The Latest Technologies for Managing Risks in Mines
How remote and real-time IoT monitoring can be applied to open pit and underground mines
Recent tailings dam disasters like the one at Córrego do Feijão mining complex in Brazil, highlight the need for sustainable risk management and monitoring programs for the mining industry. According to the 2018 Responsible Mining Index report by Amsterdam-based Responsible Mining Foundation, many leading mining companies struggle to prove that they are addressing risks efficiently to prevent tailings dam failure. Once a monitoring solution has been put into place, most operators fail to continuously review the effectiveness of their applied method of choice. The challenge of having to comply with environmental and legal requirements while constantly having to raise productivity levels in an ever-changing, harsh environment, makes it difficult for mines to stay in control.
Common risk management approaches: manual readings and cables
For a long time, ensuring safety in tailings dams entailed monitoring risk indicators such as pore-pressure through manual readings and collecting data from vibrating wire sensors such as piezometers. This traditional method requires deploying workers which not only poses health and safety risks but also incurs significant logistics costs. Due to the often hard-to-access environments, some mines even have to use a helicopter and satellite technology to collect data over large areas. Given the costs and risks, data collection becomes infrequent and the information collected may be irrelevant or outdated quickly. This is why most mines currently use cabled solutions to automate data collection from multiple sensors within a tailings dam or around the slope.
Besides tailings dams, slope stability is another major risk that needs to be managed by mines. Cables along the slope allow gathering information from a multitude of sensors at the same time and storing the information in one read-out unit which makes the monitoring process more efficient. The downside is that cables are static and difficult to adapt to the environment of a mine, which is like a never-ending construction project. When there are roads included in a slope, cables have to be laid underground to accommodate the mobility needs of the workers and this may have a significant impact on the operations, costs and the environment. While cable monitoring addresses the issues of manpower safety regarding both tailings dams and slopes, it is costly in terms of installation and maintenance. Installing cables around a tailings dam, slope and across the whole worksite with equipment scattered everywhere can make cables highly vulnerable to damage that will be difficult to detect and may compromise the data.
Wireless monitoring: the current misconception
The past few years, mines have started leveraging technological advances to update their risk management programs. According to a report by Accenture on digital mining, over 200 C-level decision makers in the mining and metal industry surveyed ranked real-time data visualization as the second most important digital investment, only topped by cybersecurity and followed by real-time analytics. In 2017, 31% stated that real-time data visualization has already been widely adopted within their organization.
To gather real-time data from a mine, existing geotechnical sensors are connected to wireless data loggers which transmit information remotely and at sample rates close to real time, if needed. While most mines are eager to try out this new approach and successfully update their programs, as the Accenture reports confirms, others test wireless methods and are left disappointed. As with most novelties, the devil is in the detail: while wireless monitoring makes mining operators less dependent on manual readings or cable installations, not all technologies available are the same, especially when it comes to network connectivity and adaptability.
Devil in the detail: short vs. long range
What makes wireless monitoring attractive for operators is the massive area of land mines generally span over. A good example would be the Bingham Canyon mine owned by Rio Tinto. One of the largest open pit mines in the world, it covers a total area of more than 900 hectares, is 1.2km deep and over 4km wide. To make data available in real time, the information needs to be remotely captured and transmitted over very long distances to servers located at a remote operating center. The challenge is to choose a wireless monitoring system that can handle the scope of a mining operation. Most wireless technologies depend on local area networks (LAN) such as Zigbee, Bluetooth or Wifi which are used for short distances between 50 and 100 meters and are not sufficient for mines. While cellular technologies such as 3G and 4G may reach longer distances and allow for frequent data collection, mobile devices feature high power consumption rates. Both LAN and cellular technologies dependent on network signal and line of sight (LOS), which can be difficult to achieve in mines. For mines, the key to successfully implementing wireless monitoring is to work with devices running on IoT connectivity such as LoRa. With this low-power, wide-area network (LPWAN) technology, data can be transmitted over distances of up to 15 kilometers / 9 miles while only needing very little power. Batteries can last up to 10 years as devices only ‘wake up’ when they have to read and transmit data and go back into sleeping mode after.
Network adaptability: static vs. dynamic
Mining engineers should not only focus on range and battery when evaluating potential monitoring solutions, but want to make sure the network they install has the ability to automatically adapt to changes in the sensor network setup. Let’s picture a tailings dam where data nodes are used to monitor more than 90 piezometers. Each piezometer is connected to a wireless data logger enabling the mine to collect information on the health of the piezometer and pore pressure within the tailings dam in real time. Every time a new device is included or removed from the network, the sensor network needs to be capable of updating itself and shouldn’t require to manual reprogramming by an expert to prevent wrong readings and potential disasters due to human errors. If five sensors are removed from the network without it dynamically reconfiguring, the data loggers keep recording data based on the previous network configuration which will result in e.g. data from sensor 20 being recorded as if it was from sensor 15. This will not only cause delays when processing the data, but will also cause confusion when interpreting the information; a major threat to any risk management initiative.
Going deeper: wireless monitoring for underground environments
Real-time data gathering is applicable to both above-ground and underground monitoring situations. For example, Boliden uses wireless technology to control pore-pressure by means of 120 piezometers installed in 40 boreholes in their Aitik open pit mine situated outside the town of Gällivare in the very north of Sweden, and also uses sensors connected to robotic equipment at its underground Garpenberg mine; the sensors feed data in a central above-ground control room.
Shafts are drilled at underground mines to provide access for vehicles and workers to the ore. There is no network available underground, so shafts are used to install optic fiber, leaky feeders and access points via wifi. While Wifi features high battery consumption and limited distance coverage, IoT wireless technologies such as LoRa provide an alternative last mile option from the gateway to the actual sensors that may be installed in galleries spanning from 100 meters to 2 kilometers. Since galleries range from 2.5-6 meters in height, which is just enough to let scoop trams and trucks pass through, there is minimal space available for cabling; making easy-to-install and to adapt monitoring solutions an attractive alternative.
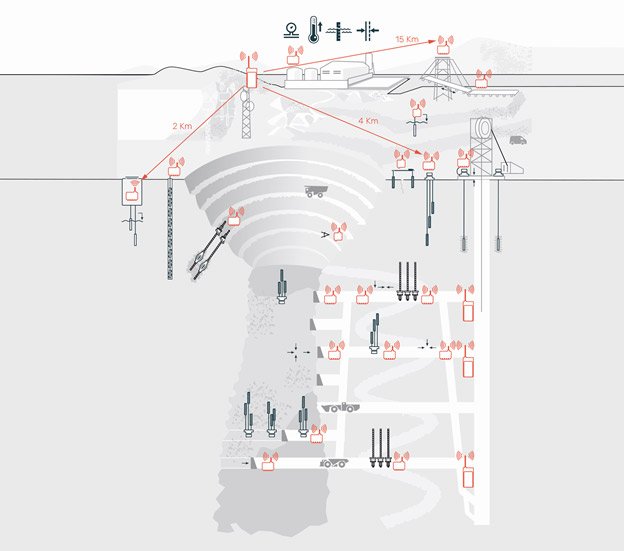
Graphic: How IoT wireless monitoring can be applied in mines
Estimated savings due to IoT wireless monitoring
Embracing digital advances like IoT wireless monitoring to increase safety and boost productivity makes even more sense, if mining operators can calculate the expected ROI of deploying a new technology in advance. Based on a recent cost comparison exercise for 2 mines in South Africa performed by IoT company Worldsensing, the results show that for long-term projects such as mining operations which can last for around 15 years, wireless monitoring can generate savings ranging from 20% (5 years) to 70% (20 years) considering the following variables:
- Project duration: from 3 to 20 years,
- Manpower: number of people deployed, estimated daily rate of field geotechnical engineers including insurance,
- Vehicle deployment: includes daily cost of fuel and maintenance,
- Number of mining sensors deployed,
- Cable: estimated length per sensor and cost per meter,
- Number and cost of wireless monitoring equipment deployed: Loadsensing, wireless monitoring system,
- Number of days allocated for monitoring and maintenance per month or year.
Note: The numbers presented are based on estimates and are only indicative of the potential savings. The figures may change depending on the variables.
Fellow mining experts from Geomotion and RamJack share insights
Worldsensing offers a more in-depth webinar about risk management through IoT wireless monitoring for open pit mines as well as underground mines in collaboration with mining experts from Geomotion and RamJack presenting relevant use cases. The panel comprised of mining and wireless monitoring industry experts from Spain, Canada, South Africa and Australia also answer questions from fellow mining professionals through a dedicated Q&A session.
About Fernando Perez Gutierrez
Fernando is a mining engineer who started working with wireless monitoring technology at Ramjack Technology Solutions before moving to IoT pioneer Worldsensing where he is in charge of supporting partners in LATAM and Africa by providing them with the globally leading wireless monitoring system, Loadsensing. Fernando earned his degree in mining, energy and materials and has a Masters degree in Mining Technologies from the University of Oviedo as well as a Masters degree in Project Management from the University of Barcelona and OBS.
About Loadsensing
Loadsensing is the leading wireless monitoring system allowing mines to connect and wirelessly monitor tailings dams, deep excavations and other mining components in remote locations. Loadsensing data nodes are used to digitize and power most geotechnical instrumentation and monitoring sensors. The data acquisition system is rapidly becoming the new standard for wireless geotechnical monitoring as it’s currently used in over 50 mines and has a network of over 30.000 sensors worldwide. The wireless monitoring system is part of the Worldsensing product portfolio, a widely recognized global IoT pioneer and operational intelligence provider.