Scientists propose new ‘salty’ non-toxic gold extraction process
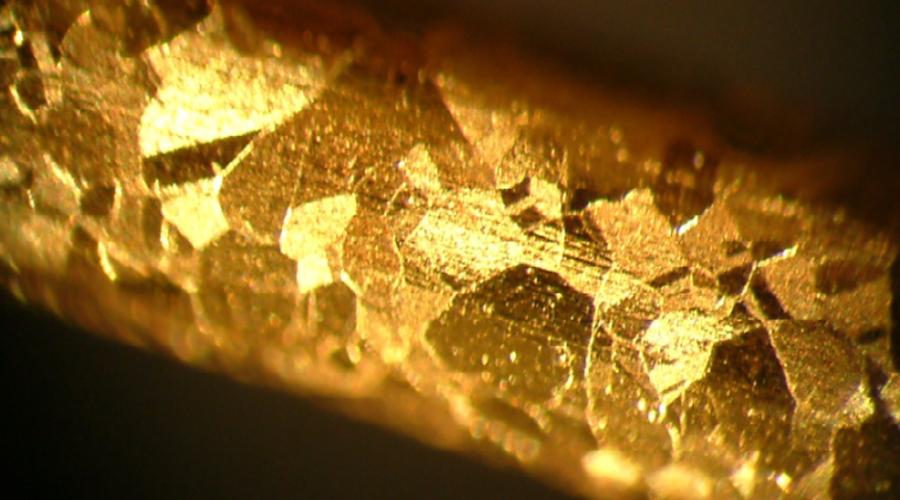
Researchers at Finland’s Aalto University have published a paper in the journal Chemical Engineering in which they describe a new scalable, non-toxic alternative to cyanide for gold extraction from ore.
The new process is based on the use of chloride, one of two elements in table salt, for the leaching and recovery of the yellow metal.
“With our process, the amount of gold we’ve been able to recover using chloride is as high as 84%,” Ivan Korolev, lead author of the study, said in a media statement. “In comparison, using the standard cyanide process with the same ore yielded only 64% in our control experiment.”
The novel approach is called electrodeposition-redox replacement (EDRR) and it combines electrolysis, which uses electric currents to reduce gold or other metals present in the leaching solution, and cementation, which adds particles of other metals to the solution to react with the gold.
Using copper to test it out, Korolev and his colleagues applied short pulses of electricity to create thin layers of metal on the electrode and cause a reaction that encourages gold to replace the copper layer by layer.
“The method has low energy consumption and doesn’t require the addition of any other elements,” the researcher said.
The lab work was conducted in collaboration with Finnish mining-technology giant Metso Outotec, which invited the scientists to work at its research center in western Finland.
“Collaborating with Metso Outotec allowed us to develop the method in a way that’s much closer to real-world implementation,” Korolev said. “We started with about 9% recovery, but it then grew to 25%, and soon we were hitting 70% — sometimes we even achieved close to 95%.”
According to the doctoral candidate, it is the first time that an experiment such as this has been conducted in a large-scale setting. Given the positive results, he expects to see mining companies interested in the technology and willing to test with their own ore on site.
“The extraction methods of the past have always left some valuable metals behind. Now, as demand for metals grows all the time, even these small amounts are important,” he said. “I think we can still increase the yield with our EDRR technology. Perhaps we cannot reach 100%, but I believe we can hit the 90% mark or more.”
More News
{{ commodity.name }}
{{ post.title }}
{{ post.date }}
5 Comments
Victoria Moya
Very good news
Udeinya Chukwudum T
It is a good development in the refining sector. I will love to have details of the process. For our work.
Valentina Ruiz Leotaud
The full details of the process are available in the original paper https://www.sciencedirect.com/science/article/pii/S1385894721038626?via%3Dihub
Rahul Bhaduri
Have you considered COMMERCIAL materials of construction under this highly corrosive chloride media at 95C? if there is any OPEX savings through increased metal recovery, it may be obfuscated with the CAPEX required for exotic material requirements including Hastelloy & Ti alloys…
Jennifer Pauli
Thank you for sharing. Very useful information. Science does not stand still and that is wonderful. Students should do scientific work, it is their responsibility. I have been using and recommending to my clients the services of a https://bestessayservicesradar.com/essaypro-review/. My experience is that they are a very reliable and useful company. My recommendation is that you think about hiring them when working on your essay. If you want to get prepared, then take a look, and I am sure you will find one that will fit your requirements!