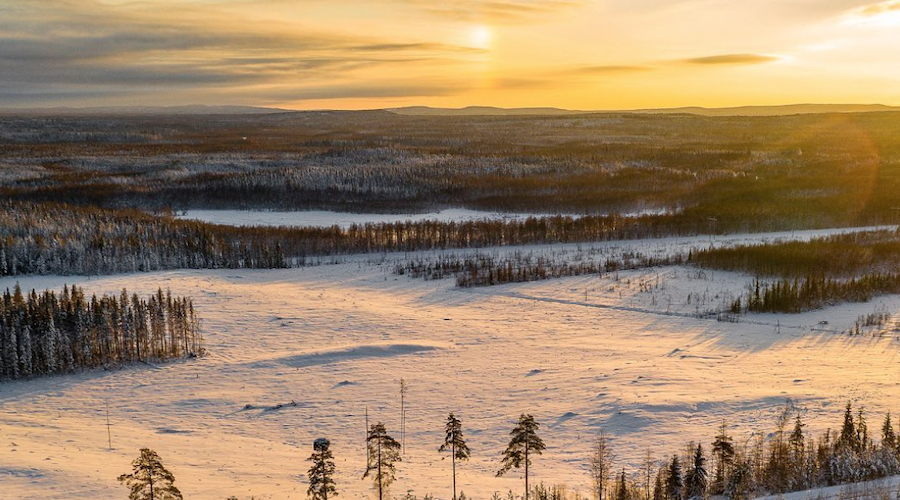
A new report by Wood Mackenzie states that Sweden could become a pioneer in green steel production as at least two initiatives by HYBRIT and H2 Green Steel, separately, have been launched with a target to manufacture 10 million tonnes (mt) of fossil fuel-free crude steel annually by 2030.
HYBRIT is a joint venture between Swedish steelmaker SSAB, iron-ore miner LKAB and utility Vattenfall, while H2 Green Steel is a company backed by Vargas Holding – the same investment firm that co-founded Northvolt.
According to the market researcher, the nordic country could take the lead when it comes to the environmentally friendlier version of the alloy, despite the fact that its current production is not particularly large. Sweden’s steel industry manufactured 4.4mt of crude steel (3.4mt of finished steel) in 2020, representing 3.2% of crude steel production (2.5% of total finished steel production) across EU-27 and the UK.
“Sweden’s decarbonization drive in the steel industry signals substantial cost reduction potential for green steel over the coming decades, due primarily to the declining cost of renewables and green hydrogen and increasing carbon prices,” Wood Mackenzie’s principal analyst, Sohaib Malik, wrote in the report.
“The country boasts Europe’s largest iron ore reserves and excellent renewable energy resources – two primary prerequisites for the production of green hydrogen and decarbonized crude steel.”
According to Malik, at a levelled cost of electricity at $30 per megawatt-hour, wind power is a highly economical source of power generation in Sweden today. Meanwhile, further cost reductions are expected with better financing structures for onshore wind, lower capex for onshore and offshore installations, technological optimization for asset management and state support for offshore grid infrastructure.
The analyst also said that alkaline electrolysis technology is most likely to play a key role in green hydrogen production which he emphasized is crucial for Sweden’s green steel production.
The WoodMac expert also pointed out that compared to proton exchange membrane electrolysis, alkaline electrolysis has a lower capex of $925 per kilowatt today and it is expected to halve by 2030, enabling a levelled cost of $1 per kilogram of green hydrogen using onshore wind power.
For Malik and report co-author Mingming Zhang, alkaline electrolysis and renewable energy from onshore wind will produce the most cost-effective green crude steel in Sweden.
“Assuming a carbon price of $100/t, green steel producers could benefit from $85/t of carbon credits. Better financing models for onshore wind and 48% lower capex for alkaline technology in 2025 yield steel cost of $360-390/t in carbon price scenarios ranging between $50/t and $150/t,” they estimated in the report.
In Zhang’s view, producing green steel with cost parity to conventional steel in the 2020s is quite possible if natural gas-based direct reduction iron and electric arc furnace steelmaking processes are used as a baseline.
“Global steel demand will reach 1,872mt a year by 2030, 6.4% higher than in 2020. The case for green steel will grow stronger as its cost reduces. In addition, the success of green hydrogen to produce green steel at a commercial scale will justify the enthusiasm around its ability to accelerate decarbonization,” the analysts concluded.
More News
Lithium Americas reaches final investment decision for Thacker Pass mine
Once open, Thacker Pass is expected to produce 40,000 metric tons of battery-quality lithium carbonate per year.
April 01, 2025 | 03:05 pm
Gold retreats from record as traders brace for Trump’s tariffs
Traders are on edge as Trump plans to announce sweeping levies on all of America’s trading partners on Wednesday, raising the risks of retaliatory measures.
April 01, 2025 | 12:58 pm
{{ commodity.name }}
{{ post.title }}
{{ post.excerpt }}
{{ post.date }}
Comments