How an Aussie miner and American tech company plan to extract lithium quickly in Argentina
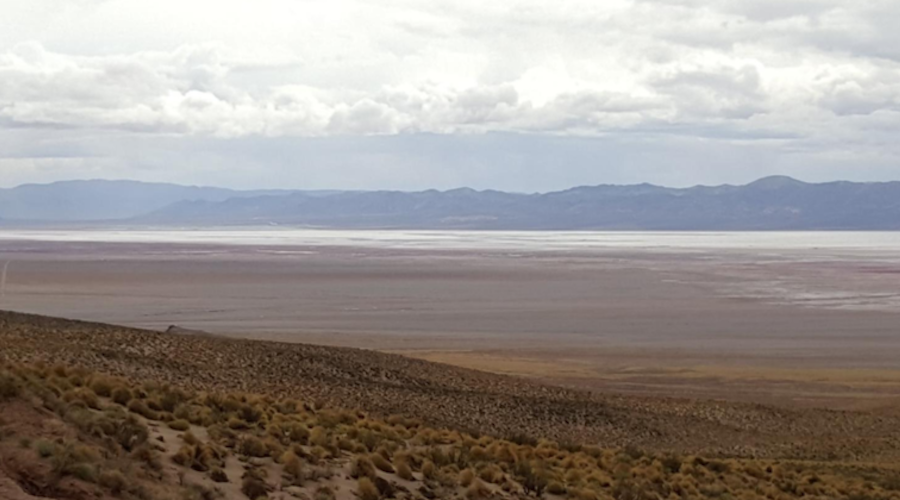
Australia’s Lake Resources NL (ASX: LKE) and America’s Lilac Solutions recently announced that they had established a partnership with the idea of developing the Kachi Lithium Brine Project in Argentina.
Lake owns the project, which is located in the northwestern Catamarca province, some 100 kilometres south of FMC’s Hombre Muerto lithium brine operation. Back in 2017, Kachi received results of over 200 mg/L lithium, recorded from near-surface auger brine sampling. The results maxed out at 204 mg/L lithium. Meanwhile, Lilac is the company in charge of providing its ion exchange technology to produce lithium at the 54,000-hectare site.
What sets this partnership apart is that both the miner and the techie claim they can produce lithium carbonate or lithium chloride more rapidly and at a lower cost than others. According to Lilac, this is possible because its system eliminates the need for sprawling evaporation ponds, which are expensive to build, slow to ramp up, and vulnerable to weather fluctuations.
“Even for the world’s best lithium reserves in the Atacama desert, conventional evaporation ponds take many years to ramp up and remain vulnerable to weather volatility. Lilac’s projects will run at full capacity from year one of commissioning and maintain that output regardless of weather or brine chemistry. We have done benchtop testing in other brines and we saw recoveries over 95% in less than 2 hours versus 9-24 months in evaporation ponds,” the company’s CEO, Dave Snydacker, told MINING.com.
Snydacker explained that the reason why the processes run by his company are so fast is that his engineers have developed ion exchange beads that absorb lithium directly from the brine. Once they do that, the beads are then loaded into ion exchange columns and brine is flowed through such columns. As the brine contacts the beads, the beads absorb the lithium out of the brine. Once the beads are saturated with lithium, the alkali metal is recovered from them as a lithium solution, which is later on processed into battery-grade lithium carbonate or lithium hydroxide using streamlined plant designs.
According to Snydacker, this technology can economically access brines with
low lithium concentrations and high concentrations of other salts, such as magnesium. “With conventional lithium processing, very large quantities of lime and sodium carbonate need to be trucked in to remove magnesium and calcium from the brine. Lilac dramatically decreases the volumes of reagents that need to be trucked in, so we can unlock resources in remote locations. On top of this, our technology is modular so the physical footprint of our facilities is approximately 1,000 times smaller than conventional lithium brine projects using evaporation ponds,” he said.
Lake and Lilac plan to install on-site pilot plants in early 2019 and start commercial production in 2020 with the idea of selling their product to battery companies and affiliated chemical companies producing cathode powders such as NMC, NCA, and LFP.
“We currently have four process engineers working on the Lake project. For the on-site pilot plant next year, we will add three field engineers and three technicians. Each commercial plant will employ dozens of people, and we’re excited to develop positive ties with the communities where we operate,” the executive said.
{{ commodity.name }}
{{ post.title }}
{{ post.date }}
Comments
Stu Crow
Great article except for typo, grade has been report at 204 instead of actual 304mg/l as reported to ASX but simply means recovered Lithium will be greater!