Li-Metal produces first batch of lithium metal ingots from scrap
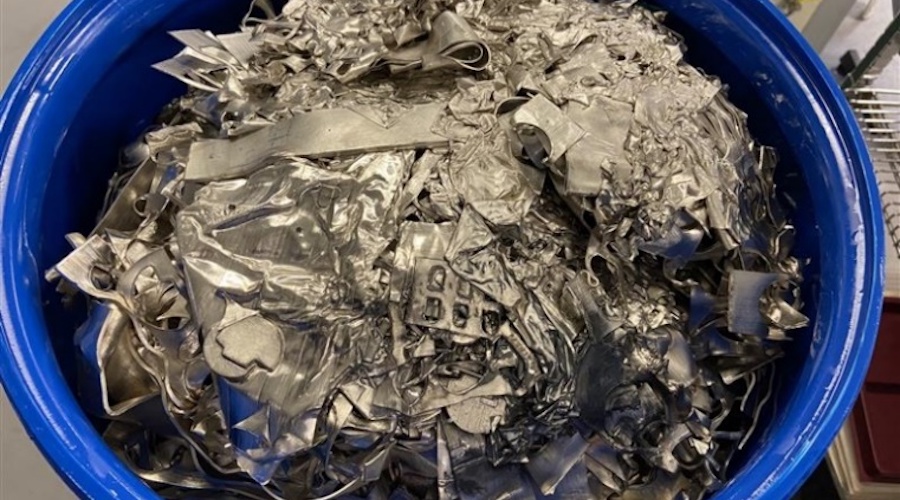
Ontario-based Li-Metal Corp. (CSE: LIM) announced the successful production and shipment of its first batch of lithium metal ingots, which were manufactured at the company’s recently commissioned reprocessing and casting facility in Markham.
The facility has the capacity to process up to 15 metric tonnes of anode scrap material per year using Li-Metal’s reprocessing and casting technology, which reconfigures scrap lithium from sources such as lithium foil producers into ingots that may be used for anode production.
“Lithium metal anodes are produced either through a conventional extrusion/rolling or through more economically viable physical vapour deposition (PVD) processes, the commercialization of which Li-Metal is championing in conjunction with its exclusive manufacturing partner, Mustang Vacuum Systems,” the company said in a media statement.
“Traditional extrusion processes require the lithium metal to be supplied in ingot form. On average, production scrap generated by gigafactories can have up to a 30% metal scrap rate. Lithium metal ingot manufacturing scraps are currently designated as hazardous waste and, typically, incinerated whereby valuable, critical battery materials are lost forever.”
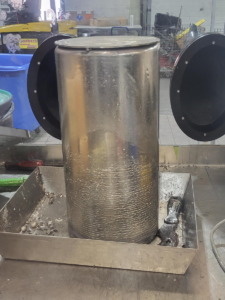
Li-Metal said that it expects to eventually leverage the pilot facility and know-how generated during the scale-up of the reprocessing facility to help its potential partners produce high-purity specialty lithium-alloy ingots for advanced battery producers.
“We are thrilled to produce our first batch of lithium metal ingots using our reprocessing and casting technology and commission our new facility in Markham,” Srini Godavarthy, CEO of Li-Metal, said in the brief.
“The ability to produce lithium metal products is a key differentiator for Li-Metal’s positioning in the next-generation battery ecosystem, further enabling the growth and development of our business. This is an important milestone in our roadmap as we advance our technologies and plan to become a leading vertically integrated and domestic supplier of lithium metal and high-performance anode materials.”
Godavarthy pointed out that earlier this year, Li-Metal also successfully produced its first lithium metal product using its patented carbonate-to-metal (C2M) technology, which is designed to produce high-quality lithium metal ingots with the lowest environmental footprint possible.
“The additional capabilities to produce lithium metal ingots from scrap allow for diversity of raw material supply, which is critical as the company continues to advance its C2M metal technology and its ultra-thin lithium metal anodes platform,” the executive said.
More News
Capital signs civil works, tailings contract with Reko Diq
The contract will run through December 2028 and is expected to generate over $60 million in annual revenue.
April 02, 2025 | 03:31 pm
PDAC video: Energy Fuels produces rare earths using fast process, CEO says
The company made on-spec neodymium-praseodymium in less than a week at its White Mesa uranium mill.
April 02, 2025 | 12:52 pm
{{ commodity.name }}
{{ post.title }}
{{ post.excerpt }}
{{ post.date }}
Comments