Mining Operations Around the World Employ Continuous Surface Mining Methods
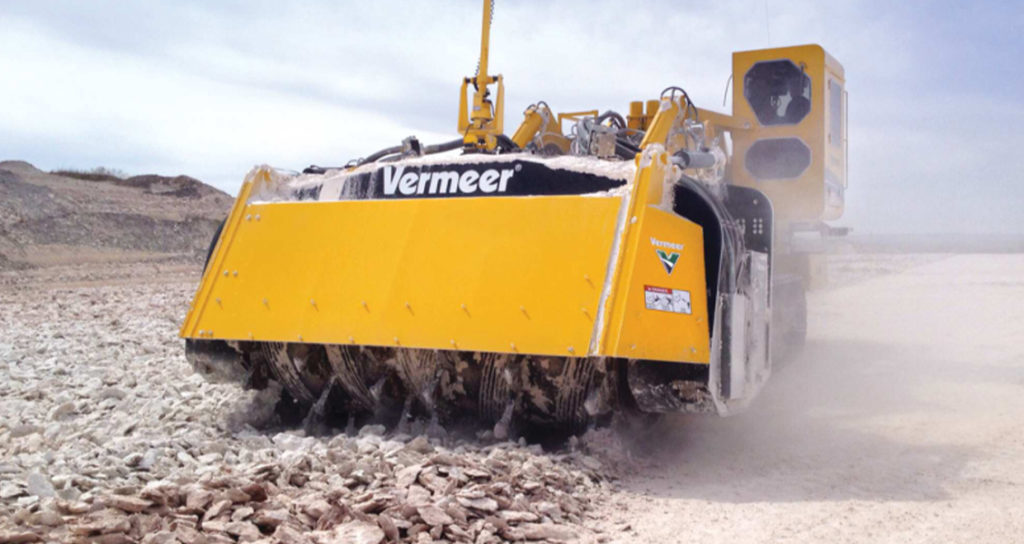
Mining plays a vital role in everyone’s daily lives. The material extracted by surface mining operations creates energy and is used by manufacturers to develop machinery, technology and the infrastructure people use every day. Through continuous surface mining methods, today’s miners are actively taking steps to make mines safer, more sustainable and better neighbors to nearby communities.
Continuous surfacing mining is proving to be efficient and more sustainable for many mines. Using surface excavation machines equipped with powerful cutting wheels to break up hard, rocky material often requires fewer steps than drill and blast methods. Continuous mining methods can also significantly reduce the material handling time at many mines. Material can be extracted a layer at a time, and the process produces consistently sized material that typically does not need to be run through a crusher.
Today, surface excavation machines (SEMs) are working at mines ranging from precious minerals and stones to quarry operations. For many of the mines using continuous surface mining methods, equipment like the Vermeer® Terrain Leveler® SEM has made it possible to extract material in areas deemed “off-limits” for traditional drill and blast mining due to increased regulations and community pressures to reduce noise, vibration and dust.
DIAMOND MINING IN NAMIBIA, AFRICA
Oranjemund, Namibia, is a diamond mining town on the northern bank of the Orange River. Having crossed most of southern Africa on its journey to the sea, the Orange River is rich in minerals where it meets the ocean. At the river’s mouth, the current slows, and the rocky fragments settle out. The tide then drives the sediment up against the coast, forming banks of sand and gravel. And, in amongst the deposits, there are diamonds.
However, retrieving the gems is far from straightforward for Namdeb, the public-private partnership that operates the mine. Because a lot of the sediments are ordinarily underwater, extraction involves creating seawalls beyond the natural coastline and draining the sandbanks behind them. Millions of tons of gravel then need to be extracted and taken inland for processing.
Although it sounds simple, gravel extraction is a challenging process. The beach-like surface sediment hides a sculpted maze of bedrock with hollows and gullies several meters deep, and those hollows and gullies are filled with diamond-bearing deposits Namdeb wants to retrieve. For years, the procedure involved removing the surface gravels down to the first bedrock outcrops. Teams of workers were then deployed to empty the gullies using vacuum extractors – slow, labor-intensive work.
Looking for a mechanized solution, Namdeb invited tenders. “We had four objectives,” explained Namdeb’s project manager. “First, to improve the safety of the workforce. With the old mining method, there was too much risk of people slipping and falling, breaking arms and legs. Second, we wanted to improve surveillance. A person who spots a diamond while they’re out of sight down a gulley is obviously going to be tempted. The third thing we were thinking was that if we took the whole surface off, rock and all, we could use the oversized material — the big lumps of solid rock — for seawall construction. Number four, we saw mechanization as a way of increasing the clearance rate. The viability of an operation like this depends on efficiency: When you’re extracting and processing tons of sediment for very few carats of diamond, you’ve got to work efficiently to make it pay.”
Responding to the call, Vermeer proposed the use of a T1255III Terrain Leveler SEM. A new approach was envisaged, where bulldozers would first strip each newly drained block of ground. The Vermeer machine would then be brought onto the flattened site. It would proceed to cut layer after layer from the surface until the bedrock-to-gravel ratio made continuation uneconomical.
“We knew that the T1255III with single-sided direct drive would be ideal for the job,” recalled Frank Beerthuis, managing director for the Vermeer dealership in South Africa. “In looks, it’s not dissimilar to a common rotating milling machine. However, its unique crawler-tracked design, combined with the direct-drive technology, made the T1255III the best fit for the job. Most machines used in surface mining have a lot of high-wear mechanical drive components — things such as gearboxes, chains and sprockets.
Being a direct drive, the T1255III doesn’t have anything like that. As a result, it’s reliable and more than capable of chewing its way through the mix of bedrock and gravelly sediment on the Namibian coastal site.”
A year from its initial deployment, the machine is in continuous use, the linchpin of a highly efficient extraction operation. Diamond mining is expected to continue at Oranjemund for some years to come. Then, once the viable deposits have been extracted, Namdeb will breach the seawall and return the site to the ocean. In another generation, the area will simply be another part of Namibia’s precious wilderness, with no sign of the sophisticated operations enabled by sector-leading engineering from Vermeer.
IODINE/NITRATES MINING IN CHILE, SOUTH AMERICA
A prominent mine in Iquique, Chile, also started using continuous surface mining methods in 2017. The mine had a goal of taking a broader approach and evaluating the benefits of continuous surface mining from pit to heap leach. Results have been measured and compared with traditional drill and blast methods, and after almost 3” million metric tonnes (3.3 million t) of material cut, the benefits are sound and clear. The mining operation has reported positive results in the areas of material separation, more consistent particle sizes and gains in the heap leaching process.
According to César Leite, Vermeer regional manager for Chile and specialty excavation, “Continuous surface mining has helped dilution issues because of the way the Terrain Leveler SEM cuts material in layers.” Leite continued, “With a modulable cutting depth, miners can be highly selective in the way they recover the mining ore with minimum presence – if any – of sterile material. Geological mapping of the pit can result in less dilution. It can help improve efficiencies through the whole process from loading and hauling of rich and concentrated mineral ore to a heap leaching process with a high level of mineral recovery.”
The effectiveness of the leaching process can be affected by the direct particle size output of the blasting stage. In normal conditions, blasting is simply not able to control or guarantee a consistent particle size. Inconsistent particle sizing can result in poor recovery during heap leaching stages. With continuous surface mining, there is a high level of consistency in particle sizes, resulting in better mineral recovery in later heap leaching stages. On top of that, avoiding big chunks of rocks – very common in blasting – increases the hauling process’s efficiency as more material is transported in a given spatial volume.
Around 95% of the material cut with the Terrain Leveler SEM produced particle sizes below 25.4 centimeters (10 in) at the Iquique mine. The results of mineral recovery created by continuous surface mining with the Terrain Leveler SEM showed 12% more mineral recovery than heaps with traditional mining. This mineral recovery rate was also achieved in a period 33% shorter than using traditional mining methods.
QUARRY MINING IN SWITZERLAND, EUROPE
For more than 125 years, Switzerland’s Jura Cement, a subsidiary of CRH plc, has served as a manufacturer and supplier of building materials. However, mounting community pressure regarding dust emissions, vibration and noise threaten the company’s future at its largest quarry operations. To address these concerns, Jura Cement is implementing new precision surface mining methods to help secure the quarries’ future.
Comprised of two production plants, Jura Cement produces more than 1 million metric tonnes (1.1 million t) of cement per annum. The bulk of its annual production is mined at its quarry operations in Wildegg, which first opened in 1891. There was nothing but open land around the quarry in those early days, but as the mine and surrounding community have expanded, the bordering area between the two has continued to shrink.
There are now residential areas surrounding three sides of Jura Cement’s Wildegg facility, as well as a growing concern from local inhabitants about how the mining operation extracts limestone for the quarry. To address these concerns, quarry officials conducted an internal investigation several years ago to determine how they can be better neighbors to the community while producing the materials their customers need.
“Based on our findings, it was determined that we needed to lower blasting-induced ground vibrations, which were already relatively low, to ease the concerns raised by the surrounding community,” explained Marcel Bieri, manager of cement production for Jura Cement. “Our search for alternative mining methods started in 2012, and since then, we’ve explored several mining techniques, including rock excavation using a hydraulic excavator, ripping material with dozers and specialized surface excavation machinery. Based on our findings, using SEMs is the most efficient mining method among those we tested.”
The team at Jura Cement brought in a Vermeer T1255III single-sided direct drive with an optional dust suppression system to help address concerns about dust emissions. The unit also incorporated Vermeer SmartTEC performance software to aid with control adjustments and recording machine productivity, Vermeer Telematics to monitor and track fuel consumption and hours, and a full-function remote control.
During an initial trial period, the Jura Cement team paid close attention to production rates, machine operational costs, service support and operator feedback.
The Terrain Leveler SEM achieved an average production cutting efficiency of 250 metric tonnes (275.6 t) per hour while working in soft-to-medium rock up to 80 megapascals (11,603 psi) at Jura Cement jobsites. With a fuel consumption average of 70.9 liters (18.2 gal) per hour and normal preventive maintenance expenses, Jura Cement’s operational costs fall in line with other drilling and blasting methods when working in soft and heavily ragged rock.
“The Terrain Leveler SEM also allowed work close to the edge of the cut, and a lower center of gravity provided stability on uneven terrain,” said Andreas Kofler, project supervisor for Jura Cement’s Wildegg quarry. “Our operators also appreciated all of the assisting tools built into the Terrain Leveler SEM.”
“At the conclusion of our trial rental period, we evaluated all of the results and chose to extend our rental agreement for the Terrain Leveler SEM,” said Kofler.
The strides made with continuous surface mining methods have helped Jura Cement earn community officials’ and residents’ trust and respect. They can see that Jura Cement is taking their concerns seriously and are taking the necessary steps to verify that the quarry can remain open and continue to expand in the future.
FUTURE OF SURFACE MINING
Developing more sustainable mining practices and mitigating the safety risks associated with drilling and blasting has surface mining operations worldwide turning to continuous surface mining methods.
This article contains third-party observations, advice or experiences that do not necessarily reflect the opinions of Vermeer Corporation, its affiliates or its dealers. Testimonials and/or endorsements by contractors in specific circumstances may not be representative of normal circumstances experienced by all customers.
Vermeer Corporation reserves the right to make changes in engineering, design and specifications; add improvements; or discontinue manufacturing at any time without notice or obligation. Equipment shown is for illustrative purposes only and may display optional accessories or components specific to their global region. Please contact your local Vermeer dealer for more information on machine specifications.
6 Comments
Hermanus Silver
I would like to know if one gets different drum sizes for smaller bench mining.
Also, the availability of such a cutter and delivery time, if possible I would also like a quote to purchase or rent one in Namibia for Diamond mining near the Orange river and Copper mining.
shamit varma
we can help you rent or purchase a surface miner, we operate one in kenya.
Roy Shantika
I am an adt operator and a mine health and safety certificate holder. Any company to employ me am ready
Albert Barfo
There are some opportunity in the mining sector that can employ 1 3rd of the world population. And it is an example here for others to do more.
Nasarullah Khan
I want to know weather SEM is suitable for Copper mining in Balochistan Pakistan near Richodic
Habdul Moahmed
There are other supplier of surface miner like Tesmec that are very very reliable