Scientists find ideal conditions to produce high nickel-based batteries
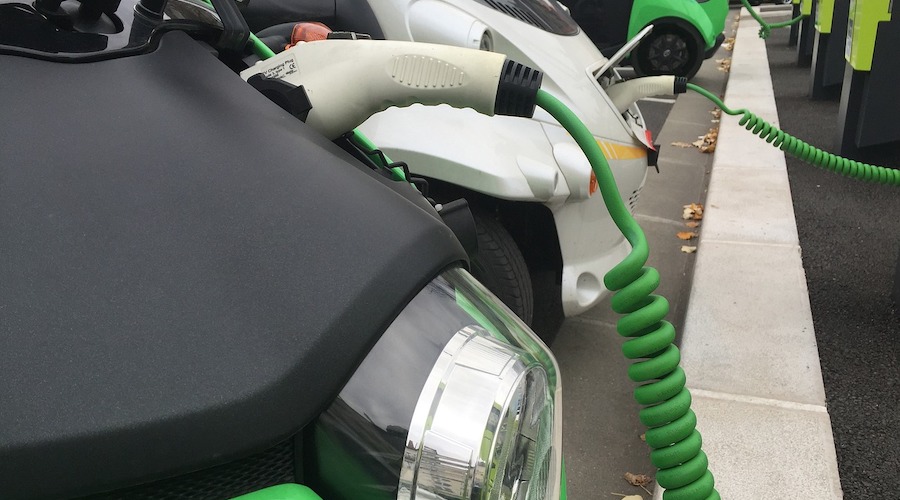
New research conducted at the University of Warwick in the UK found that the drier the conditions in which high nickel-based battery cathodes are stored and processed, the better the battery performs.
High-Ni cathode materials are prone to reactivity and instability if exposed to humidity, therefore how they are stored in order to offer the best performance is crucial.
In a paper published in the journal Electrochimica Acta, the Warwick scientists explain that to find those ideal storage conditions, they exposed NMC-811 (high-Ni cathode material) to different temperatures and humidities, then measured the material’s performance and degradation in a battery over a 28-day period, analyzing them using a combination of physical, chemical and electrochemical testing. This included high-resolution microscopy to identify the morphological and chemical changes that occurred at the micron and sub-micron scale during the batteries charging and discharging.
The driest conditions, at dew points of around -45 degrees Celsius, are the best for storing and processing the materials
The storage conditions included vacuum oven-dried, as exposed (to humidity) and a control measure. The researchers looked for surface impurities, which include carbonates and H2O, and found there were three processes that can be responsible for impurities, namely, residual impurities emanating from unreacted precursors during synthesis; higher equilibrium coverage of surface carbonates/hydroxides (present to stabilize the surface of Ni-rich materials after the synthesis process); and impurities formed during ambient storage time.
They found that in all conditions, (oven-dried and as-exposed) showed inferior first discharged specific capacity and cycling performance, compared to the control. However, the as-exposed measure showed that after 28 days of ambient moisture exposure the H2O and CO2 react with the Li+ ions in the battery cell, resulting in the formation of lithium carbonate and hydroxide species.
The formation of carbonates and oxides on the surface of NMC-811 contributes to the loss of the electrochemical performance during the ageing of the materials, due to the inferior ionic and electronic conductivity, as well as the electrical isolation of the active particles. This means that they can no longer reversibly store lithium ions to convey “charge.” An SEM analysis confirmed the inter-granular porosity and micro-cracks on these aggregate particles, following the 28 days of ambient exposure.
This allowed the scientists to conclude that the driest conditions, at dew points of around -45 degrees Celsius, are the best for storing and processing the materials, in order to then produce the best battery performance.
Conversely, humidity conditions and exposure at junctions along the manufacturing process will cause the materials and components to experience degradation, which results in a shorter battery lifespan.
{{ commodity.name }}
{{ post.title }}
{{ post.date }}
Comments