AspenTech Reduces Downtime for Mining Equipment
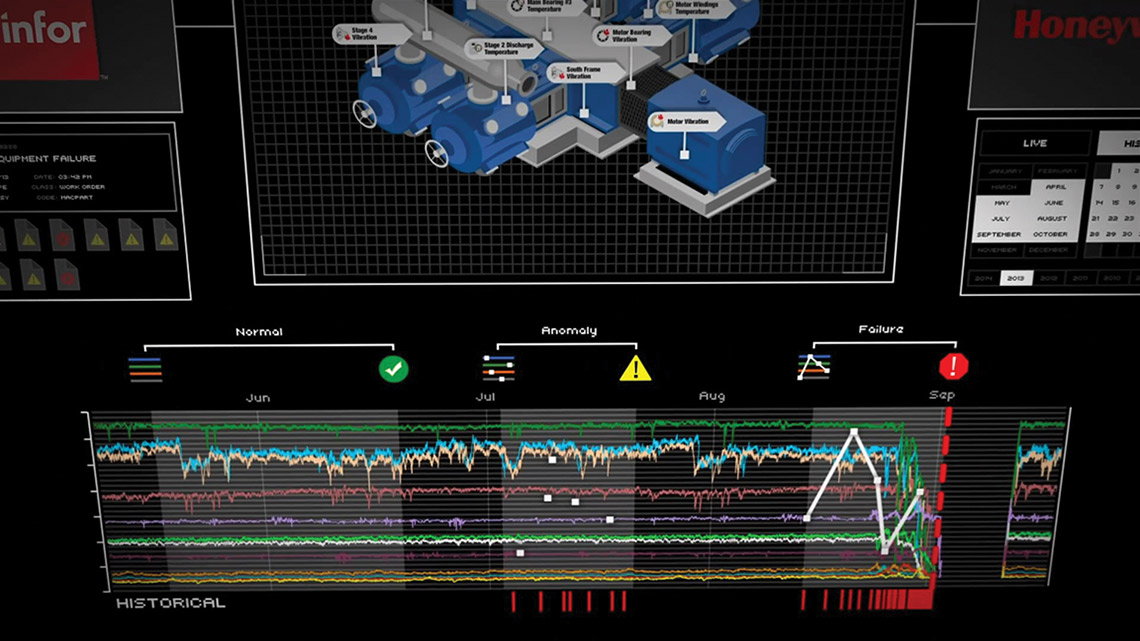
Screen image of AspenTech’s Aspen Mtell software in action. Credit: Aspen Technology.
AspenTech Reduces Downtime for Mining Equipment
In 1981, the chemical engineering group at Cambridge, Mass.-based MIT received a U.S. Department of Energy grant to study technical innovation in the processing industries as part of a strategy to mitigate the impact of another oil crisis like the one that threatened the U.S. in the 1970s.
Thirty-eight years later, Aspen Technology (NASDAQ: AZPN) has a market cap approaching US$7 billion—greater than all but a handful of mining companies in North America—by becoming a software company that makes processing companies more efficient.
Most of its work to date has been in the chemicals and petrochemicals spaces but now AspenTech is seeking to gain a bigger pied-a-terre in the mining space.
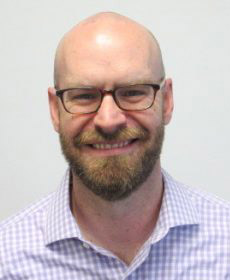
Michael Saucier
“We’re a household name in the chemicals and petrochemicals industries but in mining, not so much,” says Michael Saucier, senior manager of product marketing. “We are, however, getting some notches on our belt.”
Saucier points to a multinational mining company based in Vancouver that has implemented AspenTech’s proprietary Aspen Mtell software into its metals refining processes.
Aspen Mtell’s autonomous agents predict impending failures, determine lead-times and provide prescriptive guidance to mitigate or even prevent breakdowns
“We can tell you, for example, that a bearing on a slurry pump is going to go in 36 days. That gives the company time to still use that pump and schedule the proper maintenance and get the right part out there – because God knows these operations are pretty remote – and that way you’re not losing any time and running the system to failure. That’s the piece we’re focused on.”
Saucier says Aspen Mtell will seek out similar warning signs on any static or dynamic assets such as heat exchangers and pumps as well as crushers or tailings monitoring systems.
But how does it do it?
Aspen Mtell uses what AspenTech calls “low-touch machine learning,” which cleverly deploys autonomous software “agents” that watch live equipment feeds to look for normal and abnormal behavior patterns that ultimately identify the “signatures” of failures.
These agents are created by an Aspen Mtell proprietary software “wizard” that analyzes years of data and weaves it into a simple chart known as a probability waveform.
There are four patterns that emerge in the waveform: offline, failure, hidden failure and normal.
Once all offline data is removed, the wizard seeks out failure signatures defined as “multi-variant and temporal changes in behavior patterns” leading up to a recorded event. An agent is created for each failure event. The agent will send out an alert when a failure is detected.
Spikes or changes in behavior that do not lead to an event are defined as hidden failures and the wizard creates more agents for each instance.
The Mtell wizard then removes all the failure and hidden failure patterns from the waveform. All that’s left is considered normal. Then an anomaly detector agent is sent out to monitor any variations in normal behavior.
If an anomaly is detected but doesn’t match any previous failure patterns, it will trigger an alert that requires an inspection to determine the cause. The event is either categorized as a new variation of normal or a new failure event.
If it’s considered normal, the baseline is then added to the anomaly detector agent so it won’t set off an alarm if that behavior pattern happens again.
If the anomaly is deemed to be a failure event, a new failure agent is created that allows the software to detect the problem sooner, essentially learning as it goes.
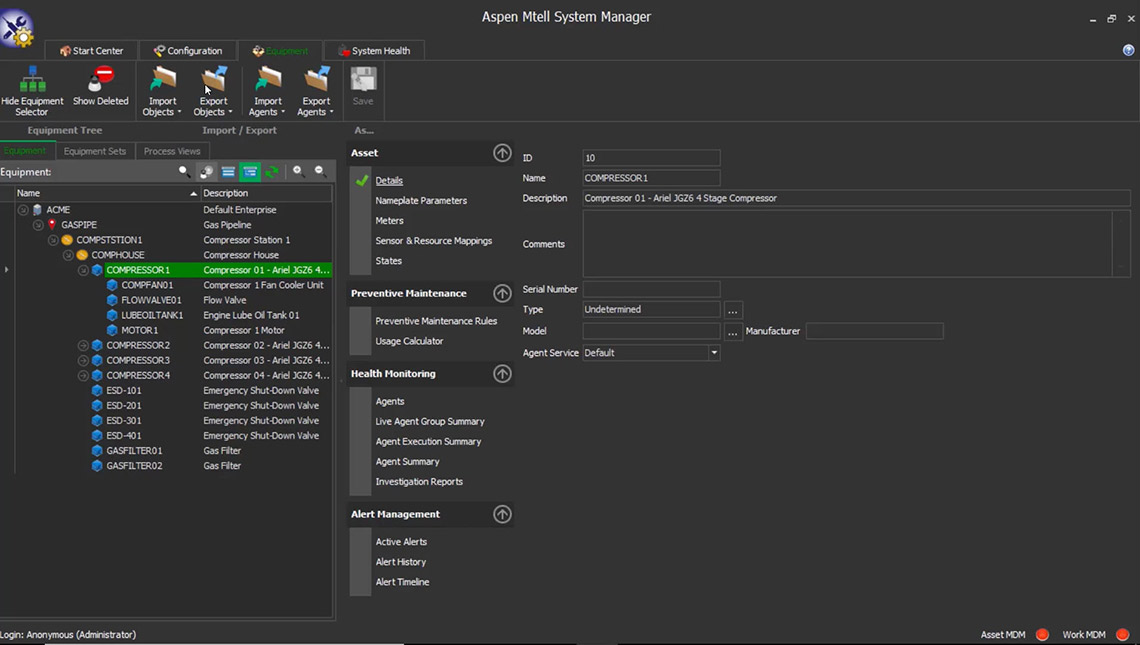
The Mtell tool’s user interface. Credit: Aspen Technology.
All of these Aspen Mtell agents can be fine-tuned to provide a company with whatever it wants in terms of prescriptive maintenance. For example, Saucier cites a Fortune 500 energy company that operates two liquefied natural gas terminals.
In the past, the company’s internal management system had produced scheduled maintenance work orders based on calendar triggers, whether the maintenance was required or not.
Once Aspen Mtell was implemented, Saucier says, it reduced the work by as much as 60% when compared with scheduled maintenance based on equipment runtime hours.
Another tool the company offers is Aspen Fidelis Reliability™.
Through simulation, the software predicts the future performance of a plant and the variations in that performance given the current design, operations, logistics, maintenance and market dynamics.
Aspen Fidelis models can be custom designed to fit almost any situation and help managers make better decisions about where to deploy capital.
For example, an engineer in any department can quickly build a specific model to tackle a problem. Once a solution is found, managers can determine how to proceed.
Aspen Fidelis, formerly known as Fidelis Titan 2, was acquired by AspenTech in 2016 to increase their focus on asset optimization, by enabling customers to optimize the design, operation and maintenance of their assets throughout the asset lifecycle.
Saucier has some advice for mining company executives seeking software that will lower costs and boost uptime.
“If I were a purchaser of software, I would be completely overwhelmed because everyone is saying the same things. It’s all predictive analytics; it’s all prescriptive analytics. And people use nuanced terms like ‘machine learning,’” Saucier explains.
“Make sure you do your research,” he says. “Make sure you find a software provider that can work with all of your equipment, not just one piece or even three pieces. And make sure they have a staff and a true machine learning solution that can work with you long after the pilot phase.”
— The preceding Joint-Venture Article is PROMOTED CONTENT sponsored by Aspen Technology, Inc., and compiled in cooperation with The Northern Miner. Visit www.aspentech.com for more information.