The secret to safer oil & gas pipelines: graphene

Incorporating graphene into a polymer liner used in pipes that transport crude oil and gas from the sea floor makes them stronger, researchers say.
According to a team of scientists from the University of Manchester and The Welding Institute, laminating a thin layer of graphene nanoplatelets to polyamide 11 (PA11) – a plastic often used in the aforementioned liners – helps produce structures that behave as exceptionally good barriers, avoid the escape of gasses and, therefore, stop corrosion.
In a study published in Advanced Materials Interfaces, the experts explain that pipes are generally made of internal layers of polymer or composite and external strengthening steel. Within these pipes, fluids may be at very high pressure and elevated temperature.
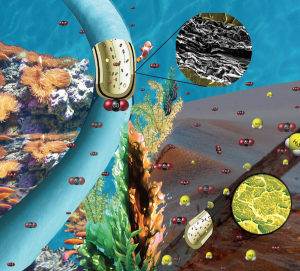
Image by the University of Manchester.
Occasionally, carbon dioxide, hydrogen sulfide and water permeate through the protective barrier layer of the pipe and this makes the steel corrode causing the pipe to lose strength over time. Such weakness could cause a catastrophic failure.
However, the researchers tested their multi-layered laminate structures at 60oC and at pressures up to 400 times atmospheric pressure and noticed that CO2 permeation was reduced by over 90 per cent compared to PA11 alone, while permeation of hydrogen sulfide can be reduced to undetectable levels.
In a media statement, the researchers said that corrosion costs the oil and gas industry in the US alone $1.4 billion every year but, in their view, this graphene technology has the potential to significantly extend the life of the underwater pipework and therefore reduce the time between repairs.
Beyond the oil & gas sector, the scientists say graphene membranes like the ones they used, have the potential to revolutionise industrial processes, such as food packaging, water filtration and gas separation.
{{ commodity.name }}
{{ post.title }}
{{ post.date }}
Comments