How technology can help miners comply with new global tailings standard guidelines
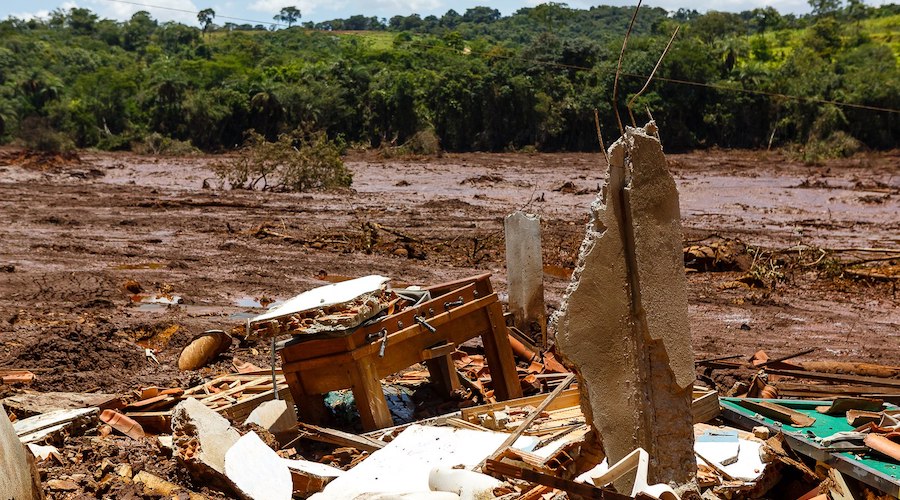
Technology is key in helping miners comply with the recently released Global Industry Standard on Tailings Management, a set of guidelines aimed at strengthening current practices with the goal of zero harm to people and the environment.
Prepared by the United Nations Environment Program, Principles for Responsible Investment (PRI) and the International Council on Metals and Mining (ICMM), the standard was a direct response to a series of lethal accidents that took place in recent years, with the failure of the tailings dam at Vale’s Córrego do Feijão mine being the latest of such incidents.
According to Robin Bolton, head of sustainability at IsoMetrix – a company that develops software for integrated risk management – one of the major challenges that miners face when it comes to preventing these accidents is that 79% of them use multiple tools in their risk management process.
In his view, this fragmented approach causes operators to miss interconnected risks or ‘golden threads,’ which are the links between companies’ processes, threats, controls and events. By not having an understanding of these ‘golden threads,’ mines are more likely to ignore the early warning signs of a tailings disaster.
Operators tend to miss interconnected risks or ‘golden threads,’ which makes then more likely to ignore the early warning signs of a tailings disaster
The key is, then, using technology to continuously track an array of complex site-specific risks and detect these connections.
“By linking datasets and asset performance data that were previously siloed through a Governance, Risk and Compliance (GRC) solution, mines are able to gain a deeper understanding of their critical tailing controls in line with the global standard,” Bolton told MINING.COM.
“By integrating into pre-existing systems, including weather tracking, engineering control monitoring, production rates and more, GRC platforms can detect faults and alert critical stakeholder groups of a potential incident which can then be managed appropriately. Through a unified view of tailing facilities, mines can ensure its processes comply with the new tailing management standards and mitigate potential disaster.”
Besides ensuring safety and compliance while operative, Bolton said miners ought to remember that they are still liable for an array of risks, including security, safety and contamination after a tailings dam closes. This is why he is convinced that remote monitoring through a digital risk management ecosystem is essential to detect faults and alert risk managers if an action is needed.
MDC: Do you see mining companies leaning towards a specific trend/solution when it comes to tailings management?
Bolton: Over the past year, mines have been focused on integrating new types of data collection and making it quickly available to operators. The new types of data include satellite imagery, data gathered through IoT and more. This gives mines a holistic view of its site-specific risks, allowing them to identify new controls that can mitigate incidents. By tying this data into its overall risk assessment, mines can better assess their operations against new and existing ESG standards, such as the new tailing management standards.
MDC: What, do you think, has changed for miners following the release of the global standard on tailings management?
Bolton: The new tailing management standards are going to have the largest impact on internal management and compliance processes. To meet the standards, mines must update their policies and standard operating procedures. Within these operational updates, they should determine how technology can fit into its larger operational strategy to automate monitoring the necessary controls. Through a holistic view of risk made possible by integrated technology, mines can create a universal tailing management approach to meet the new global standards, while still taking country-specific requirements into account.
MDC: Did IsoMetrix have to change/modify anything in its tailings management solution once the global standard on tailings management was launched?
Bolton: There’s a close alignment between our tailing management solution and the requirements of the new tailing management standards, especially as it relates to understanding the risks and controls that can minimize a potential event.
However, to ensure that our solution fully equips customers with the resources they need, we are currently advancing the solution’s IoT integration capabilities to ensure that relevant data, such as monitoring and production data, and images from satellites and thermal cameras, can seamlessly flow into the platform. We are also implementing new auditing processes that capture the content of the tailing management standards, so mines can gauge how they are aligned with the requirements, and we are adding-in management of change functionality to better track a mine’s critical controls as well as the skills and training register.
MDC: How does the solution work exactly?
Bolton: The tailing management solution is a central repository for managing all tailing related information. Through key health, safety and environmental modules, along with emergency preparedness and response modules, mines can ensure their critical controls are in place and monitored. Also, by integrating into already existing systems, the solution imports data from various monitoring modules to manage and analyze risks, such as water, rehabilitation and air quality. This allows the mine to set thresholds for particular metrics in one universal built-in dashboard.
Often, the responsible tailing managers work remotely, and through IsoMetrix’s mobile app and automated alerting system, mining organizations can capture required information in detail in real-time. Through the integrated risk ecosystem our TMS creates, mines can proactively identify missing safeguards to minimize the likelihood and consequences of a tailings incident.
{{ commodity.name }}
{{ post.title }}
{{ post.date }}
3 Comments
Serhii
There are currently two problems. The first is the lack of willingness to invest in the safety of tailing storage. The second is the lack of desire to invest in qualified personnel. All tailings storage technologies have been developed long ago and they are quite reliable. Two factors remain: competence and material costs. The combination of these two points together give a positive result of the operation of tailing.
Charles Becket
Is the Global standard mandatory for new mine applications? This standard came out just weeks before an Enviromental Effects Statement was published for a mineral sands mine in a a sensitive location..
Valentina Ruiz Leotaud
The standard is voluntary but members of the International Council on Metals and Mining – which include Vale, and which represent about a third of the global mining industry – will be required to implement the standard.