Scientists ‘stretch’ li-ion batteries storage capacity, lifespan
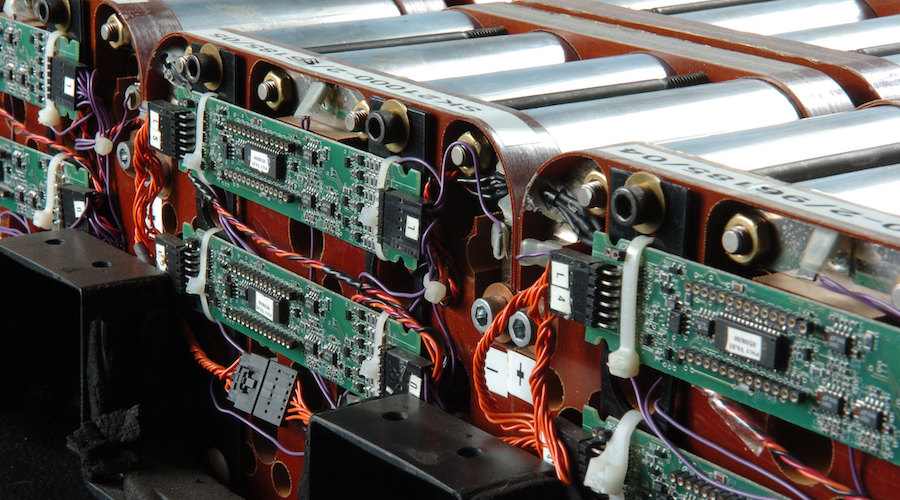
Researchers at the University of Southern California are working on a development aimed at discouraging the degradation of lithium-ion batteries’ structural integrity, which is one of the reasons that lead to a functionality drop over time.
Their solution involves introducing “stretch” into battery materials so they can be cycled repeatedly without structural fatigue.
In a paper published in the Journal of Mechanics and Physics of Solids, the USC team explains that a typical battery works through a repetitive cycle of inserting and extracting li-ions from electrodes. This process expands and compresses the electrode lattices and these volume shifts create microcracks, fractures, and defects over time, which lead to structural degradation and decreased battery capacity.
“Eventually, we need to replace these batteries, which is not only expensive but also depletes the rare earth elements used in making them,” the group said in a media statement.
To discourage the degradation, Delin Zhang, lead author of the article who studies intercalation materials —a class of materials used as electrodes in lithium-ion batteries— stretches these intercalation electrodes ahead of time. This change in the initial stress state regulates the phase transformation voltages, thus making electrodes more resilient to fracture or amorphization, which means losing their crystalline properties.
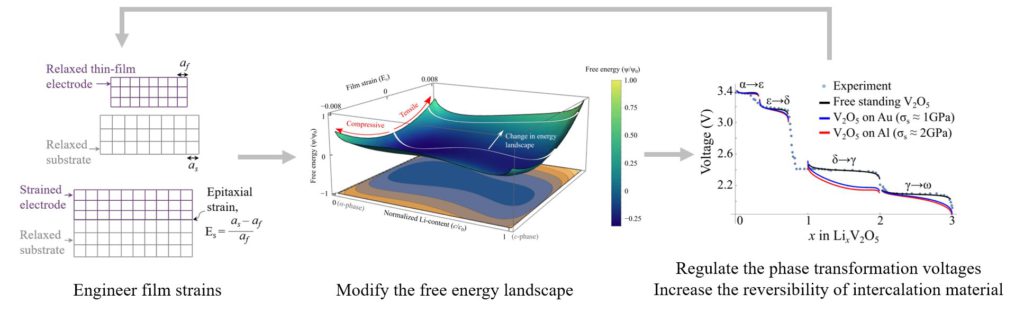
“By stretching the electrodes prior to charging and discharging, we are changing the energy landscape across which an electrode goes from the charged to the discharged state,” Zhang said in the media brief.
“This initial strain allows us to reduce the energy barrier for these transformations and prevent detrimental lattice deformations that lead to material failure. This change in the energy landscape helps prevent microcracks and fractures, protecting the battery’s sustainability and energy storage capacity.”
According to the researcher, an added benefit of this approach is that by stretching the electrodes, the battery can also operate in a wider voltage window, making it more efficient in its energy storage capacity.
Zhang’s development is also believed to be a step forward toward safer, more sustainable batteries while tackling the mechanical challenges imposed by flammable liquid electrolytes typically used in batteries by substituting them for solid materials.
Co-author Ananya Renuka-Balakrishna explained that solid objects can deteriorate over time when repeatedly stressed, and said once a crack is introduced, the two sides of a surface will lose contact. In the case of the battery, without the connection, it’s difficult to transport ions across the material.
In Renuka-Balakrishna’s view, the novelty of this approach is that instead of finding a new material to improve battery lifespan, it becomes possible to improve an existing material’s lifespan by introducing fundamental mechanics concepts.
“Mechanics hasn’t always been an integral part of developing batteries,” Renuka-Balakrishna said. “But now engineers can play with this theory/tool Zhang has created and work to engineer the lifespans of battery materials.”
The team believes that improving the lifespans of batteries would benefit users of electronic devices and electric vehicles enabling longer use of devices and minimizing battery replacement, thus saving money and resources over time.
{{ commodity.name }}
{{ post.title }}
{{ post.date }}
Comments