Critical minerals and the global supply chain: Challenges and opportunities
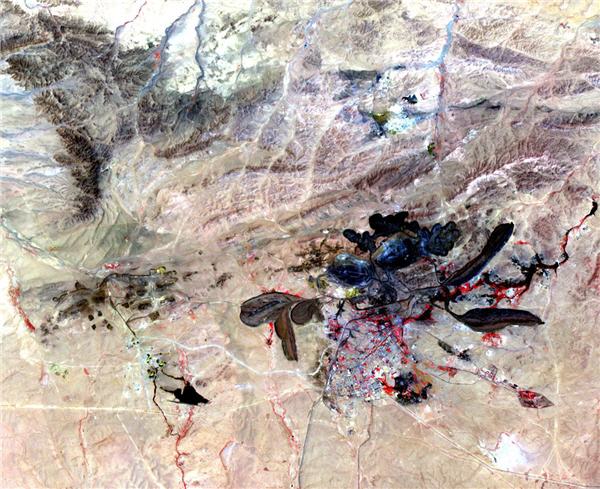
Critical minerals play a key role in advancing emerging technologies, such as electric vehicles and wind turbines. Improving access to these supplies should support a greener future. However, the associated global supply chain includes challenges and opportunities to address.
Concentration of supply
One of the current difficulties with the global supply chain for critical minerals is that too few countries produce most of them. For example, China is the top producer of many critical minerals, along with South Africa and the Democratic Republic of Congo. This concentration of supply could cause significant, rippling effects. For example, if a regional conflict affects one country, manufacturers worldwide could experience associated hardships.
Many countries have begun dedicated plans to increase domestic production, but getting meaningful results will take a while. For example, China produced more than 98% of the world’s gallium as of 2023. However, diversification doesn’t come easily or quickly. The U.S. has only one primary mining site for critical minerals.
Since establishing new mines in the country may take decades, scientists and corporate heads are eager to find secondary or little-known alternative sources. That essential work could reduce the current supply chain strain.
Opportunities also exist to create new technologies that use fewer or no critical minerals. Additionally, people must invest in recycling facilities that can reclaim some of those supplies. One company handles an average of 15,000 battery packs and modules monthly, highlighting the present demand for these services.
Sustainability
Many authority figures insist that companies, countries and individuals make progressively sustainable choices to shrink their carbon footprint. However, a reality that poses challenges and opportunities is that the processes used to obtain critical minerals are not traditionally sustainable. Many workflows must become entirely transformed to meet new emissions targets.
Fortunately, industry decision-makers have many possibilities to consider. For example, diesel suppliers serving industrial clients typically have wide distribution networks to keep their supply chains secure. These arrangements may reduce the overall distance diesel must travel to reach clients, substantially reducing the likelihood that clients will run out of fuel. The latter benefit supports sustainability.
Some mining company leaders are also using advanced data analytics tools to determine the most viable places before launching their extraction efforts. Such approaches are more sustainable because they allow making the most of time and resources without unnecessary harm to the environment. Estimates suggest one in every 100 potential sites becomes a mine. That means precision is an important part of making ongoing improvements.
Another possibility is to apply artificial intelligence to find high-quality ores and reduce mining’s downstream impact. It’ll likely take a while to make such efforts consistently viable. Even so, people must seize these opportunities to see what works well and what options may need further development before people use them in industrial environments.
Analysts warn that the global supply chain needs robust investment to keep pace with expected demands over the coming years. There’s no easy or universally applicable solution to make the necessary progress, but the possibilities explored above are worth further investigation by industry leaders.
(Ellie Gabel is an environmental science writer at Revolutionized)
{{ commodity.name }}
{{ post.title }}
{{ post.date }}
Comments