Kutcho de-risks copper-zinc project with eye to controlling costs
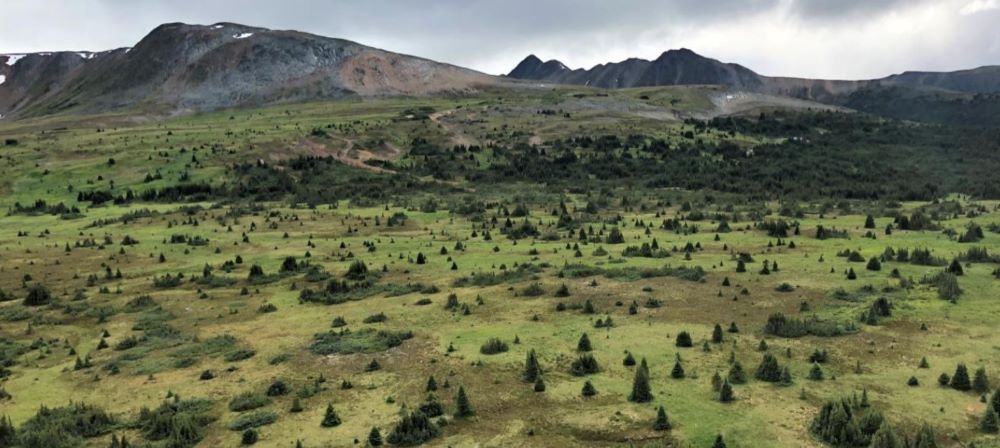
Kutcho Copper (TSXV: KC) is re-examining the 2021 feasibility study for its Kutcho high-grade copper-zinc project with an eye toward de-risking the project and controlling capital costs. The 100%-owned property is located 120 km east of Dease Lake in northern British Columbia.
The feasibility study estimated pre-production capital requirements to be C$483 million (undiscounted), sustaining costs of C$90 million over the mine life, plus C$34.5 million for closure and rehabilitation. All-in sustaining costs would be $1.80/lb. of copper-equivalent.
President and CEO Vince Sorace says the engineers and designers have been looking to de-risk the project since the study was completed. They say by delaying the start of underground operations, C$50 million can be saved, according to in-house estimates. That saving and the existing streaming deal with Wheaton Precious Metals (C$76 million towards development capital), should bring the pre-production capex down to C$350 million.
Kutcho also plans to take advantage of the federal Critical Minerals Strategy and its C$1.5 billion promise to bring clean hydro power to northern projects. “Kutcho is engaged in discussions with federal and provincial government regarding potential extensions of existing transmission lines towards its project,” said Sorace.
As mentioned, deferring the start of underground mining to year two of operations would reduce the initial capital by C$40 million with little impact on both the net present value and internal rate of return as outlined in the feasibility study.
Thought is being given to replacing the semi-autogenous mill circuit with tertiary crushing plus ball milling, which would save both capital and power consumption. This could result in a capital saving of C$8.5 million, and studies will continue. Other processing initiatives include changes to primary grind size, reagent consumptions, and grinding media.
The feasibility study also recommended more bulk ore sorting tests. A better understanding of low-grade particle sorting dynamics may allow more material to be mined from the edges of the proposed open pit. Tests of using ore sorter rejects and binders for backfill are continuing.
Closure plans call for returning all potentially acid generating (PAG) waste rock to the bottom of the pit or underground to reduce acid rock drainage and metal leaching. Non-acid generating waste rock will be used to cover the PAG material. This strategy should decrease the length of post-closure water management required.
More News
Trump planning to stockpile deep-sea minerals to counter China: FT
April 13, 2025 | 07:56 am
Goldman Sachs upgrades gold forecast again to $3,700
April 12, 2025 | 08:05 pm
{{ commodity.name }}
{{ post.title }}
{{ post.date }}
Comments