On Diamonds, Mining and Incident Management
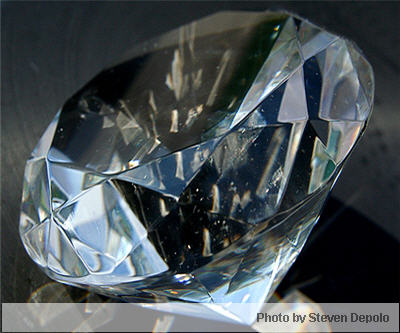
The diamond sparkled in the soft light of a restaurant candle, its allure accentuated by the heady aroma of deep red wine. Yet it looked incongruous in her nose: more a symbol of defiance than of beauty.
“It is a Canadian diamond,” she said. “Straight from the kimberlite of the Northwest Territories. Not tainted by blood or the heart of darkness.”
There had been an incident involving jewellery on the mine we were to visit the next day and I had to advise her to remove the diamond before we entered the mine. Then I explained to this young engineer what incident control involves in a well managed mine.
I told her of my first encounter with incident management. I was excavating a test pit into the cover of an old landfill. The landfill rose some 300 feet above a busy freeway leading east from Los Angeles. The slopes were steep: one and a half horizontal to one vertical. We dug a neat pit and put the excavated soil in a pile on the slope beside the pit.
Some time into the excavation process, a clod tumbled off the waste pile, rolled and bounced down the slope, jumped the perimeter fence and went onto the freeway to splatter on the side of a passing car. The driver must have received a shock, but drove on in the busy stream of traffic with a big, brown splotch on his right-hand side door.
I mentioned this incident in passing at the technical review meeting that evening. The project manager, well trained in incident control, immediately tagged this event as an incident worthy of investigation. There was no blame directed toward me, no retribution to anybody, but it was an event to be considered. He assembled a neutral team that included the health and safety officer and the community relations specialist. They went through the sequence of events carefully, evaluated root causes and potential really serious consequences and considered methods to avoid a repeat — or worse.
The upshot included these recommendations that were implemented throughout the remainder of the project:
• Place test pit spoil on a flat bench if possible;
• Place test pit soil upgradient of the test pit so that clods
rolling down enter the test pit;
• Install a plywood barrier along and above the perimeter fence to preclude any object falling or rolling down the slope from entering the freeway. This cost upward of a million dollars to install, and
• Train all site staff in incident control and teach employees to recognize incidents to be reported and controlled.
By the end of the project, two years later, the plywood was sun-bleached and tatty. But it had stopped a few mishandled objects leaving the site. No driver ever again received a shock from from a passing clod. I was trained in incident control and made a believer in the process. So let me continue.
Recent Event/Incident
An incident can be defined as a small event that is a bit out of the ordinary. It is a small deviation from the planned, expected or desired but, nevertheless, a hint of far worse things that could happen.
Incidents should be managed in order to improve the system so that big, bad events are precluded. The U.S. Occupational Safety & Health Administration (OSHA) defines and summarizes how to deal with mining-related incidents accordingly:
“Accident/incident investigation is another tool for uncovering hazards that were missed earlier or that slipped by the planned controls. But it is only useful when the process is positive and focuses on finding the root cause, not someone to blame!
“All accidents and incidents should be investigated. “Near misses” are considered incidents because, given a slight change in time or position, injury or damage could have occurred;
“Six key questions should be answered in the accident investigation and report: who, what, when, where, why and how. Thorough interviews with everyone involved are necessary;
“The primary purpose of the accident/incident investigation is to prevent future occurrences. Therefore, the results of the investigation should be used to initiate corrective action.”
The Pennsylvania Bureau of Mine Safety, in turn, considers as “incidents” more serious problems, such as: the death of an individual at a mine; an injury to an individual at a mine that has a reasonable potential to cause death and/or serious injuries resulting in the injured being admitted to a hospital, excluding sprains and strains; an unplanned mine fire requiring more than five minutes to extinguish, and an event at a mine which causes death or bodily injury to an individual not at the mine at the time the event occurs, among others.
Regardless of the definition given to the term “incident,” these events need to be properly managed. In the book Mine Health and Safety Management, edited by Michael Karmis, there is a useful chapter on the principles and implementation details of incident management in the health and safety field of mining.
In a mere ten pages, Douglas Martin and H.L. Boling write of Mine Incident Reporting and Analysis, explaining that established procedures for evaluating causes of incidents should be in place at all companies and organizations. They add that incident analysis should be followed by the implementation of controls to prevent future similar occurrences and that comprehensive procedures should also include the analysis of near incidents.
“Potential causes can be controlled before an incident occurs. All incidents that result in fatalities or serious injuries to more than one person should have the analysis conducted under the direction of corporate safety and with legal advice,”say Martin and Boling.
Clearly they extend the scope of incident analysis to fatalities. The principles, however, remain the same: Incident analysis should always be conducted as a fact-finding mission, not a fault-finding one.
Industry Practice
Barrick has an incident investigation program, which it justifies by saying that along with health programs, safety education, risk assessments and regular safety inspections, incident investigation and analysis can be used as a tool to bring us closer to the goal of having “every employee go home in good health and uninjured, after every shift, each and every day.”
The Rio Tinto Incident Management Standard Operating Procedure is another good example of a well designed plan. It is a detailed and integrated document for the management of health, safety, the environment and quality performance, applicable in the mining industry world-wide.
BHP’s Incident Notification and Reporting is also worth a thorough reading.
In summary, the essence of workplace H&S is that the individual is responsible for his or her own health and safety. The company, big or small, is responsible for providing the systems, training and equipment to enable that individual to work in a safe and healthy manner.
* Jack Caldwell is a mining industry commentator who blogs
at ithinkmining.com
Links and References
Click here for full list of links:
{{ commodity.name }}
{{ post.title }}
{{ post.date }}
Comments