Metaspectral’s ore resource evaluation system gets IMII innovation award
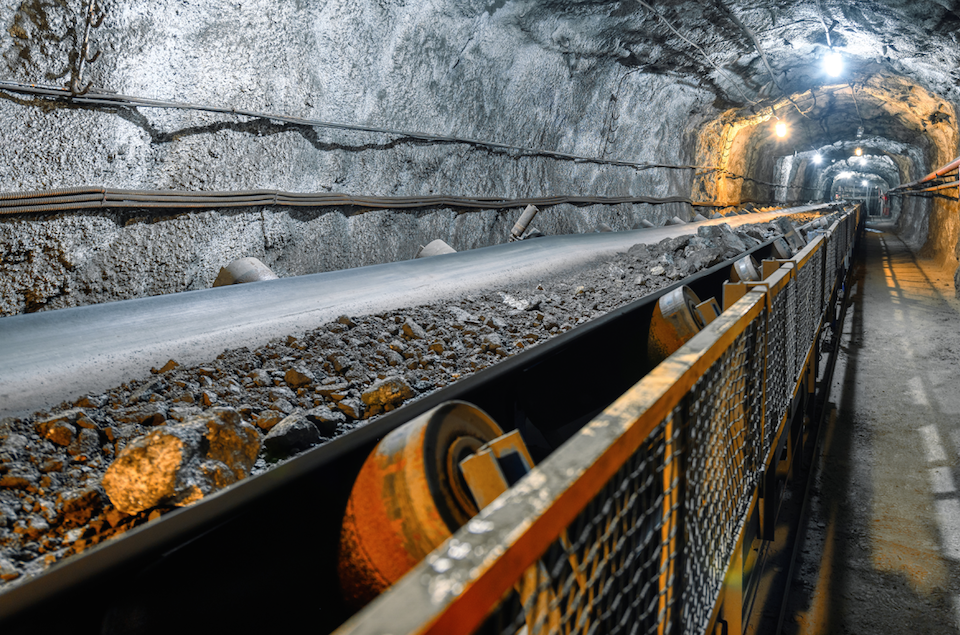
Metaspectral this week introduced its ore resource evaluation system (ORES) at the International Minerals Innovation Institute (IMII) DEMOday in Saskatchewan and was named the “Most Actionable” solution and awarded a 2024 Innovation Award for the technology.
IMII is a non-profit organization jointly funded by industry and government to develop and implement innovative education, training, research, and development partnerships to support the minerals industry.
ORES will automate the sampling process of potash, uranium, and other ores, providing comprehensive, real-time analysis of ore composition and quality, Metaspectral said. The technology uses artificial intelligence (AI) to analyze data from hyperspectral sensors placed along conveyor belts that move the ores, allowing for continuous, non-contact, non-destructive analysis.
“Our integrated software platform can provide immediate information to operators about ore quality and composition. This can guide early decision-making in the milling process and make it possible to identify and select only ores of a predetermined grade for processing,” CEO Francis Doumet said in a media statement.
“Enabling the selective processing of ores makes it possible to reduce costs and lessen environmental impact, using less water and energy, while producing fewer tailings and less waste.”
This comprehensive level of analysis is not possible using traditional methods of ore sampling, which only analyzes a single point on the sample, the Vancouver-based company said.
ORES, conversely, captures complete data about the materials when the ore passes by the spectral sensors on a conveyor belt. These sensors capture hyperspectral data, which measures photon interactions to produce unique spectral signatures that can be interpreted to uncover detailed information about the properties of the ore at the molecular level.
This high level of detail has significant potential to improve the mining sector’s operational efficiency and profitability while lessening its environmental impact, the company said, adding that the technology can also help to reduce the need for human exposure to ores, which can enhance worker safety.
Metaspectral’s technology has been validated and is already deployed commercially in other sectors, including plastics recycling. A similar conveyor belt configuration has achieved identification accuracies exceeding 92% at high speeds for difficult-to-sort materials such as thin plastic film, black material, and transparent material by polymer type, the company said.
More News
Rio Tinto, Founders Factory’s Mining Tech Accelerator invests in startups from US and OZ
April 23, 2025 | 04:02 pm
{{ commodity.name }}
{{ post.title }}
{{ post.date }}
Comments