Nickel-rich cathodes show promising results for longer-lasting EV batteries
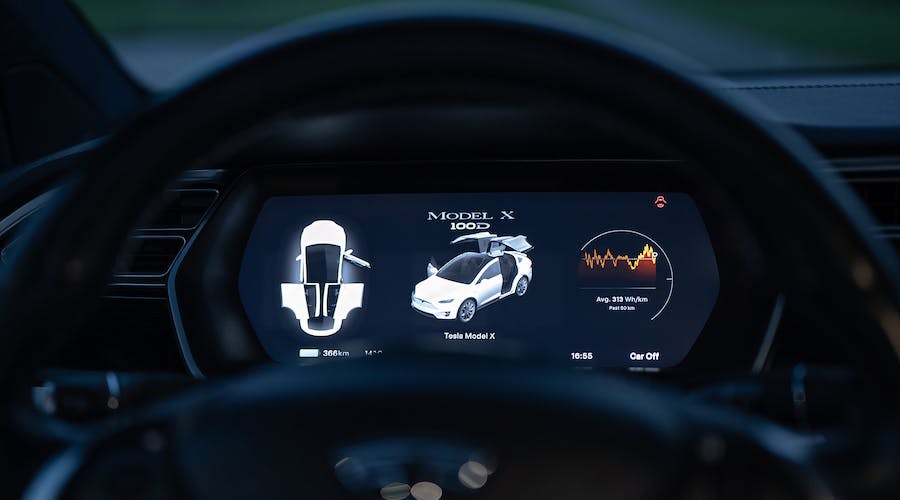
A cost-effective approach for synthesizing single-crystal, high-energy, nickel-rich cathodes may open up the bottleneck that affects cell-level energy capacity and cell cost in lithium-ion batteries. This, in turn, could increase electric vehicles’ ability to store more energy per charge and to withstand more charging cycles.
In a paper published in the journal Energy Storage Materials, researchers with the Pacific Northwest National Laboratory and Albemarle Corporation explain that nickel-rich battery vision cathodes for conventional EV batteries use a cocktail of metal oxides—lithium nickel manganese cobalt oxides (LiNi1/3Mn1/3Co1/3O2), abbreviated NMC. When more nickel is incorporated into a cathode, it greatly increases the battery’s ability to store energy, and thus, the range of the EV. As a result, nickel-rich NMC (such as NMC811, where the “8” denotes 80% nickel) is of great interest and importance.
However, high-nickel NMC cathodes formed using the standard method are agglomerated into polycrystal structures that are rough and lumpy. This meatball-like texture has its advantages in regular NMC. For NMC811 and beyond, though, the bulbous polycrystal fissures are prone to splitting apart, causing material failure. This renders batteries made using these nickel-rich cathodes susceptible to cracking; they also begin to produce gases and decay faster than cathodes with less nickel.
One strategy to fix this problem is to convert that lumpy, polycrystal NMC into a smooth, single-crystal form by eliminating the problematic boundaries between the crystals—but this conversion is easier said than done. In laboratories, single crystals are grown in environments such as molten salts or hydrothermal reactions that produce smooth crystal surfaces. However, these environments are impractical for real-world cathode manufacturing, where lower-cost, solid-state methods are preferred.
In these more typical solid-state approaches, an NMC cathode is prepared by mixing a metal hydroxide precursor with lithium salt, directly mixing and heating those hydroxides—and producing the agglomerated (lumpily clustered) polycrystal NMC. Using a multiple-step heating process results in micron-sized crystals, which are still agglomerated, so the undesirable side effects persist.
Pre-heating step
To solve these issues, the research team introduced a pre-heating step that changes the structure and chemical properties of the transition metal hydroxide. When the pre-heated transition metal hydroxide reacts with lithium salt to form the cathode, it creates a uniform single-crystal NMC structure that looks smooth, even under magnification.
“The one-step heating process of precursors seems straightforward, but there is a lot of interesting atomic-level phase transition involved to make the single crystal segregation possible,” said Yujing Bi, first author of the paper. “It is also convenient for industry to adopt.”
Bi and colleagues are now scaling up this single-crystal NMC811 to a kilogram level by using lithium salt provided by Albemarle. The scaled single crystals were tested in realistic 2Ah lithium-ion pouch cells, using a standard graphite anode to make sure that the new cathode mainly dictated the battery’s performance.
The prototype battery equipped with the scaled single crystals was stable, even after 1,000 charge and discharge cycles. When the researchers looked at the microscopic structure of the crystals after 1,000 cycles, they found no defects and a perfectly aligned electronic structure.
“This is an important breakthrough that will allow the highest energy density lithium batteries to be used without degradation,” Stan Whittingham, a Nobel Laureate and distinguished professor of chemistry at Binghamton University, said. “In addition, this breakthrough on long-lived batteries will be critical to their use in vehicles that can be tethered to the grid to make it more resilient and to support clean renewable energy sources.”
Scaling up
The synthesis method for the single-crystal, nickel-rich cathode is both innovative and cost-efficient. It is also easy to scale up, as it is a drop-in approach that allows cathode manufacturers to use existing production facilities to conveniently produce single-crystal NMC811—and even cathodes with more than 80% nickel.
“This is a fundamentally new direction for large-scale production of single crystal cathode materials,” said Jie Xiao, the principal investigator of the project. “This work is only part of the cathode technology we are developing at PNNL. In collaboration with Albemarle, we are addressing the scientific challenges in the synthesis and scaleup of single crystals and reducing the manufacturing cost starting from raw materials.”
More News
First Quantum pulls back from arbitration on Panama copper mine
Signals potential for more negotiations with the nation over the Cobre Panama mine that’s been shuttered for more than a year.
March 31, 2025 | 04:30 pm
Freeport-McMoRan lowers first-quarter gold sales forecast
The company said it expects first-quarter gold sales to be roughly 100,000 ounces below its prior forecast of 225,000 ounces.
March 31, 2025 | 03:41 pm
{{ commodity.name }}
{{ post.title }}
{{ post.excerpt }}
{{ post.date }}
Comments