Translating East to West as South Korean companies take battery business models abroad
Global battery material producers are aware of current and emerging localization policies that reward in-country manufacturing. What are the challenges of vertically integrating supply chains abroad as Asian powerhouses conjure up Western entry strategies?
According to demand forecasts by the Advanced Propulsion Centre UK, the global compound annual growth rate for batteries is sitting at 28 percent from now until 2030, higher in both Europe and North America.
“That’s another 12 million units per year by 2025 and 34 million units per year by 2030,” says Dave OudeNijeweme, Senior Director for Batteries at Worley. “It is widely appreciated that more than 60 percent of the battery value is added upstream of battery manufacturing, in the complex and protracted value chain from mine to active material.”
Electric vehicle (EV) producing countries appreciate this and, in the context of increasingly favorable policy settings, are looking for greater security of supply and value-add with localized manufacturing of battery materials.
These dynamics have prompted the world’s leading battery materials producers to enter new and unfamiliar regions. What will it take for them to establish successful supply chains in every corner of the world?
Policy shifts are now a major driving force on the electric vehicle industry
Policies in many countries are still driving the uptake of EVs. Additional initiatives are now being put in place by governments to ensure that more value is added locally leading to increased economic benefit in those territories.
For example, since the Trade and Cooperation Agreement (Brexit deal) came into effect on 31 January 2020, EU- and UK-based carmakers are required to increase the minimum local content from 40 percent in 2021 to 55 percent by 2027 to avoid tariffs. Further rules of origin apply to batteries and their materials, with cathode active material – the highest value component in the battery – specifically mentioned.
And in the US, the Biden administration via its Inflation Reduction Act (IRA) has ‘started to put money where its mouth is’ in terms of policy initiatives, which provides tax incentives for companies that manufacture battery materials locally. Significant end-user tax credits of up to $7,500 are available for vehicles with locally sourced battery components.
This was recently followed by a specific funding round under the Bipartisan Infrastructure Law of 21 projects for new, retrofitted, and expanded commercial-scale domestic facilities to produce battery materials, processing, and battery recycling and manufacturing.
“As predicted, we now see increasing proportions of the battery and its components to be made in the US with critical materials sourced from the local region or countries it has Free Trade Agreements with,” says OudeNijeweme.
Initiatives of this kind have triggered a huge effort into rethinking the supply chains for EVs, the materials that go into them, and where they will be produced.
South Korean powerhouses conjure up entry strategies
South Korea is home to some of the world’s largest battery and battery material producers, including LG Chem, SK On, Samsung SDI, Posco Chemicals and EcoPro BM. These are in turn supported by long standing research and development programs and a buoyant supply chain. It’s why many South Korean battery companies already have significant supply deals with large OEMs, many of which are located across Europe and North America.
With localization policies such as the one triggered by the Brexit and IRA deals on the horizon, South Korean manufacturers, along with their supply partners, recently announced significant expansion plans for production abroad.
Coming to America
OudeNijeweme is seeing a significant capacity expansion of South Korean companies across the battery value chain.
“This is a global trend across battery manufacturing, active materials and mining,” he says. “Most notably, it’s happening in end-markets such as Europe and North America, but also Indonesia.
The United States seems a most attractive market for South Korean battery makers, due to the country’s large domestic auto market and the presence of major vehicle manufacturers.
“Just recently, we’ve seen joint ventures between Ford & SK and GM & LG to build capacity of 129GWh/yr and 120GWh/yr by 2025 respectively,” says OudeNijeweme. “These are huge numbers if you consider that all the batteries for the Nissan Leaf produced in the US came from a 2GWh/yr factory.
“249GWh of batteries needs approximately 250kt (kilotons) of active anode materials and 350kt of active cathode materials. These capacities don’t currently exist outside of Asia, and with the Inflation Reduction Act on top of sound commercial reasons and supply chain logistics, we are expecting a significant localization effort for this material.”
Don’t get ‘lost in translation’
According to OudeNijeweme, translating an Asian business model to operate effectively within the construction, environmental, social and governance (ESG) practices of the Western world can be overwhelming and time-consuming to navigate.
“To reduce time to market, it’s vital to have a strong and knowledgeable delivery partner that knows how to execute projects in its own backyard,” he says.
“It’s not sufficient to simply be experienced in converting battery material facility designs into local standards and codes – there is a much broader range of expertise required to ensure smooth execution: understanding capacity of the local labor market and work practices, integration with the materials supply and construction ecosystem, awareness of how to manage community impacts and permitting to name a few. All of these issues can risk project delays and cost overruns when not managed effectively.”
Need for speed
The speed and scale at which this energy transition is happening, especially the electrification of transportation, is something that makes this extraordinarily exciting. But it’s also extremely challenging.
“Speed to market is everything, and this makes the supply chain creak,” says OudeNijeweme. “It is also fair to say that much of the battery technology is still maturing, while much of the process technology is in its relevant infancy.
“There is a complex equilibrium to be achieved between accelerating delivery, providing confidence in project outcomes whilst maintaining flexibility to adapt to changes in the environment. Very few firms have mastered this trifecta to bring operating assets online at the pace and scale required. It requires a departure from traditional sequential development processes seen in more mature industries and requires a heightened level of collaboration with owners, contractors and the equipment vendors.”
But nothing is doable without adequate feedstock. And material scarcity is a growing concern.
Show me the minerals
The minerals supply gap is widening, and the sheer scale required for the electronic mobility revolution – to reduce our global dependence on fossil fuels – is now affecting the value chain’s ability to operate effectively.
South Korean companies already have secured access to raw materials in key producing countries of lithium, nickel and cobalt: namely South America and Australia. But to meet demand they’ll need more, and someone to help liberate them from the ground while building up the required refining and recycling capacity.
“For all companies involved across the battery value chain, setting up sustainable practices to deliver battery materials with a low-carbon footprint will need to be considered at every step,” says OudeNijeweme.
If these challenges are not addressed, the industry risks moving the commercial viability of batteries in the wrong direction as prices surge and supply timing slips.
Partnering for success
Expansion into fast growing markets in Europe and North America provides significant growth opportunity for Asian-based battery materials producers. But it also comes with a set of unique challenges.
“Doing this without an experienced local partner isn’t impossible, but it’s not how I would go about it,” suggests OudeNijeweme. “Business success in this market is predicated on supply chain security and speed to market. It is a race to increase localized production capacity and the winners will be those who have successfully navigated the complexity of asset development and guaranteed their feedstock material.
“For battery materials producers, forming partnerships, joint ventures and collaborations across the entire supply chain will be key to overcoming the challenges – and seizing the opportunities – of expanding their operations all over the world,” ends OudeNijeweme.
Worley is a tier 1 asset and project delivery services organization and a leader in the development of battery materials production facilities. Its heritage is in the energy chemicals and resources sectors, with a project delivery track record all over the world. For more information, visit https://www.worley.com/what-we-do/our-markets/mining-minerals-and-metals/new-energy-materials
Download Free Whitepaper
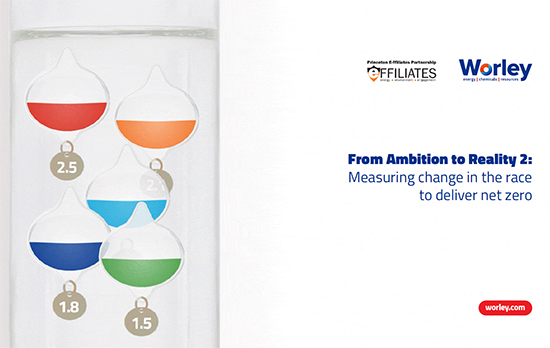
From Ambition to Reality
Measuring change in the race to deliver net zero.
If we want to get to net zero and limit warming to 1.5ºC, we must dramatically rethink the way we deliver infrastructure.
We can’t turn up to 2030 and expect the world to have fundamentally changed. We don’t want to get there and find ourselves saying, “If only we knew.”
To avoid this, we need to monitor, report and adjust our behaviours and practices along the way. So what does that look like?
From Ambition to Reality 2 is the next installment of Worley and Princeton University’s Andlinger Center for Energy and the Environment’s ground-breaking series. The first paper showed that achieving net zero is technically feasible, but there’s an immense infrastructure delivery challenge to get there.
Recalling the findings, this next paper focuses on how to convert thinking into action by outlining the indicators we’ll use to measure and drive change in this critical decade. It’ll help you understand the gaps we need to close over the next eight years to get us to a net-zero future.
Comments