AI & digital twins for mining explained
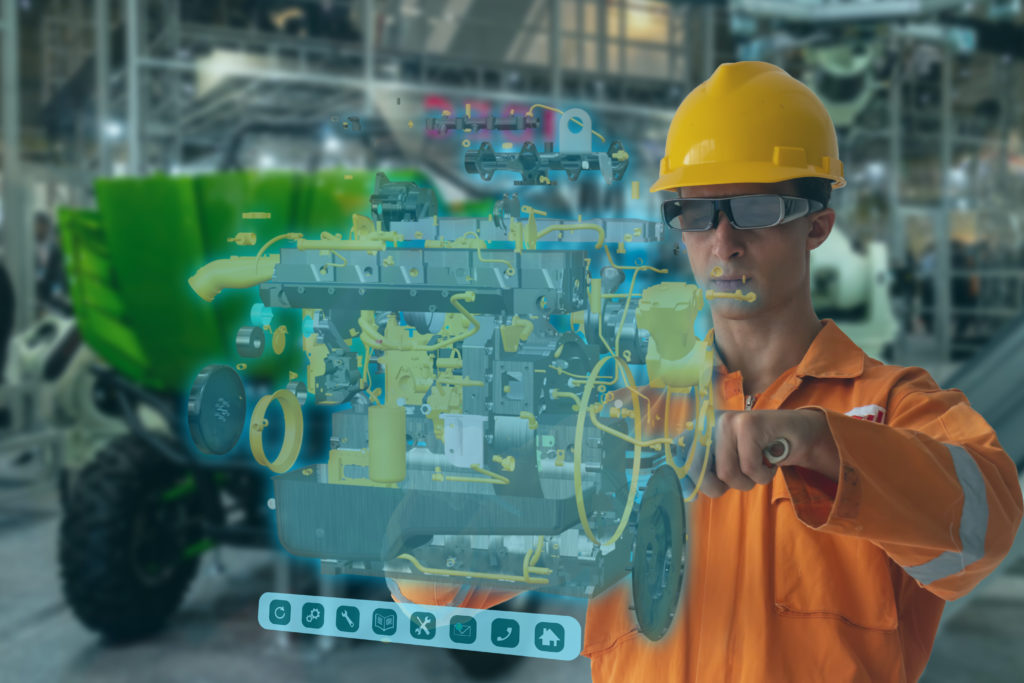
Artificial intelligence (AI) has exploded onto the public stage in 2023, but behind the scenes, many organisations have been quietly trialling and implementing AI for years on a variety of use cases. In mining, AI is becoming a common pilot or trial offering at many tier 1 and 2 miners, but has yet to revolutionise how we operate.
AI is still a misunderstood technology. The common interpretation of AI is “a computer as smart as a person” – but this is not AI in 2023, and the people creating AIs are creating them to solve specific problems, not to emulate humans. AI is used in 2 broad ways: to make predictions, or to optimise existing processes.
AI for mining
In mining, AI is beginning to surface across the value chain. While specific applications vary considerably, the general class of problem found in each area of the value chain can be easily understood. Finding economic resources in the noise of thousands of old survey and drill results is a prediction problem; we need to make a prediction about where a substantial body may be, and then act on that prediction to test it. The test results feed back to improve the next prediction. Scheduling haul trucks in a pit is an optimisation problem; we want to minimise idle time and maximise throughput for a fleet on a given day, and we have various fixed and variable factors.
Some of the key areas of the value chain where AI is present in 2023:
- Exploration (prediction)
- Mining (optimisation)
- Processing (optimisation)
- Maintenance (prediction)
- Safety (prediction)
- ESG (optimisation)
Digital twins
Digital Twins (Twins) mirror some part of the real world in software, so that we can analyse and manipulate data and make changes back in the real world. What’s different about this from what we do today? Today, we have many systems that do different things, and many humans that do different things, and when something goes wrong, humans look inside their siloed systems to gather data on what to do. The problem is that every human might be seeing different data from maintenance, control, and planning systems, and some are on site looking at the problem and using their eyes and ears to diagnose the problem, and others are 1000s of kms away imagining the problem. Each human is seeing a different part of the problem, in a different way.
Digital twins create clarity and context by creating a single picture of the problem, where all humans can see the same data (from many systems) in the same way. Decisions are improved, because maintenance can see control data, and planning can see engineering data, and they can all see when data conflicts. Decisions enacted through a twin then flow back into systems and create change in the real world, which is then reflected in the twin.
Digital twins for mining
In the mining world, there are 2 main classes of twin that reflect the industry: asset twins, and process twins. Mining has many large and complex assets, and mining is a process driven industry, both business processes and physical and chemical processing of ore, by assets. Both assets and processes rely on work; work (e.g. maintenance, planning, upgrades) is done on them and changes them, and both do work and are changed by that work. Thus any twin in mining must address asset, process and work data to create clarity and context.
A SAG mill twin is an example: the asset twin would focus on the machinery, temperature and vibration, power draw, maintenance performed and planned, engineer data. The process twin would focus on grinding efficiency, consumables use, input and output flows. The twins may be used for very different purposes, but they are clearly inextricably linked, as in the real world where separating material flow from the shell liner would be non-sensical.
Twins and AI
What do these 2 technology categories have in common? They both seek to improve decisions. AI optimises and predicts; Twins provide clarity and context. Bringing them together gives decision makers clarity and context into optimisations and predictions of assets, processes and work. AI provides the ability to improve some decisions, and to learn how to improve further; Twins enable humans to compare AI predictions and optimisations against the rules based systems and processes that we use every day.
As AI grows, in performance and across use cases, the ratio of predictions to rules will change, and the instances of predictions violating rules will increase. Groups of humans will need clarity and context about the problem to resolve these conflicts, and to enable the predictions and optimisations to be enacted without negative consequences. AI and Digital Twins are growing quickly in maturity and proving themselves across varied and specific mining use cases.
As the power of predictions and optimisations of specific metrics grows, so too will the expectations that these insights will be used to improve overall mine operating metrics. In most cases, this will require functions to collaborate closely to understand the changes to rule based business processes, and the impacts of changes to processes, work and assets.
AI has the potential to change how we make decisions entirely, but some decisions will remain in the hands of humans for many decades, and our industry needs to find the right mix of machine and human at the site and individual level. Digital twins provide a method for tying people, processes and technology together at the site level, and managing these transitions in structured, risk adjusted ways.
(Rob Foster is CEO at Geminum, a technology solutions provider to the mining industry)
{{ commodity.name }}
{{ post.title }}
{{ post.date }}
Comments