Four charts show why cobalt supply is tightening
[Editor’s note: Adapted from recent McKinsey report, The Future of Nickel: A Class Act]
Lithium batteries have a variety of blends that entail many improvements and trade-offs.
The EV industry developed the NMC mix, which has less cobalt than lithium-cobalt-oxide batteries (LCO), commonly used in the portable electronic industry.
NMC chemistry is evolving with a shift from the relatively cobalt-rich NMC111 to the NMC811 cathode configuration, partly driven by the higher energy density of the 811. An even bigger factor in the move to the 811 configuration is the limited cobalt supply.According to the United States Geological Survey (USGS) approximately 123 KT of cobalt was mined in 2016, and the organization projects insufficient supply to meet demand in 2017.
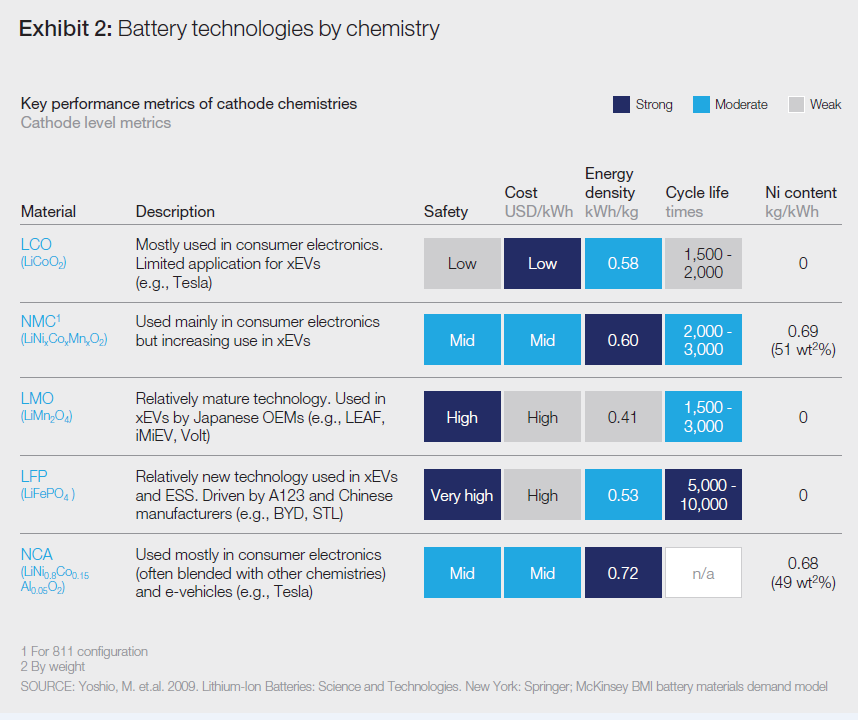
Exhibit from “The Future of Nickel: A Class Act”, November 2017, McKinsey & Company, www.mckinsey.com. Copyright (c) 2017 McKinsey & Company. All rights reserved. Reprinted by permission.
At present, approximately 30 percent of annual cobalt use is in a variety of technical applications, including material used for EV batteries. This segment is expected to increase rapidly, with demand likely outstripping supply. The result has been a rapid price increase, from USD 20,000 per metric ton tin January 2016 to over USD 60,0000 per metric ton in September 2017.

Exhibit from “The Future of Nickel: A Class Act”, November 2017, McKinsey & Company, www.mckinsey.com. Copyright (c) 2017 McKinsey & Company. All rights reserved. Reprinted by permission.
Constraint in supply are likely to persist. Approximately 60 percent of cobalt production comes from the Democratic Republic of the Congo, which present both operating and reputation risks from mining companies. Additionally, cobalt is rarely found in high concentrations and is mostly produced as a byproduct of copper and nickel. Limited new investment in these two commodities and only increase supply challenge for cobalt.
Consequently, cobalt supply constraints are likely to curb the growth of cobalt rich battery technology, including NCAS and NCM. For now, manufacturers of these high capacity batteries are trying to reduce the percentage of cobalt content by increasing the amount of nickel sulfate used. For example, the 622 battery (two parts cobalt per six parts nickel) used in a number of European EV battery application may be replaced soon by an 811 chemistry with only one part cobalt and eight parts nickel.

Exhibit from “The Future of Nickel: A Class Act”, November 2017, McKinsey & Company, www.mckinsey.com. Copyright (c) 2017 McKinsey & Company. All rights reserved. Reprinted by permission.

Exhibit from “The Future of Nickel: A Class Act”, November 2017, McKinsey & Company, www.mckinsey.com. Copyright (c) 2017 McKinsey & Company. All rights reserved. Reprinted by permission.
Creative Commons image by DVIDSHUB
More News
Chile to cut 2025 copper price forecast, WSJ reports
The Chilean government will cut the estimated average price to $3.90 to $4 a pound from a current projection of $4.25.
April 06, 2025 | 10:49 am
Breakthrough Cu-Ta-Li alloy could transform aerospace, defense applications, researchers say
US Army Research Laboratory developed nanostructured copper alloy with exceptional thermal stability and mechanical strength.
April 04, 2025 | 04:17 pm
{{ commodity.name }}
{{ post.title }}
{{ post.excerpt }}
{{ post.date }}
Comments