E-haul trucks could result in major savings for miners but adoption is slow – report
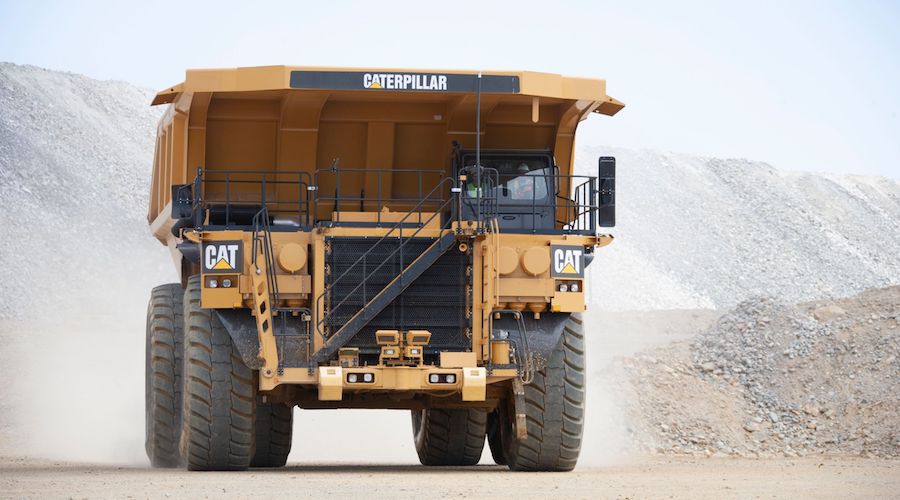
A new report by IDTechEx states that investing in e-haul trucks could result in major savings for miners due to the replacement of diesel with cheaper electricity, as these vehicles have the most intensive duty cycles of any vehicle in a mine.
“A single 150-tonne haul truck can save over $5.5 million in energy costs alone,” the report reads. “This is widely applicable across all vehicle weights, with heavier trucks providing even greater upside, highlighting the potential savings that can be generated when an entire fleet of haul trucks is electrified.”
Yet, the document points out that miners worry about the size and cost of haul truck batteries, as well as about the fact that they will need multiple replacements within a 10-year window.
“The large batteries needed for electric haul trucks have perhaps been the largest technological and financial bottlenecks inhibiting their adoption, but they are now sufficiently developed and competitively priced for wider use. These batteries regularly exceed 1 MWh, with the largest ones approaching 2 MWh,” the report reads.
“IDTechEx has collated a database of all existing EV haul truck models, showing that current vehicle runtimes remain under six hours on a single charge. For a 150-tonne haul truck to operate for this duration, it will require a battery pack of over 1700 kWh and cost over $500,0000.”
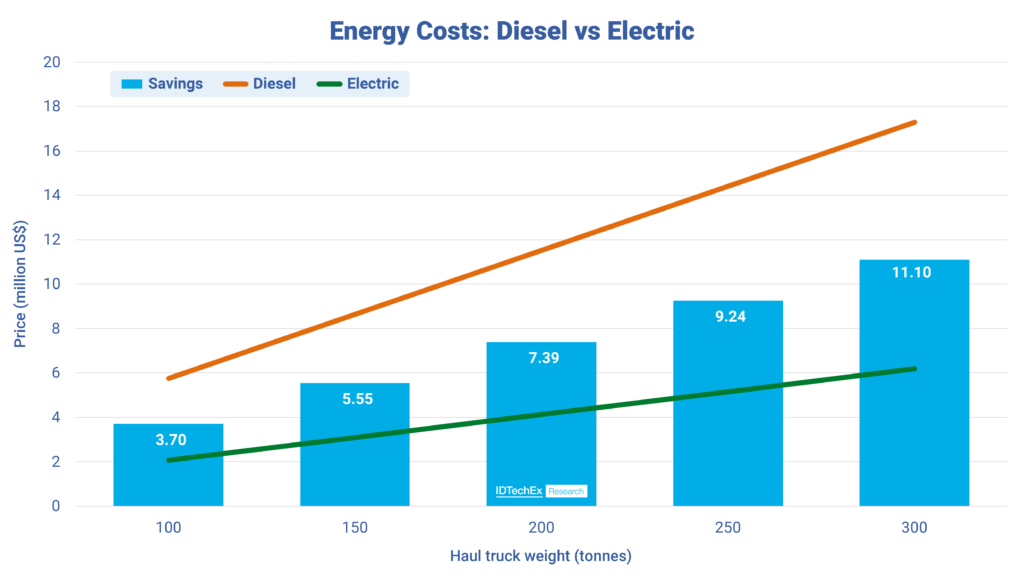
In the market analyst’s view, energy savings will comfortably exceed the added cost of a single battery. However, the firm’s experts forecast electric haul trucks will need an additional five battery replacements per vehicle on average, costing an extra $2.6 million.
“More cost factors also play into the total cost of ownership of electric haul trucks. On average, a 150-tonne truck will be able to save around $340,000 in maintenance costs in its lifetime. However, an electric driveline is needed for $70,000, plus the labour of retrofitting which IDTechEx estimates at $360,000.
While these are relevant and substantial costs, they pale in comparison to the amounts spent on diesel or batteries and are not the key determinants in haul truck economics,” the dossier notes.
The market researcher’s figures show that despite multiple battery replacements, total ownership costs are strongly in favour of electrification as mining companies will be able to save nearly $2.5 million per electrified haul truck, and trucks will break even on their added CAPEX in under three years.
The report also points out that given that the volumes of electric haul trucks are still so small, there is room for the cost of batteries to fall below the estimated $300/kWh.
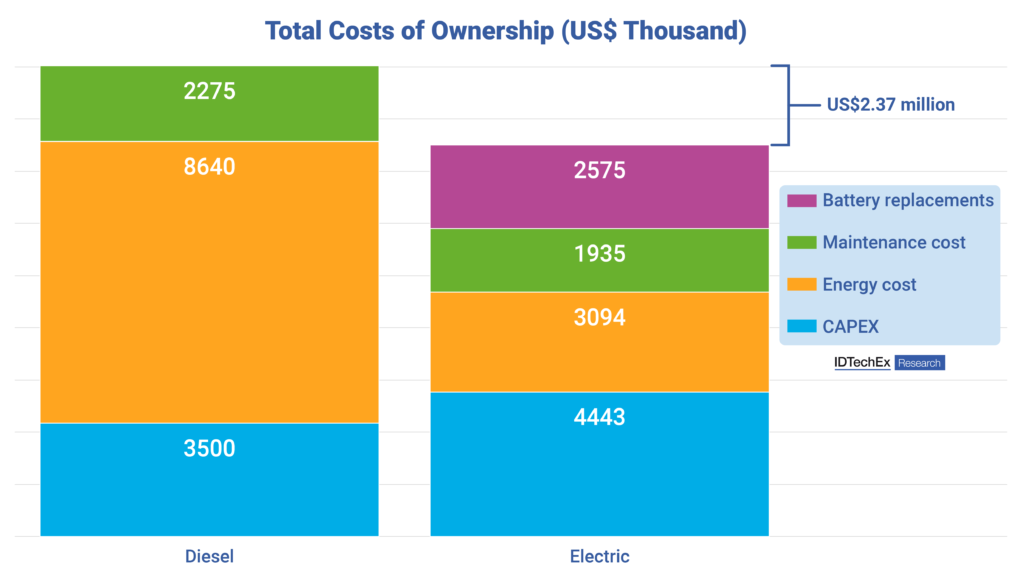
Not there yet
Despite electric haul trucks being cheaper to operate, more productive and environmentally friendlier than existing diesel trucks, IDTechEx’s file notes that haul truck electrification is still in its nascent stages.
“Only one or two electric haul trucks have been made per year, and only in 2023 did the total number of these vehicles tip into the double digits. The majority of these have been prototypes and testing models developed by the mining companies themselves and independent retrofitters instead of OEMs,” the report reads. “They repurpose existing diesel machines to install batteries or fuel cells for zero-emission operation. First Mode and WAE have been the two most active players in this area and are expanding their retrofitting capacities in the near term.”
According to the market researcher, more recently, major mining OEMs such as Caterpillar and Komatsu are seeking to develop and commercialize e-haul trucks, with Caterpillar building the 793 Electric prototype, currently in testing and with aims for commercialization by 2027, and Komatsu developing its 830E electric, aiming for production pre-2030.
“If electric haul trucks are so financially attractive, why are they not yet widespread? First and most importantly, batteries require size and endurance that are in line with the demands of haul truck duty cycles while still maintaining relative affordability.
This aspect has only recently been achievable from battery suppliers such as CATL, ABB, and Northvolt, and the industry is now expanding in response,” the dossier states. “Development of haul truck batteries is in its infancy – a wide range of designs and chemistries are currently being employed to meet performance demands, and there is yet to be an industry-wide consensus.”
For IDTechEx’s analysts, productivity is another sticking point in the adoption of electric haul trucks as currently, an electric truck can’t match the uptime of diesel.
“Where a diesel truck only needs 10 minutes a day to refuel, EVs need to be charged multiple times a day for two to three hours in total. Mining companies will not be willing to adopt a technology if it means sacrificing the productivity and output of their operations,” the report concludes.
{{ commodity.name }}
{{ post.title }}
{{ post.date }}
Comments