Graphite One could take a leading role in loosening China’s grip on US graphite market
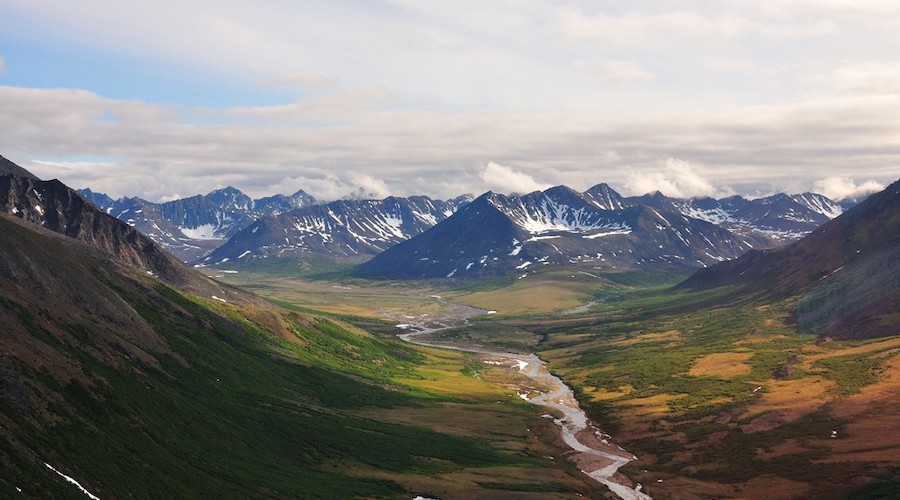
Due to its natural strength and stiffness, graphite is an excellent conductor of heat and electricity. It is also stable over a wide range of temperatures.
Graphite is thus found in a wide range of consumer devices, including smartphones, laptops, tablets and other wireless devices, earbuds and headsets. Besides being integral to electric car batteries, graphite is found in e-bikes and scooters.
A White House report on critical supply chains showed that graphite demand for clean energy applications will require 25 times more graphite by 2040 than was produced in 2020.
Graphite has the largest component in batteries by weight, constituting 45% or more of the cell. Nearly four times more graphite feedstock is consumed in each battery cell than lithium and nine times more than cobalt.
Graphite is therefore indispensable to the EV supply chain.
BloombergNEF expects graphite demand to quadruple by 2030 on the back of an EV battery boom transforming the transportation sector. It is not an exaggeration to say that electrification of the global transportation system doesn’t happen without graphite, copper and lithium.
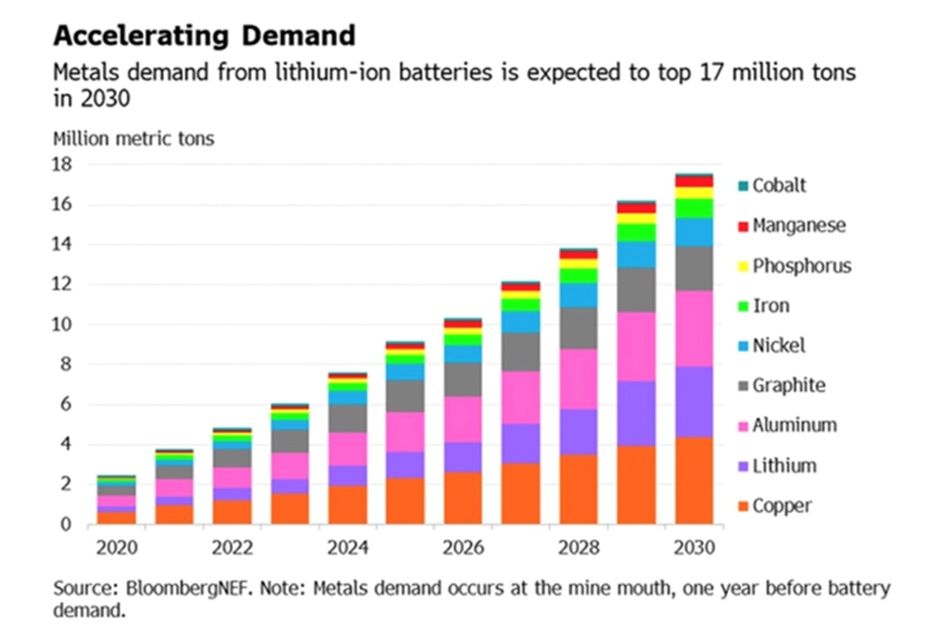
The lithium-ion batteries in electric vehicles are composed of an anode (negative) on one side and a cathode (positive) on the other. Graphite is used in the anode.
The cathode is where metals like lithium, nickel, manganese and cobalt are used, and depending on the battery chemistry, there are different options available to battery makers. Not so for graphite, a material for which there are no substitutes.
Synthetic vs natural graphite
Synthetic, or artificial graphite, and natural graphite are both used in battery anode applications, but synthetic dominates the market.
China is the number one graphite producer in the world, outputting 850,000 tonnes in 2022, and accounting for two-thirds of mine supply. Moreover, the Asian nation also controls 80% of synthetic graphite production.
Some battery-makers are keen on natural graphite due to its lower carbon emissions compared to synthetic graphite, which is made from petroleum coke.
Synthetic graphite’s primary application is in the graphite electrodes used for electric arc furnace steelmaking, which accounts for 70-80% of graphite electrode consumption. The market for this sector is estimated at 1.6 million tons in 2024, and is expected to reached 1.9Mt by 2029, according to Mordor Intelligence.
The boost is partly due to the Chinese government’s recent Work Plan for Steady Growth of the Iron and Steel Industry, which promotes the expansion of steel production with electric arc furnaces.
Total synthetic graphite consumption is pegged at 3.04Mt this year, compared to 1.68Mt for natural graphite.
Battery supply chain could reach $400 billion
Global demand for batteries is increasing largely due to the imperative to switch from gas-powered to electric vehicles and the broader energy transition from fossil fuels to renewables.
According to a new report from Bain & Company, global battery demand is expected to quadruple between 2023 and 2030 to 4,100 gigawatt hours (GWh).
The report emphasizes that lithium-ion batteries will remain the dominant technology for the foreseeable future, with nickel-manganese-cobalt (NMC) and lithium-iron-phosphate being the most common cathode chemistries.
“Emerging technologies such as solid-state and high-density sodium-ion are still in the prototype and pilot manufacturing stages, and their market share is expected to stay in the single-digit range until 2030,” the firm said.
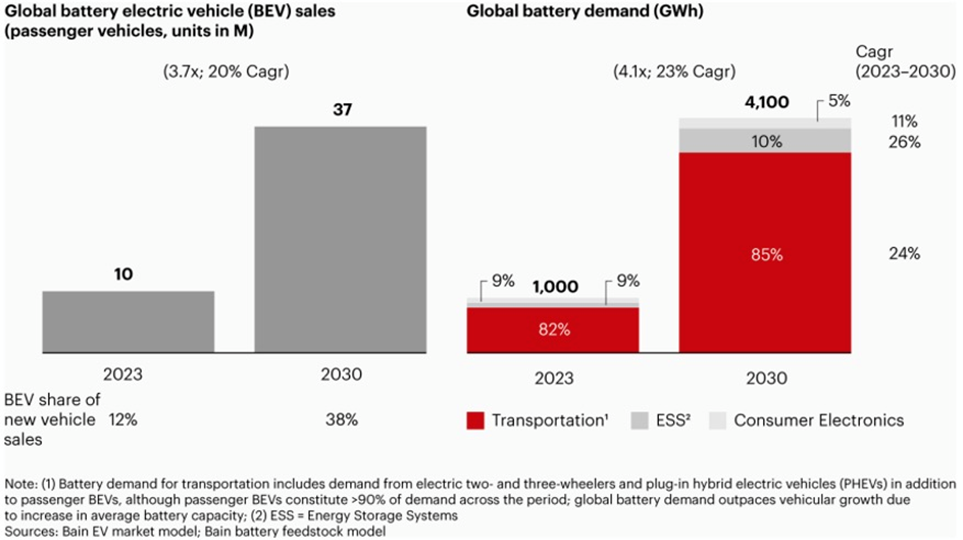
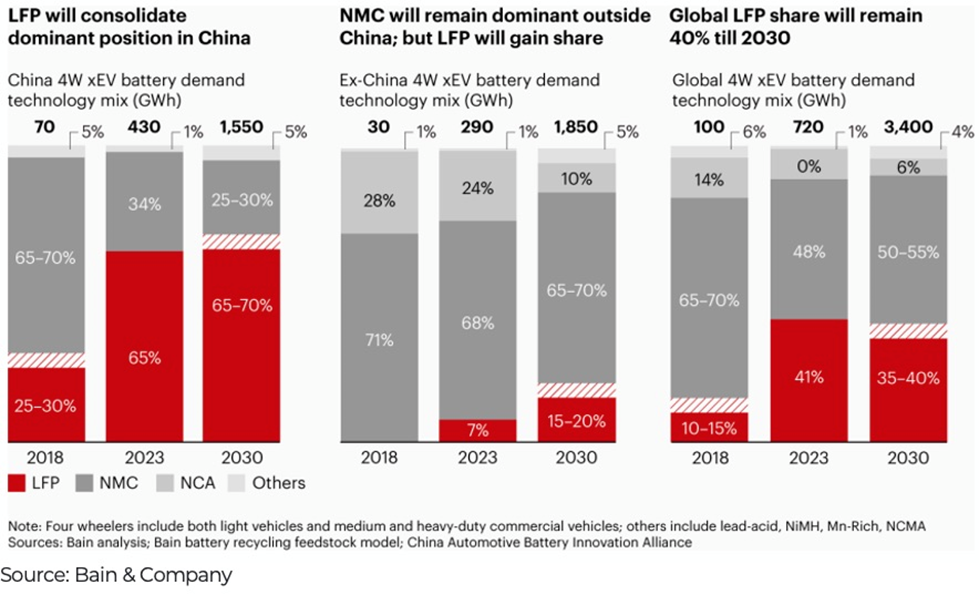
A 2023 article by McKinsey, a consulting company, reported on a 2022 analysis by the McKinsey Battery Insights team. The analysis projects that the entire Li-ion battery supply chain, from mining through recycling, could grow by over 30% annually from 2022 to 2030, when it would reach a market value of more than $400 billion.
Demand for these batteries is seen increasing from about 700 gigawatt-hours (GWh) in 2022 to around 4.7 terawatt-hours (TWh) by 2030. Electric vehicles will account for the vast majority of demand — about 4.3 TWh — driven mainly by three factors:
- A regulatory shift toward sustainability, which includes new net-zero targets and guidelines, including Europe’s “Fit for 55” program, the US Inflation Reduction Act, the 2035 ban of internal combustion engine (ICE) vehicles in the EU, and India’s Faster Adoption and Manufacture of Hybrid and Electric Vehicles Scheme.
- Greater customer adoption rates and increased consumer demand for greener technologies (up to 90 percent of total passenger car sales will involve EVs in selected countries by 2030).
- Announcements by 13 of the top 15 OEMs to ban ICE vehicles and achieve new emission-reduction targets.
Energy storage systems are also expected to require a lot of lithium batteries. According to McKinsey,
Battery energy storage systems (BESS) will have a CAGR of 30 percent, and the GWh required to power these applications in 2030 will be comparable to the GWh needed for all applications today.
While much of the demand is expected to come from China, which leads the electric-vehicle market, the consultancy notes the highest growth rates are in the United States and the European Union.
Between 120 and 150 new battery factories will need to be built between 2023 and 2030.
Revenues along the battery supply chain will quintuple from about $85 billion in 2022 to over $400B in 2030, according to McKinsey.
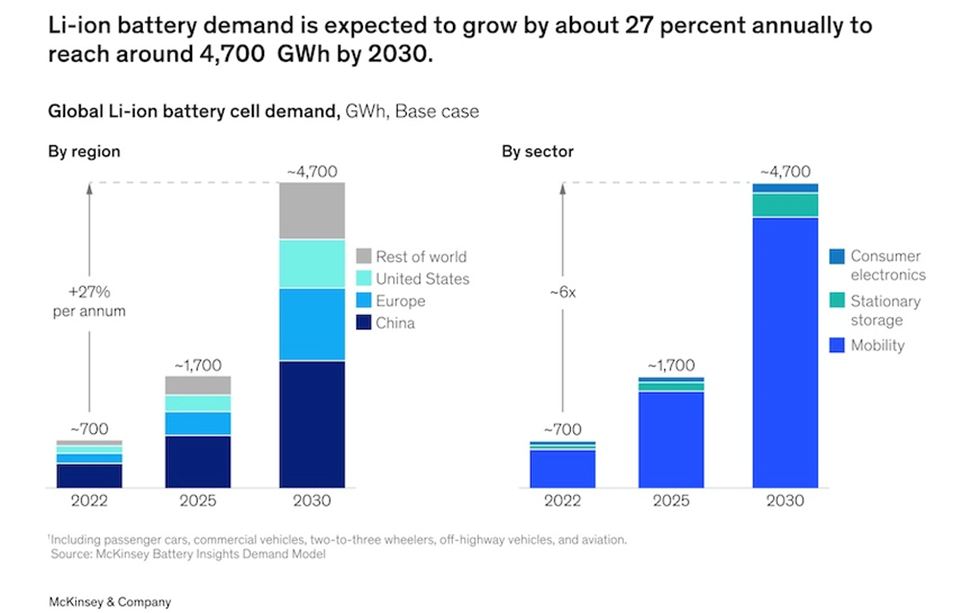
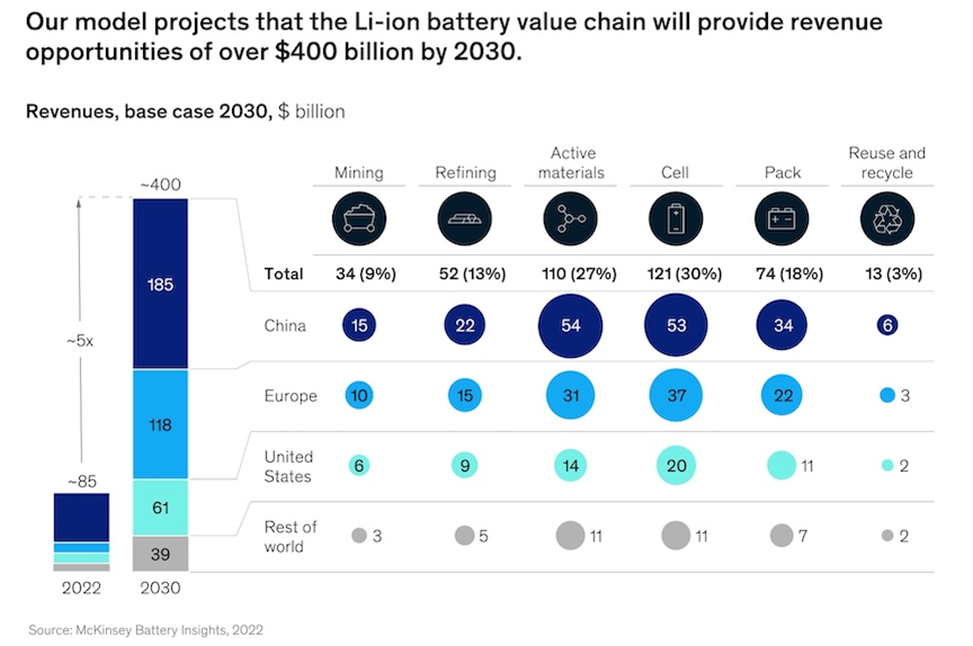
Drilling down to North America, Mordor Intelligence says the North American battery market is expected to grow from $16.1 billion in 2024 to $68.9B in 2029, a CAGR of 33.7%. The firm concurs with McKinsey, in that the market will be driven by the increasing adoption of electric and hybrid vehicles, and the increasing demand for energy storage systems.
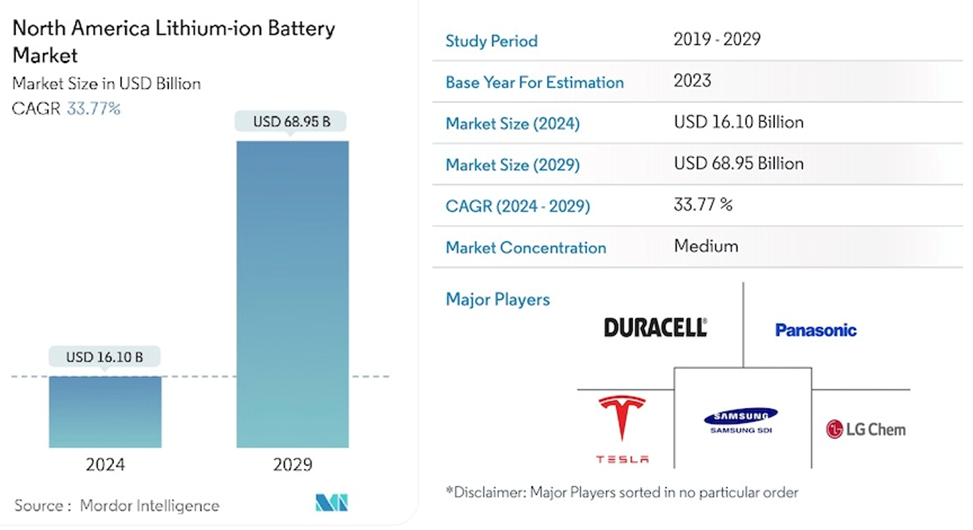
The United States obviously dominates the market for lithium batteries in North America. Revenue was valued at $11.2 billion in 2023 and is expected to reach $35B by 2028, for a CAGR of 25.4%.
The Canadian battery market was valued at just $1.4B in 2023, but it is forecast to nearly triple in five years, growing at a CAGR of 22.1% and reaching $3.9B by 2028.
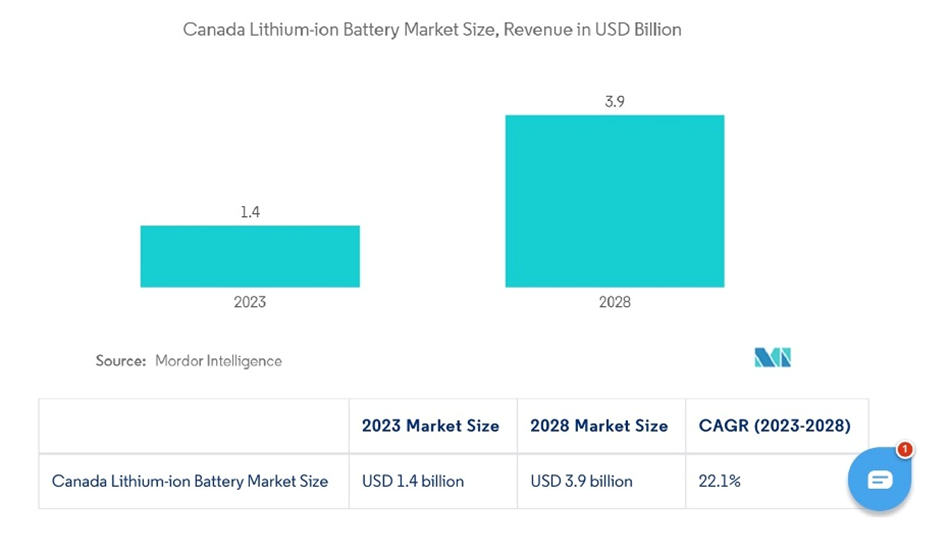
The most important trend in North America, according to Mordor, is automotive batteries becoming the fastest-growing segment of the market. Specifically:
- Lithium-ion battery systems drive the performance of plug-in hybrid and electric vehicles by meeting OEM requirements for driving range and charging time. Their high energy density, fast recharge capability, and high discharge power make lithium-ion batteries the preferred technology.
- Lithium-ion batteries are considered environmentally friendly compared to other batteries as they do not contain toxic materials like lead or cadmium. Additionally, lithium-ion batteries provide a high power output.
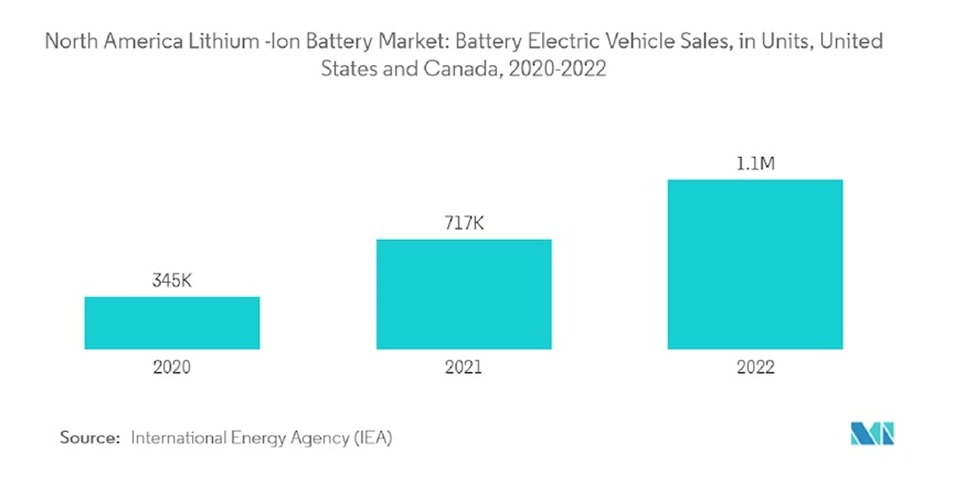
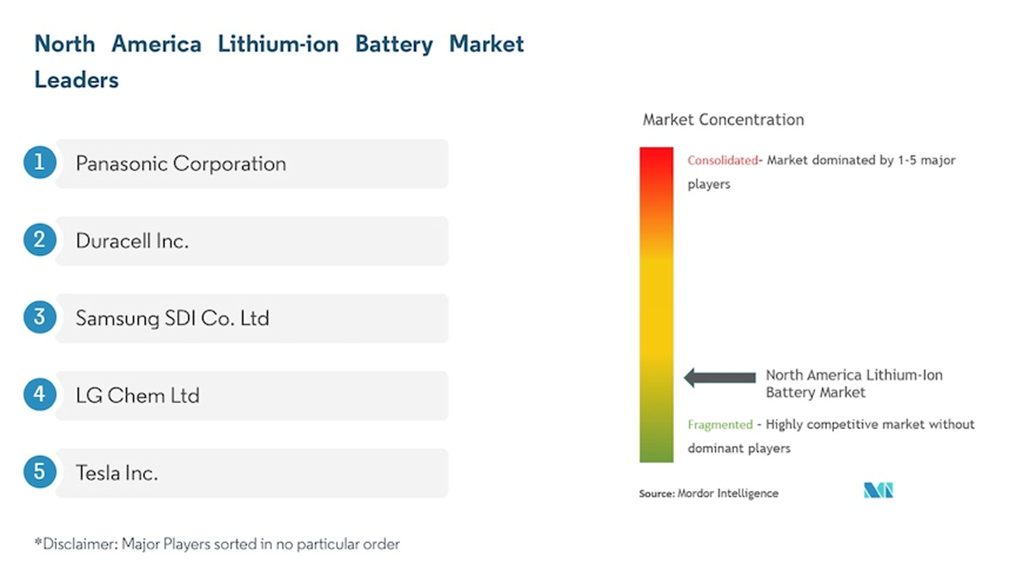
Anodes
The battery anode market is dealt with separately despite anodes being part of lithium-ion batteries. A report by Polaris Research valued the global anode market at $11.5 billion in 2023. By 2032, revenues should reach $123.7B, with the industry growing at a CAGR of 30.9%.
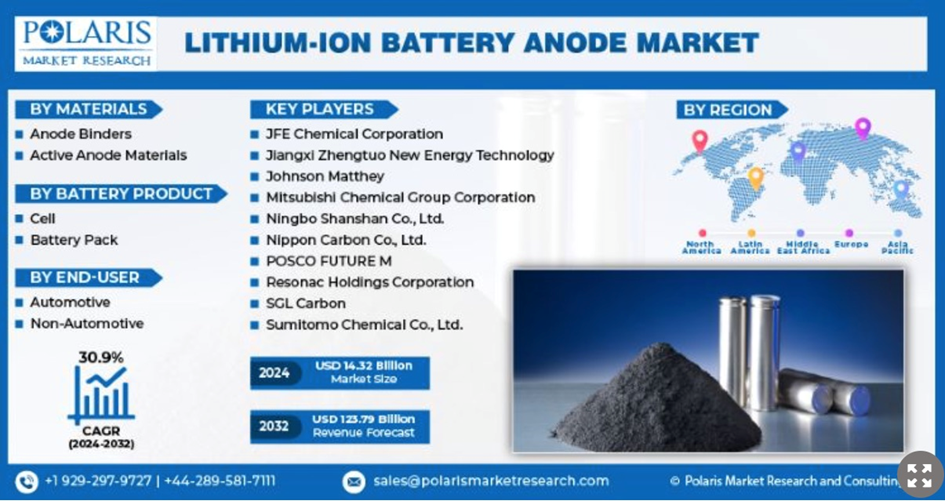
The main reason for such a high growth rate is increasing EV adoption.
“The lithium-ion battery anode market is experiencing notable growth due to electric vehicle acquisition. The growing approval of plug-in hybrids and EVs instantly translates into growing demand for lithium-ion batteries,” states Polaris Market Research via PR Newswire.
Another report by Markets&Markets projects anodes will grow from a $12 billion industry in 2023 to $46.5 billion in 2028.
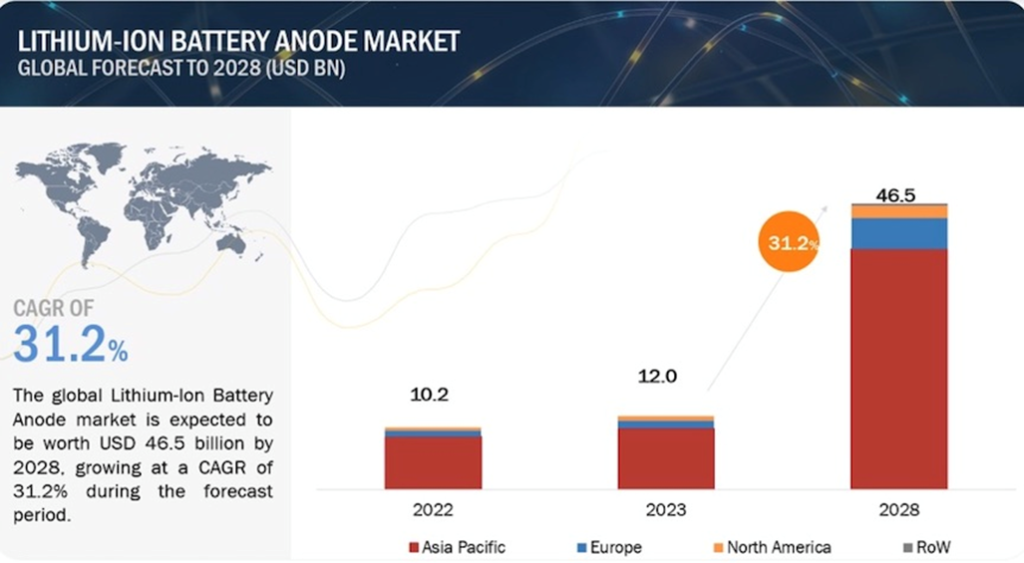
The report concurs with Polaris Research’s observation that electric vehicles are the key demand driver, but adds that industrial applications are increasingly adopting lithium-ion batteries for their efficiency and clean-energy benefits.
Growth will be fueled by the rising need for energy storage solutions, the shift toward sustainable energy sources, and government initiatives promoting clean energy adoption, according to the report.
The growth of the anode market will be impacted by factors including technology, the level of demand for electric vehicles, renewable energy integration, and the development of consumer electronics.
EV adoption includes EVs and plug-in hybrids, a key component of which is the anode. Energy storage devices are increasingly used in hybrid automobiles and renewable energy. Lithium-ion batteries have proven to be suitable for large-capacity energy storage systems.
Anodes made from synthetic graphite are expected to be the largest market from 2023 to 2028. Despite its higher cost compared to natural graphite from graphite mines, “its well-defined structure facilitates smoother lithium-ion movement, enabling faster charging and higher reliability,” states Markets&Markets. An additional advantage of synthetic graphite is its longer lifespan compared to natural.
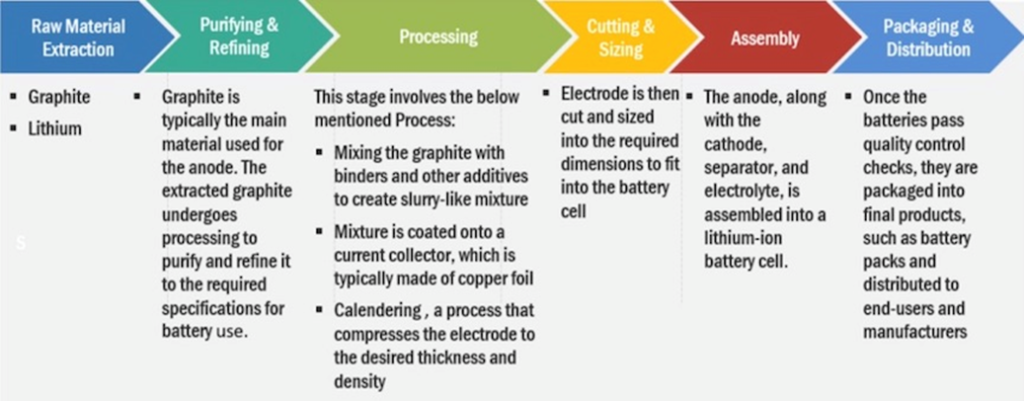
Active anode materials
The anode, also known as the negative electrode, is typically made up of graphite powder baked onto copper foil. According to Targray,
Graphite is a crystalline solid with a black/grey color and a metallic sheen. Due to its electronic structure, it is highly conductive and can reach 25,000 S/cm2 in the plane of a single-crystal.
Graphite is commonly used as the active material in negative electrodes mainly because it can reversibly place Lithium-ions between its many layers. This reversible electrochemical capability is maintained over several of thousands of cycles in batteries with optimized electrodes. However, one requirement for this application is that the Graphite surface must be compatible with Lithium-ion battery chemistry (salts, solvents and binders).
Within the anode market, the active anode material segment is divided into four categories: natural and synthetic graphite, silicon, lithium-ion compounds, and lithium metal.
To be suitable for lithium-ion battery manufacturing, anode materials should meet the following requirements:
- Excellent porosity and conductivity
- Good durability and light weight
- Low cost
- Voltage match with preferred cathode
Defense applications
Virtually every US military system requires mineral components, from steel and titanium to graphite composites and cadmium alloys. Global defense spending shows that military demand is increasing for these platforms, munitions, and thus minerals. (Modern War Institute)
Graphite is the ideal material for defense purposes thanks to its unique properties, i.e., it is able to withstand very high temperatures with a high melting melting point; it is stable at these high temperatures; it is lightweight and easy to machine; and it is corrosion-resistant.
Four ways graphite has transformed aerospace engineering to make it more efficient, are increasing the service life of airplanes; improving fuel economy; having the ability to run hotter engines; and reducing the weight of airplanes.
Fun fact: when an industry giant replaced a single leaded bronze part with a graphite equivalent, it saw a weight decrease of 1.5 lbs. In aerospace, every pound saved equates to $5,000 a year in fuel costs.
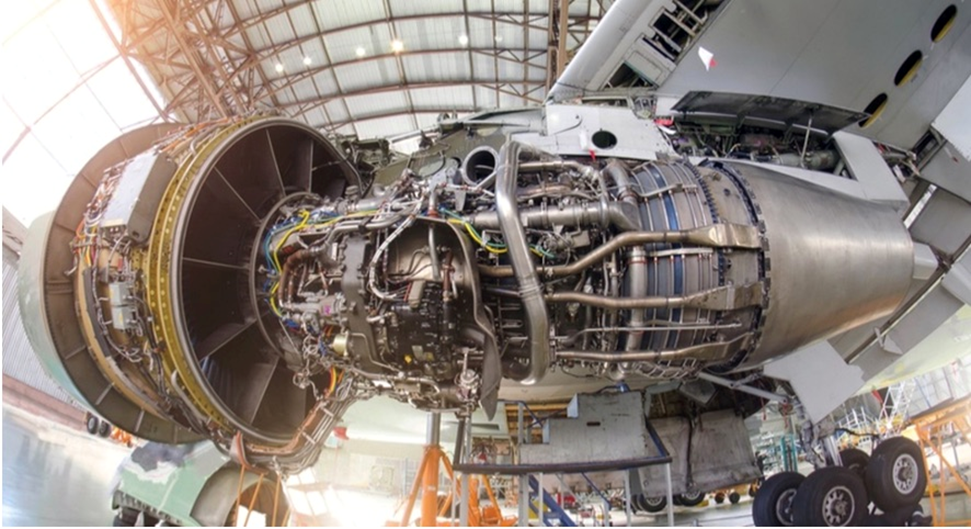
A report last year from the Hague Centre for Strategic Studies found that natural graphite and aluminium are the materials most commonly used across military applications and are also subject to considerable supply security risks that stem from the lack of suppliers’ diversification and the instability associated with supplying countries.
The report assessed the degree of criticality for each of 40 materials deemed critical or soon to be critical. Natural graphite was rated “very high-risk” for air applications, and “high-risk” for sea applications.
In the table below, natural graphite is rated red, very high risk, for its use in fighter aircraft, main battle tanks, submarines, corvettes, artillery and ammunition. Aluminum, used in fighters, tanks, missiles, submarines, corvettes, artillery, ammunition and torpedos, was also rated a very high-risk material.
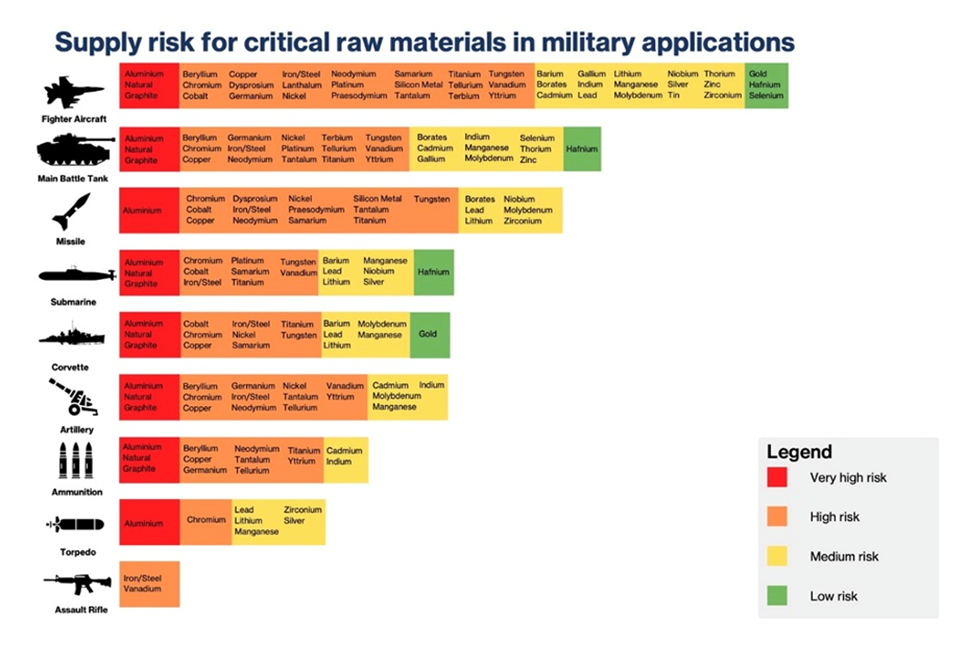
For the construction of tank guns, Howitzers, machine guns in infantry fighter vehicles, and GPS/SAL guidance systems in ammunition, natural graphite is found in combination with other materials to construct these components.
The amount of equipment used by the US military alone demonstrates a captive market for natural graphite. One source reported in 2018, the US government had roughly 440,000 vehicles, 780 strategic missiles, 278 combat ships and 14,000 aircraft.
It notes A key market risk for the US defense sector is a material reliance on a geopolitical competitor that can create a shortage of natural graphite on a whim that would directly impede manufacturing of critical defense systems and equipment in the US.
The Defense Logistics Agency, the same agency that manages the National Defense Stockpile, is reportedly looking for a domestic source of isomolded graphite production, used by the military in several applications, including tactical munitions, strategic rockets and missiles, and large advance-launch systems.
The US military uses graphite flakes to block electromagnetic waves that the enemy might detect and use to target troops in the field. Essentially a type of smoke, synthetic graphite flakes are released from ground-based systems that disperse bulk powders into the atmosphere. The powders, called Micro-260 and K-2, are composed of flakes of various sizes.
It should be pointed out that synthetic graphite, made from petroleum coke, is used in all the downstream industries that produce military equipment components, such as foundries (graphite electrodes) that make steel; and facilities that manufacture wheels for vehicles or body armor for soldiers (various types of graphite molds and dies).
Synthetic graphite is employed directly in graphite nozzles, used in high-powered rockets due to graphite’s ability to withstand extreme temperatures. These graphite components can be as simple as a hole drilled into a synthetic graphite block, or a more advanced, machined nozzle that has its own cooling system.
A new graphite application for military and industrial usages is a graphite oxide patented by the US Army. The water recycling system is designed for washing out tanks and trucks exposed to chemical and biological weapons.
The system filters out impurities at up to 600 gallons of wash water per hour, allowing dumped wastewater to be re-used or safely dumped.
Downstream from military applications, graphite is used widely in the aerospace industry. According to Semco Carbon, heat treating synthetic graphite is used as engineered material to create precision machined plates, posts, nuts and bolts along with heating elements and fixtures used in the heat treatment of aerospace metals such as titanium, stainless steel, and other alloys…
As an extension of heat treating for aerospace, a common graphite use is as a susceptor. “A susceptor is a material used for its ability to absorb electromagnetic energy and convert it to heat (which is sometimes designed to be re-emitted as infrared thermal radiation).”
Another use for graphite is as a mold. Graphite molds are used to cast titanium, aluminum, and stainless steel to near net shapes. Graphite molds are also used for molding non-metal composites. An example of this is for a satellite dish deployed on a satellite.
Graphite itself is used for jet and rocket engine nozzles and Carbon/Graphite vanes. Impellers and rotors move aviation fuel safely without the dangers of creating sparks to ignite fuel.
Graphite One Inc. (TSXV:GPH, OTCQX:GPHOF)
Graphite One (TSXV:GPH, OTCQX:GPHOF) plans to invest $435 million to build a graphite anode manufacturing plant in Trumbull County, Ohio, between Cleveland and Pittsburgh.
As Graphite One builds its anode active materials (AAM) production plant, first to accommodate synthetic graphite, then natural graphite from the Graphite Creek mine, the company has the opportunity to make other graphite products. Two possibilities are silicon-blend graphite, where silicon is embedded within a graphite matrix in the anode; and hard carbon, which improves ionic flow and provides higher power densities in batteries.
On July 25, G1 announced it has entered into a non-binding Supply Agreement with Lucid Group, Inc. (NASDAQ: LCID), a California-based electric vehicle manufacturer, for AAM used in EV batteries.
“This is a historic moment for Graphite One, Lucid and North America: the first synthetic graphite Supply Agreement between a U.S. graphite developer and U.S. EV company,” said Anthony Huston, Graphite One’s president and CEO.
“G1 is excited to continue pushing forward developing our 100% U.S. domestic supply chain. We appreciate the support from our investors and the grant from the Department of Defense. Subject to project financing required to build the AAM facility, the Supply Agreement with Lucid puts G1 on the path to produce revenue in 2027, and that’s just the beginning for Graphite One as work to meet market demands and create a secure 100% U.S.-based supply chain for natural and synthetic graphite for U.S. industry and national security.”
The Supply Agreement follows Graphite One’s selection in March 2024 of a site for the company’s proposed AAM facility in Warren, Ohio.
Through its wholly-owned subsidiary, Graphite One Alaska, the Vancouver-based company chose Ohio’s Voltage Valley, entering into a 50-year land-lease agreement on 85 acres. The deal also contains an option to purchase the property once known as the Warren Depot, part of the National Defense Stockpile infrastructure, until the brownfield site was processed through the Ohio EPA Voluntary Action program a decade ago, certifying that the land does not need further cleanup.
Construction is slated to start within the next three years. According to Graphite One, the Voltage Valley site is in the heart of the automobile industry, with ample low-cost electricity produced from renewable energy sources. It is accessible by road and rail, with nearby barging facilities. Existing power lines are sufficient for Graphite One’s Phase 1 production target of 25,000 tonnes per year of battery-ready anode material. Land is available for follow-on phases to ramp up to 100,000 tpy of production.
The five-year, non-binding Supply Agreement provides for 5,000 tpa of synthetic graphite. Sales are based on an agreed price formula linked to future market pricing, as well as satisfying base-case pricing agreeable to both parties.
The Ohio facility represents the second link in Graphite One’s graphite materials supply chain; the first link is Graphite One’s Graphite Creek mine in Alaska, currently working toward completion of its Feasibility Study in Q4 2024, on an accelerated timetable, funded by a $37.5 million Defense Production Act grant from the Department of Defense in July 2023.
Subject to financing, the plant will manufacture synthetic graphite until a natural graphite anode active materials becomes available from the company’s Graphite Creek mine, located near Nome, Alaska, according to the March 20th news release.
The plan also includes a recycling facility to reclaim graphite and other battery materials, to be co-located at the Ohio site, which is the third link in Graphite One’s circular economy strategy.
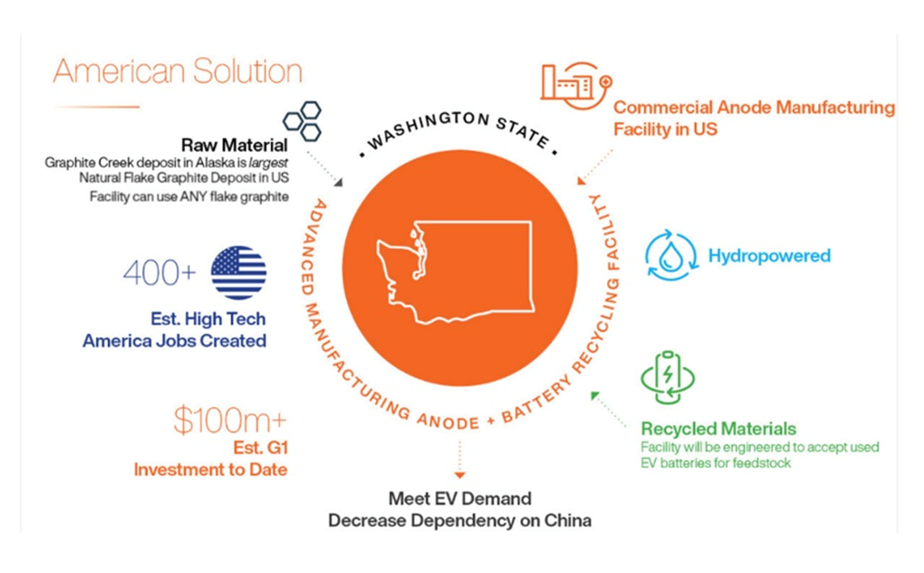
Tie-in with geopolitics
At a recent briefing held at the US Capitol, Dan Sullivan of Alaska, a Republican who sits on the Senate’s armed services committee, reminded the audience of the wider implications of the deal between Graphite One and Lucid.
He described how, the night before, US and Canadian fighter jets had intercepted a combined Russian-Chinese bomber patrol over the Bering Sea, in international airspace close to Alaska. It was the first time those two countries had conducted such a joint drill on North America’s Arctic doorstep.
Bloomberg observes how graphite “is at the center of the tightening convergence between control of critical minerals, the energy transition, and national security.”
Above we pointed out graphite’s many defense applications.
Competing with Chinese graphite producers who have a two-decade head start will neither be easy nor cheap. However, the strategic challenge presented by China, especially in tandem with hostile Russia, cannot be brushed aside, Bloomberg concludes:
Hence, building the US critical minerals and cleantech supply chain necessarily entails a mixture of strategic government backing and private funding to get it off the ground. Disparate as they seem, there’s a direct, and darkening, line between that stand-off in the skies near Alaska and Graphite One’s deal with Lucid, and not only because of the uncanny timing. The transition of our global energy system and the transition to a new era of geopolitical contest are increasingly inseparable.
Conclusion
China is by far the biggest graphite producer at about 80% of global production. It also controls almost all graphite processing, establishing itself as a dominant player in every stage of the supply chain.
(China mines about two-thirds of the world’s natural graphite, controls about 60% of synthetic graphite, and almost 100% of coated spherical graphite used in EV batteries. China also accounts for 98% of announced anode manufacturing capacity expansions through 2030, according to the International Energy Agency.)
The United States currently produces no graphite, and therefore must rely solely on imports to satisfy domestic demand.
Washington has finally begun to recognize this vulnerability.
In 2022, President Biden issued a Presidential Determination under the 1950 Defense Production Act (DPA), declaring graphite and four other key battery minerals at risk of supply disruptions, as “essential to the national defense.”
Graphite is included on a list of 23 critical metals the US Geological Survey has deemed critical to the economy and national security.
The aim of the Defense Production Act is to wrest control of “clean technology” (e.g. EVs, renewables) supply chains from China, which has been building and controlling them for decades.
Graphite One could take a leading role in loosening China’s tight grip on the US graphite market by mining feedstock from its Graphite Creek project in Alaska and shipping it to its planned graphite anode manufacturing plant in Voltage Valley, Ohio. Initially, G1 will produce synthetic graphite and other graphite products from purchased graphite.
Graphite One could supply a significant portion of the graphite demanded by the United States.
Consider: In 2023, the US imported 83,000 tonnes of natural graphite, of which 89% was flake and high-purity, suitable for electric vehicles.
Based on G1’s Prefeasibility Study (PFS), not the Feasibility Study which is expected this fall, the Graphite Creek mine is anticipated to produce, on average, 51,813 tonnes of graphite concentrate per year during its projected 23-year mine life.
Automakers and defense companies have been raising alarm bells over the fact that the United States hasn’t mined any graphite since the 1950s, and even if it had, it would need to be shipped to China for processing. G1 intends to play a large part in correcting this.
The US Energy Department forecasts that global graphite demand could be more than eight times current production by 2035.
Assuming a 60 kilowatt-hour battery, every million EVs requires almost 80,000 tons of graphite. Last year the US imported 73,870 tonnes of flake graphite needed for EVs. Global demand for flake graphite is projected by Benchmark Mineral Intelligence to more than triple by 2030, to 4.1 million tonnes.
Graphite One plans to produce, first, synthetic graphite “with ample low-cost electricity produced from renewable energy sources” and later on, to feed the anode active materials (AAM) plant in Ohio with natural graphite from the Graphite Creek mine.
Its strategy dovetails with the government’s plan to reduce dependence on China for the mining and processing of critical minerals, especially graphite, for which the United States is totally dependent on foreign, namely Chinese sources.
The only way to alleviate import dependence is for the United States to find its own sources of graphite production and manufacturing.
The company’s Prefeasibility Study (PFS) was based on the exploration of only one square kilometer of the 16-km deposit, meaning that G1 could potentially increase production by a factor several times the proposed run rate of 2,860 tonnes per day.
Only about 10% of the mineralized trend has been drilled so far.
Graphite One’s 2024 field program will gather the remaining data required to complete the Feasibility Study, expected in Q4. The company says three drill rigs are currently operating to glean geotechnical information needed to engineer the pit walls and foundations for the process facility, tailings/waste rock facility and other infrastructure.
(By Richard Mills)
Legal Notice/Disclaimer
Ahead of the Herd newsletter, aheadoftheherd.com, hereafter known as AOTH.
Please read the entire Disclaimer carefully before you use this website or read the newsletter. If you do not agree to all the AOTH/Richard Mills Disclaimer, do not access/read this website/newsletter/article, or any of its pages. By reading/using this AOTH/Richard Mills website/newsletter/article, and whether you actually read this Disclaimer, you are deemed to have accepted it.
{{ commodity.name }}
{{ post.title }}
{{ post.date }}
Comments